Twoim problemem jest to, że powszechną NICOŚĆ mylisz z osobistą PUSTKĄ
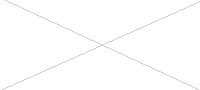
Wyk6 maszyny
Sprężarka maszyna przepływowa, której zadaniem jest podwyższenie ciśnienia lub wymuszenie jego przepływu. Zastosowanie: tam gdzie chodzi o zmniejszenie objętości (zwiększenie gęstości) czynnika gazowego, podniesienie ciśnienia tgo czynnika, wymuszenie przepływu, podwyższenie temperatury czynnika gazowego. Najczęściej spręza się: powietrze, azot, amoniak, wodór, SO2, CO2. ze względu na budowę mamy: wyporowe (tłokowe, rotacyjne), wirowe (odśrodkowe i osiowe), specjalne (strumienice). Ze względu na różnicę ciśnień na wylocie i wlocie(p2/p1) wyróżniamy: wentylatory – 1-1,1- zwiększaja ciśnienie o około 20%, dmuchawy – 1,1-3 – zasysają czynnik o cisnieniu otoczenia i sprężają do około 1,2 – 3 bar, sprężarki właściwe, kompresory – 3-1000 (nadaja czynnikoi ciśnienie 3-2000 bar) W sprężarce ciśnienie ssawne jest nieznacznie niższe od ciśnienia atmosferycznego (tak aby zachować zdolność ssania), zaś ciśnienie tłoczone jest znacznie wyższe od atmosferycznego. Sprężarki gdzie ciśnienie ssawne jest znacznie niższe a tłoczone nieznacznie wyższe od ciśnienia atmosferycznego nazywamy pompami próżniowymi. Spręż>6 uzyskujemy przez wielokrotne sprężanie. Sprężarki wydzielaja w czasie pracy dużo ciepła. Spręzarka służy jako napęd różnych narzędzi np. szlifierka, klucz pneumatyczny, wiertarka, młot; rozpylania cieczy; dystrybucja gazów technicznych; pompowanie opon samochodowych; podnoszenie ciśnienia w ukl turbin gazowych;doładowanie silnika spalinowego; transport materiałów sypkich; instalacje chłodnicze i zamrażalnicze; klimatyzacja; dosp domowe – chłodziarka, wentylator, odkurzacz, suszarka). Do uzyskania wyskich ciśnień potrzebna duża energia ponieważ gaz jest ściśliwy. Cykle pracy sprężarki 1. ssanie – ruch tłoka od martwego polożenia( w którym dotyka cylindra);otwarty zawór ssący; ciśnienie wewnątrz cylindra jest stale i równe ciśnieniu przestrzeni z której zasysany jest gaz. 2. sprężanie powrotny ruch tłoka, wzrost ciśnienia zamkniętego w cylindrze gazu aż do ciśnienia panującego w przewodzie tłocznym; przemiana adiabatyczna zamknięta(cylinder zaizolowany, obydwa zawory zamknięte) 3 tłoczenie – tłok wytłacz przez otwarty zawór tłoczny gaz z cylindra; ciśnienie wewnątrz cylindra jest stałe i równe ciśnieniu panującemu w przewodzie tłocznym. Spręzarka z chłodzeniem cylindra – chłodzenie zapobiega podnoszeniu się temp gazu podczas sprężania, praca włożona podczas sprężania izotermicznego jest mniejsza, ciśnienie gazu takie jak w sprężarce adiabatycznej, ale temp gazu niższa. Sprężarka wielostopniowa z chłodzeniem wielostopniowym – gaz chłodzi się między stopniami w chłodnicach, gaz zostaje zassany, sprężony adiabatycznie, wytłoczony do chłodnicy i ochłodzony. Podczas chłodzenia zmniejsza się jego objętość, następnie zostaje zassany do drugiego cylindra, sprężony adiabatycznie, wytłoczony, schłodzony izobarycznie, zassany do cylindra trzeciego. Sprężarka tłokowa jednostopniowa – tłok sprężarki w martwym położeniu nie może dochodzić do dna sprężarki, pozostawiona objętość to objętośc szkodliwa. Sprężarka zasysa mniejszą ilść gazu, gdyż przemiana ssania poprzedzona jest przemianą rozprężania gazu w przestrzeni szkodliwej. Wydajność sprężarki Qrz=λnV λ- wsp napełnienia, n- stosunek między objętością rzeczywiście zassana a objętością skokową. Liczba stopni spręż nie przekracza 6, przy wyższej konstrukcja komplikuje się, a zysk z każdego stopnia jest zoraz mniejszy. Ciśnienie końcowe w poszczególnych stopnich dobiera się tak, aby zużycie energii było najmniejsze. MOC sprężarek tłokowych moc teoretyczna Nt=LtQρ, Lt praca techniczna sprężania 1kg gazu, q wydajność m3/s, ρ -gestość kg/m3 Moc rzeczywista Nrz=Nt/ηm , ηm sprawność mechaniczna. Działanie spr tłokowej jest prawie identyczne jak pompy tłokowej. Budowa: żebrowane cylindry z tłokami środku, napędzający silnik elekt, zbiornik na spr powietrze. Spr z wirującymi tłokami – pompa Rootsa to objętościowa pompa rotacyjna, dwa obracające się tłoki tworzą przestrzenie, powodując zasysanie i sprężanie gazu, spręż <2, przetłaczanie dużej ilości gazu przy stosunkowo niewysokim ciśnieniu, może pracować jako pompa próżniowa przy niskiej próżni lub jako pompa wstępna przy układach wysokoprężnych. Spr śrubowa – maszyna typu wyporowego, komora sprężania jest przestrzenią utworzoną pomiędzy dwoma zazębiającymi się wirnikami w kształcie śruby i wewnętr5zną ścianą korpusu, objętość spr powietrza jest ściśle powiązana z wymiarami śrub, spręż zależy od długości wirników. Spr wirowa – rodzaj sprężarki przepływowej, w której szybko obracający się wirnik wywołuje określony wzrost ciśnienia oraz prędkości gazu, który to gaz przepływa w kierunku promieniowym lub osiowym (podobnie jak w pompach wirowych),każdemu wirnikowi odpowiada jeden stopień sprężania. Ze względu na kształt wirnika i kierunek przepływu gazu dzielą się na: sprężarki osiowe, osiowo-promieniowe, promieniowe. Wentylator promieniowy – przepływ gazu przez wirnik promieniowy, działa podobnie jak pompa odśrodkowa, wytw. różnica ciśnień 0,1-10kPa, do przetłaczania gazu o małym sprężeniu(urządzenia klimatyzacyjne, suszarnie). Ze względu na budowę: normalne, bębnowe, poprzeczne.
Do tłoczenia lub wyciągania powietrza w procesach produkcyjnych, systemach wentylacji, uk transportu pneumatycznego, suszarniach, modułów elektrycznych, elemantów maszyn. Wentylator osiowy – klimatyzacja, suszarnie, chłodnictwo, wentylacja, rolnictwo. W diagonalny – dosieci kanałów, wentylacja obiektów mieszkalnych, biurowych, przemysłowych. Pompa próżniowa – stosowana w technice do usuwania gazów w zamkniętej przestrzeni, zasysa gaz pod ciśnieniem poniżej 0,1 MPa, po sprężeniu do ciśnienia nieco większego od atmosf wytłacza go na zewnątrz. Najważniejszy parametr: najmniejsze ciśnienie jakie można uzyskać pompą – próżnia techniczna 100-2 kPa, pośrednia 2- 0,6 kPa, niska 600 – 1 Pa, wysoka <1Pa.
Próżnia techniczna: odparowanie, suszenie, destylacja, odgazowanie cieczy, filtracja. Wyróżnika max ciśnienie na wylocie pompy. Ze względu na sposób działania dzielimy na: wirowe (turbosprężarki), wyporowe (tłokowe, membranowe, z wirującymi tłokami), strumieniowe, jonowo-sorpcyjne, jonowo magnetyczne, molekularne, kondensacyjne. Magazynowanie gazów – zbiorniki niskociśnieniowe o zmiennej objętości: mokre i suche. Zbiorniki średnio i wysokociśnieniowe o stałej objętości: stałe (duże objętości gazu), pr4zenośne tzw butle gazowe (niewielkie pojemności). Niskociśnieniowe mokre: wielkość nadciśnienia 4-8 kPa, pojemność 1 do 200000 m3, średnica basenów 12-50 m, wysokość do 40m, do 20000m3 w budynkach, reszta na zewnątrz, zast ograniczone dla gazów nierozpuszczalnych w wodzie, tańsze w eksploatacji od zb suchych, konieczność ogrzewania zimą, ciężka konstrukcja. Wysokociśnieniowe suche: stała objętość, cylindryczne, kuliste, pojemność do 30000m3, ciśnienie do 30 bar, wieksze ciśnienie i pojemność zbiornika tym większa objętość magazynowania gazu, podlegają nadzorowi UDT, duże ilość gazów sprężonych – zb kuliste osadzone w betonie lub pływające w basenie wodnym śr do 50m, pojemnośc do 550000m3, ciśnienie do 0,43 MPa. Wysokociśnieniowe – butle gazowe: stalowe, ciągnione bez szwu, do 50dm3, ciśnienie do 15 MPa, gazy w stanie sprężonym: powietrze, tlen, azot, wodór, gazy szlachetne, gazy w stanie skroplonym: amoniak, CO2, chlor, gazy rozp w rozpuczalnikach np. amoniak w wodzie, CO2 w wodzie. Gazy technologiczne stosowane w przemyśle spożywczym – najczęściej azot i CO2 – w postaci ciekłej (do mrożenie, schładzania), lub gazowej (do pakowania w atmosferze ochronnej). Tlen do natleniania hodowli ryb, pakowanie w atmosferze ochronnej produktów mięsnych, wodór do utwardzania olejów, produkcja skrobi, argon do pakowania w atm ochronnej, etylen do dojrzewania owoców. Podstawowe zastosowanie gazów w przemyśle spożywczym – schładzanie, mrożenie, zamrażanie powierzchniowe w tunelach, szafach kriogenicznych, mrożenie IQF, pokrywanie sosami, schładzanie mikserów, kutrów, młynków oraz kontrola temp, pakowanie w atm ochronnej MAP, usuwanie tlenu z cieczy, produkcja napojów gazowanych, utwardzanie olejów. CO2 – temp wrzenia -78,5C,dostawa w butlach, z zb na ciekły gaz lub lub w fazie stałej (tzw suchy lód), stosowany w : karbonizacja napojów, mrożenie i chłodzenie żywności, regulacja temp podczas transportu. Azot – temp topnienia -195,9C, dostawa w butlach, w zb na ciekły gaz, rurociągami lub produkowany na miejscu (on site). Stosowany: szybkie mrożenie, schładzanie, konserwacja i ochrona art. Spożywczych. wodór – temp wrzenia – 252,8C dostawa w butlach, rurowozami, rurociągami lub produkowany na miejscu, stosowany: utwardzanie olejów spożywczych. pakowanie w atm ochronnej gazu- z gazów będących naturalnymi skł powietrza, bezwonnych i neutralnym smaku, odp skład mieszaniny gazów gwarantuje trwałości produktów nie powodując zmien fizyko-chemicznych produktu. Azot spełnia funkcje obojętnego wypełnienia oraz zabezpieczenia przed zapadaniem się opakowań. CO2 hamuje rozwój bakterii i grzybów(pleśni)i bakterii tlenowych. Tlen do zachowania trwałości barwy w przypadku wyrobów z surowego mięsa, do pakowania białych ryb oraz produktów oddychających – owoców i warzyw. Ciekły azot – technologia firmy Air Liquide – Crust Flow P poliestrowa taśma nasączona ciekłym azotem zmieniająca się w gąbkę. W zetknięciu z taśma produktu zostaje natychmiast zamrożony bez zmiany kształtu i tekstury. Doskonałe mrożenie powierzchniowe delikatnych, lepkich produktów. Crust Flow Vmrożenie i zamrażanie powierzchniowe małych i drobnych produktów. Produkt szybko mrożony w wibrującej wannie izolowanej próżniowo. Wibracje chronia produkt przed sklejeniem z innymi produktami i zapewniają transport produktu. Ciecze – sposób magazynowania zależy od objętości cieczy, właściwości cieczy (prężnośc par, korozyjność, palność, wybuchowość).zbiorniki otwarte i zamnknięte o pojemności od kilku do kilkudziesięciu tys dm3. ogólne wymagania wynikające z konstrukcji i zastosowania zbiornika na ciecze. Wytrzymałość konstrukcji zbiornika, odporność korozyjna, szczelność, wyposażone w odpowiednia armaturę umożliwiającą ich racjonalną eksploatację, rodzaj i typ uzależniony od zadań jakie mają spełniać. Wyposażenie zbiornika: właz dolny i górny, króciec spustowy i zasilający, króciec czujnika poziomu i temperatury, kurek poboru próbek – aseptyczny zawór, mieszadło boczne, pionowe, odpowietrznik, system CIP, przyrządy pomiarowo – kontrolne, króćce do napełniania i opróżniania, zb izotermiczne wyposażone dodatkowo w płaszcz izolujący. Temperatura ustala stan skupienia magazynowanej substancji i może wpływać na szereg zjawisk. Spadek temp poniżej temp zamarzania – zbiornik może pęknąć, przeciwdziałanie – ogrzewanie, mieszanie, przepompowywanie. Wzrost temp – odparowanie lotnych składników – straty materiałowe albo wzrost ciśnienia ponad dozwolone granice, przeciwdziałanie – izolacja zewnętrzna, konieczność dodatkowego chłodzenia.
Subst wchodzące w reakcje z powietrzem przechowuje się w atm gazu obojętnego (nadciśnienie gazu, ciągły dopływ niedużego strumienia tego gazu). Zjawisko rozwarstwienia cieczy na fazy – mieszanie albo dodatek stabilizatorów. Warstwa szlamu na dnie zbiornika – zawory spustowe do szlamu. Naładowanie się elektryczne zb podczas napełniania materiałami nieprzewodzącymi prądu elektrycznego – uziemienie zb. Ciecze zbiorniki podział – otwarte i zamknięte. Usytuowanie: podziemne, półpodziemne, naziemne. Kształt: cylindryczne, stożkowe, prostopadłościenne, kuliste, kroplokształtne. Tworzywo: metalowe, z tworzyw sztucznych, betonowe, drewniane nie izolowane, izolowane, izolowane z płaszczem grzejnym lub chłodzącym. Najczęściej stalowe pionowe lub poziome o kształcie cylindrycznym, najkorzystniejsze ze względów wytrzymałościowych, konstrukcyjnych i ekonom. Pojemność od 10 do 50 tys litrów, często kilka połączonych systemem rurociągów. Prostopadłościenne zajmują najmniej miejsca, najmniej ekonomiczne pod względem zużycia materiałów, najmniej wytrzymałe. Zbiorniki metalowe – SA wykorzystywane do różnych operacji technologicznych. Zalety: łatwe utrzymanie higieny, możliwośc przechowywania pod znacznym ciśnieniem, możliwość regulacji temperatury.wady: duża przewodniośc cieplna metalu utrudniająca utrzymanie stabilnej temp, koniecznośc izolacji. Ze stali zwykłej wymagaja pokrywania powłokami antykorozyjnymi, drogie w wykonaniu ze stali kwasoodpornej ale ekonomiczna eksploatacja: bez kosztu drogich wykładzin, odpadaja remonty, trwałość stali kwasoodpornej. Zbiorniki z tw sztucznych – do transportu i przechowywania np. win, przydatne do transportu ze względu na małą masę, pojemność do 30tys litrów, rózne kształty, lekkie, odporne na niskie i wysokie temperatury, nietoksyczne, odporne na środki chemiczne, gładkie- nie wymagaja specjalnych zabiegów pielęgnacyjnych, wykonane z żywic poliestrowych i impregnowanego włókna szklanego nadaja odpowiedni kształt i wytrzymałość zbiornikowi. Zbiorniki betonowe –w winiarstwie, przemysle owocowo warzywnym do trans i przechowywania dzięki powłokom ochronnym na bazie tworzyw sztucznych, prostopadłościany lub cylindryczne, kształt i wielkość zależy od pomieszczeń, profilu i zdolność produkcyjnych. Powinny Stanowic monolit, bez pęknięć i rys. powierzchnia dna powinna mieć niewielki spadek ok. 1% w kierunku spustu. Zalety: możliwość wykorzystania optymalnej kubatury pomieszczeń, najniższy koszt wykonania, długi okres użytkowania, niewielki zaniki płynu, łatwośc czyszczenia i mycia. Zbiorniki drewniane – wychodza z użycia, wady: ograniczone wykorzystanie pomieszczeń składowych, utrudnione utrzymanie higieny, wysoki koszt instalowania, utrudnienie wprowadzenia mechanizacji i automatyzacji, trudność przeprowadzenia zabiegów technologicznych. Zalety: neutralność w stosunku do składników płynu, niewielkie koszty konserwacji.zbiorniki do cieczy niebezpiecznych – do cieczy toksycznych, niebezpiecznych, żrących, trujących, ciekłych zapalnych. Zgodne z rozporządzeniem w sprawie warunków technicznych dozoru technicznego. Zbiorniki ciśnieniowe aseptyczne – do mag cieczy spożywczych w warunkach aseptycznych uzyskanych przez prowadzony proces mycia i sterylizacji zbiornika i utrzymywanie nadciśnienie do momentu napełnienia zbiornika i po napełnieniu zbiornika. Armatura aseptyczna: rura poprowadzona wzdłuż zbiornika, wspawana z jednej strony do dennicy górnej i sprowadzona do poziomu 1800 mm, na końcu rurociągu zawór sterylny, złącza aseptyczne. Króciec probierczy aseptyczny do mycia i sterylizacji bez demontażu. Np. magazynowanie soków i koncentratów owocowych. Zbiorniki do miazgi – owocowej i warzywnej, najważniejsze odpowiednie ukształtowanie dennic, tak aby miazga mogła zsuwać się bez zakłóceń, w środku mieszadła o dużej mocy i właściwym kształcie łopat. Zbiorniki procesowe z systemami podgrzewania i chłodzenia: jednopłaszczowe, dwupłaszczowe, z płaszczami wodnymi, z wężownicami, zbiorniki CIP. Zbiorniki winiarskie do leżakowania wina, izolowane do stabilizacji, fermentacyjne z systemami podgrzewania i chłodzenia. Orurowanie i systemy rurociągów instalacji zbiorników – w systemie panelowym, w którym przyłączanie rurociągów odbywa się przez zmianę połączeń na specjalnej tablicy, orurowanie z wykorzystaniem złączy elastycznych, systemy orurowania stałego , z możliwością wizualizacji poziomu medium w poszczególnych zbiornikach. Ciała stałe magazynowanie – sposób magazynowanie zależy od charakterystyki ciała sypkiego: rodzaj i skład chemiczny substancji, rozmiar i kształt ziarna, gęstość nasypowa i porowatośc złoża, właściwości chemiczne, zdolność przejścia w stan zawieszenia i transportu pneumatycznego, zawartośc wilgoci, zawartośc substancji lotnych. Ciała stale elementy mechaniki ciał sypkich – rodzaje zsypu: rdzeniowy – część materiału w ruchu część w spoczynku, duże tarcie ściana-materiał, „pierwszy wszedł, ostatni wyszedł”(segregacja), materiały łatwopłynące, gruboziarniste, dla których segregacja nie ma znaczenia, nie podatne na zbrylanie. Magazynowanie ciał stałych problemy w obrocie na skutek zaburzeń przepływu, skutki: zmniejszenie pojemności użytkowej zbiornika (przepływ rdzeniowy), zbrylenie materiału sypkiego, wibracje i osłabienie wytrzymałości zbiornik na skutek zawalenia się nawisów, uszkodzenie zbiornika .
Magazynowanie ciał stałych problemy z wysypem – środki zapobiegawcze. Odpowiedni zaprojektowany zbiornik dla danego materiału (kształt, pojemność, gładkość, nachylenie ścian, średnica otworu wysypowego, wytrzymałość), charakterystyka materiału w symulowanych warunkach magazynowania – właściwośc płynięcia (kąt tarcia wewnętrznego, kohezja, kąt tarcia o ściany)gęstość nasypowa, ściśliwość. Warunki magazynowania – temp , wilgotność, okres składowania. Czynniki wymuszające: stosowanie wibratorów lub wytrząsaczy, wprowadzenie strugi powietrza, by oderwać materiał od ściany, załamać sklepienie, spulchnić złoże. Połączenie zasobnika z odpowiednim przenośnikami rozładowującym, dodatek substancji zmniejszających tarcie wewnętrzne.
...