Twoim problemem jest to, że powszechną NICOŚĆ mylisz z osobistą PUSTKĄ
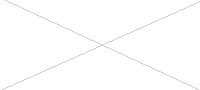
1. METODY WYKONYWANIA OTW. Metody wiertnicze dzielimy na klasyczne i na metody niekonwencjonalne, mające mniejsze zastosowanie i będące w stadium prób.
Metody klasyczne dzielimy w zależności od:
– sposobu zwiercania skały na dnie otworu
– rodzaju przewodu wiertniczego
– wielkości średnicy otworu
– sposobu usuwania zwiercin z dna otworu
– siły napędowej używanej do wiercenia i umieszczenia silnika
– kierunku wykonywania otworów
W zależności od sposobu zwiercania skały na dnie otworu wiertniczego wiercenia można podzielić na udarowe, obrotowe i udarowo-obrotowe lub obrotowo-udarowe. Metody wierceń udarowych można podzielić w zależności od rodzaju przewodu na wiercenia z przewodem linowym i wiercenia z przewodem żerdziowym. Wiercenia udarowe na przewodzie żerdziowym, w zależności od liczby udarów świdra o skałę, można podzielić na wolno- i szybkoudarowe.
W zależności od sposobu usuwania zwiercin z dna i spodu otworu wiercenia udarowe dzielą się na suche lub płuczkowe. W czasie wiercenia suchego zwierciny z dna otworu wiertniczego wydobywa się zawieszoną na linie łyżką, a przy wierceniu płuczkowym zwierciny są usuwane i wynoszone na powierzchnię przez wtłaczaną do otworu płuczkę wiertniczą.
Wiercenia udarowe mogą być ręczne lub mechaniczne, można je podzielić na wiercenia udarowe zwykłe z silnikiem na powierzchni ziemi oraz wiercenia z silnikiem na spodzie, w otworze ponad świdrem. W zależności od częstotliwości udarów świdra o skałę w metodzie udarowej można wyróżnić wiercenia wolnoudarowe lub szybkoudarowe.
Metody wierceń udarowych mogą służyć do wykonywania otworów normalnych o średnicy do 500 mm lub otworów wielkośrednicowych, np. szybów wiertniczych, o średnicy powyżej 500 mm.
Metody wiercenia obrotowego, ze względu na siłę napędową potrzebną do obracania świdra przy wierceniu, dzielą się na wiercenia ręczne obrotowe – okrętne albo wiercenia mechaniczne obrotowe – maszynowe. W metodzie okrętnej przewodem są żerdzie, a w metodach mechanicznych rury płuczkowe.
Przy metodach obrotowych mechanicznych zwierciny usuwane są z dna otworu przez tłoczoną z powierzchni płuczkę wiertniczą, przy metodach udarowych zaś specjalnym przyrządem w kształcie rury zwanym łyżką, która ma umieszczony u dołu zawór. Stąd też wiercenie z płuczką nazywa się mokrym, a bez płuczki — suchym.
W zależności od wielkości średnic wykonywanych otworów wiercenia mechaniczne obrotowe można podzielić na:
— normalnośrednicowe — Rotary — o początkowej średnicy ≤ 500 mm,
— małośrednicowe, zwane czasem małodymensyjnymi, zwykle o początkowej średnicy otworu wynoszącej ≤ 200 mm,
— wielkośrednicowe, zwane wielkodymensyjnymi, przy wykonywaniu otworów (szybów wiertniczych, tuneli) o najmniejszej początkowej średnicy ≤ 500 mm.
W zależności od sposobu otrzymywania próbek z wierceń metody wiertnicze można podzielić na: — wiercenia rdzeniowe i wiercenia pełne, zwane też pełnootworowymi — bezrdzeniowe. Rdzenie można też otrzymywać przy wierceniach w postaci „kawałków" przy odwrotnym krążeniu płuczki (metoda Con-Cor).
Biorąc pod uwagę sposób wprowadzania w ruch obrotowy przewodu wiertniczego (rur płuczkowych), wiercenia mechaniczne można podzielić na: — wiercenia stołowe (Rotary), — wiercenia wrzecionowe.
W zależności od sposobu usuwania próbek skalnych spod świdra przez płuczkę. wiercenia obrotowe można podzielić na: — płuczkowe z prawym krążeniem płuczki wiertniczej, — płuczkowe z odwrotnym krążeniem płuczki wiertniczej.
Jednocześnie płuczkę wiertniczą można stosować w postaci lotnej (powietrze), w postaci płynnej (iłowa, olejowa, wapienna, wodna, skrobiowa itd.) lub w postaci „kombinowanej".
W zależności od miejsca umieszczenia silnika napędowego wiercenia obrotowe mechaniczne można podzielić na: — wiercenia z silnikiem na powierzchni, wiercenia z silnikiem na spodzie otworu wiertniczego, bezpośrednio nad świdrem. Do metod z silnikiem na spodzie otworu wiertniczego można zaliczyć: — wiercenia elektrowiertem, — wiercenia turbowiertem.
W zależności od rodzaju przewodu, na którym zapuszcza się elektrowiert do otworu, można podzielić te wiercenia na:
— wiercenia elektrowiertem rurowym zapuszczanym na rurach płuczkowych, — wiercenia elektrowiertem bezrurowym zapuszczanym na linie. Przy wierceniach turbowiertem, zwanych inaczej wierceniami turbinowymi, zamiast silnika elektrycznego stosuje się turbinę napędzaną płynną płuczką wiertniczą. Wierceniami, w których przewodem wiertniczym są rury płuczkowe, można wykonywać otwory: — normalne — pionowe w dół, kierunkowe — celowo odchylone od pionu pod określonym kątem.
Wiercenia udarowo-obrotowe w zależności od przewagi udarów czy też obrotów przy wierceniu dzielą się na: — udarowo-obrotowe, — obrotowo-udarowe.
Metody niekonwencjonalne dzielą się na: wybuchowe, termiczne, hydrauliczne i elektrofizyczne.
2. SYSTEMY OBIEGU PŁUCZKI.
– normalne krążenie płuczki
– odwrotne krążenie płuczki
– specjalne systemy krążenia płuczki
Wynoszenie zwiercin ze spodu otworu odbywa się przy wierceniach obrotowych wskutek krążenia płuczki wiertniczej. Krążenie płuczki wiertniczej może być normalne czyli prawe lub odwrotne. Najczęściej jest stosowane prawe krążenie płuczki. Odmianą prawego krążenia płuczki Jest odwrotne krążenie. W tym przypadku płuczka wiertnicza jest tłoczona z powierzchni ziemi pompą płuczkową na spód otworu, przestrzenią między ścianą otworu a przewodem wiertniczym. Z dna otworu wiertniczego wynosi kawałki rdzeni odwiercone przez koronkę i rurami płuczkowymi wypływa do koryta na powierzchnię ziemi. Przy odwrotnym krążeniu płuczki mogą być wynoszone większe okruchy skalne, a nawet kawałki rdzenia. Jest to możliwe dzięki większej prędkości strumienia wypływającej płuczki wiertniczej w rurach płuczkowych.
Przy wierceniach otworów wielkośrednicowych bezrdzeniowych można po kolei stosować wszystkie trzy systemy krążenia, przy czym mogą się one zmieniać w poszczególnych etapach wiercenia takiego otworu.
Przy wierceniach rdzeniowych oraz turbinowych stosowane jest zazwyczaj normalne krążenie płuczki lub obiegi specjalne, jakkolwiek mogą wystąpić wówczas trudności w stosowaniu pomp płuczkowych o wymaganych wydajnościach.
Przy wierceniach wielkośrednicowych bezrdzeniowych powinno się stosować odwrotne krążenie płuczki, które w porównaniu z normalnym zapewnia większą prędkość przepływu płuczki wynoszącej zwierciny, w związku z czym mogą być wynoszone większe cząstki zwiercin. W przypadku powiększenia prędkości przepływu płuczki dla uzyskania lepszego oczyszczania dna otworu, wymywanie ściany otworu wiertniczego nie stwarza zbyt dużego niebezpieczeństwa. Do wad tego systemu krążenia należy zaliczyć jednak zbyt słabe oczyszczanie dna otworu oraz ostrzy świdra przez płuczkę na skutek małej prędkości jej przepływu na dnie otworu. Poza tym przy odwrotnym systemie krążenia płuczka porywa zwierciny spod świdra, doprowadzając je do środka otworu. Przeciwstawiają się temu siły odśrodkowe powstałe przy obracaniu się przewodu ze świdrem. W wyniku tego zwierciny skalne przemieszczają się do środka otworu po dłuższej drodze, co powoduje większe zanieczyszczenie dna otworu zwiercinami oraz powtórne ich urabianie (dodatkowa praca). Przy tym obiegu do wynoszenia płuczki ze zwiercinami wykorzystywana jest energia sprężonego powietrza, którego cząsteczki wtłoczone w płuczkę ciekłą posiadają siłę unoszenia równą ciężarowi wypartej płuczki (przy pominięciu ciężaru powietrza). Poza tym przy odwrotnym systemie płukania otworu płuczka znajduje się w ruchu wraz z przewodem wiertniczym poniżej poziomu zanurzenia rur powietrznych. W związku z tym powstają dodatkowe opory hydrauliczne przepływu, na pokonanie których zużywane jest dodatkowe ciśnienie.
Odwrotny system krążenia płuczki może być zrealizowany przez zastosowanie sprężonego powietrza (air-liftu) do wynoszenia płuczki ciekłej ze zwiercinami na powierzchnię przy użyciu agregatu pompowego ssącego.
Prawe i lewe krążenie płuczki wiertniczej
Wiercenia mogą być wykonywane przy prawym i lewym (odwrotnym) krążeniu płuczki w otworze wiertniczym. Przy prawym krążeniu płuczki pompy płuczkowe zasysają płuczkę wiertniczą ze zbiornika ssawnego i przetłaczają ją za pośrednictwem przewodów napowierzchniowych do kolumny rur płuczkowych i do świdra, skąd po wypływie z kanałów świdra płuczka oczyszcza dno otworu wiertniczego ze zwiercin i wypływa przestrzenią pierścieniową poza kolumną rur płuczkowych na powierzchnię, gdzie oczyszcza się w korytach płuczkowych i następnie wpływa do zbiornika stawnego płuczki.
Przy lewym krążeniu płuczki wiertniczej przepływ płuczki odbywa się w odwrotnym kierunku. Płuczka wiertnicza wtłaczana jest do przestrzeni pierścieniowej poza kolumną rur płuczkowych i po oczyszczeniu dna otworu ze zwiercin wpływa otworami do wnętrza świdra, a stąd do kolumny rur płuczkowych, którymi wypływa na powierzchnię, wynosząc zwierciny skalne w postaci małych rdzeni.
Lewe krążenie zaleca się przy przewierceniu pokładów o wysokim ciśnieniu złożowym. W tych przypadkach płuczka o wyższym ciężarze właściwym, płynąc w dół w przestrzeni pierścieniowej, będzie zabierać z sobą bańki gazu razem ze zwiercinami i wynosić je na powierzchnię poprzez kolumnę rur płuczkowych.
Krążenie lewe można także z korzyścią zastosować przy wierceniach węglowych, gdzie uzyskanie rdzeni z pokładów węglowych ma podstawowe znaczenie. Wszystkie urządzenia do wiercenia z krążeniem lewym przystosowane są również do wiercenia z krążeniem prawym.
Przy wierceniu z krążeniem lewym wylot otworu wiertniczego musi być uszczelniony za pomocą odpowiedniego dławika, poza tym świdry muszą mieć kanały przelotowe o większej średnicy dla przejścia rdzenia. Stosowanie krążenia lewego ma następujące zalety: — zmniejszanie się zaiłowania przewiercanych pokładów, — wysoka prędkość wynoszenia okruchów skalnych (rdzeni), — wynoszenie większych okruchów skalnych, które dają możność szybszego rozpoznania geologicznego przewierconych warstw, — łatwiejsze wykonywanie niektórych robót ratunkowych. Do wad krążenia lewego należą:
— niemożność jego stosowania w przypadku zaniku płuczki w otworze wiertniczym w warstwach spękanych, szczelinowatych i silnie porowatych,
— trudności z utrzymaniem szczelności dławika u wylotu otworu wiertniczego,
— możliwość zatykania okruchami skalnymi kanałów przelotowych w świdrze i w rurach płuczkowych,
— konieczność w wielu przypadkach orurowania ścian otworu wiertniczego.
3. RODZAJE PŁUCZEK WIERTNI-CZYCH I ICH PARAMETRY TECHNO-LOGICZNE ORAZ REOLOGICZNE.
Przy wierceniach stosowane są dwa rodzaje płuczek: gazowa (powietrze) i ciekła (albo równocześnie oba rodzaje). Jako płuczkę ciekłą najczęściej stosuje się wodę, zwykle z różnymi datkami (syntetyczne mydła, oleje itd.). Można też sporządzać płuczkę z wody, iłu oraz różnych dodatków, czyli odczynników. Płuczki ciekłe można zaliczyć częściowo do zawiesin, częściowo do roztworów koloidalnych.
Różnice zachodzące między roztworami zależą od składu chemicznego, rodzaju i wymiarów oraz kształtu cząstki ciała stałego znajdującego się w wodzie. W wiertnictwie stosuje się rozmaite płuczki wiertnicze, różniące się od siebie własnościami chemicznymi i fizycznymi. Płuczki ciekłe można zaliczyć do następujących płynów: plastyczno - lepkie (binghamowskie), niekiedy jako płyny pseudoplastyczne lub plastyczno-tiksotropowe, a nawet jako płyny lepko-sprężyste.
1) Płuczkę wapniową można zaliczyć do płuczek inhibitowanych. Jej zalety to niska lepkość i odporność na rozpuszczanie iłów oraz odporność na zbyt duże skażenia elektrolitami. Wadą tej płuczki jest jej nieodporność na wysoką temperaturę. Głównym składnikiem jest tu bentonit – ok. 8%
2) Płuczki chlorkowo-wapniowe różnią się od płuczek wapniowych tym, że oprócz słabo rozpuszczalnego wapna stosuje się dodatki chlorku wapnia o dużej rozpuszczalności.
3) Płuczka gipsowa jest odporna na temperatury do 200°C i ma oprócz bentonitu w ilościach 7% również gips w ilości 1–2%
4) Płuczki potasowe są przystosowane do wiercenia w skałach ilastych. Obok bentonitu zawierają one wodorotlenek potasu, lignit potasowy i potasowy preparat skrobiowy.
5) Płuczka chlorkowo-potasowa ulega gęstnieniu w temperaturze około 200°C i jest odporna na skażenia chlorkiem sodu (do 5%). Jest mało odporna na gips, anhydryt i chlorek magnezu.
6) Płuczki zaso1one stosuje się do przewiercania warstw soli lub pokładów zasolonych. W zależności od ich składu, płuczki te dzielą się na: solankowe, wielosolne, glikocelowo- solne. Płuczki te działają korozyjnie na przewód wiertniczy. Ograniczanie korozyjnej działalności tej płuczki jest możliwe poprzez podniesienie wartości pH do około 10.
7) Płuczka so1no–skrobiowa- jest sporządzona na bazie płuczki iłowej lub bentonitowej, do której dodaje się takich soli, jak NaCI, KCl lub MgCl2, a następnie obniża się filtrację dodatkiem skrobi. Ma bardzo niską wytrzymałość strukturalną.
8) Płuczki emu1syjne otrzymuje się na bazie każdej płuczki sporządzonej na bazie wodnej przez dodanie 5-20% oleju napędowego lub ropy naftowej. Odmianą tych płuczek mogą być płuczki wiertnicze inwersyjne. Do płuczek wiertniczych inwersyjnych dodaje się stabilizatory emulsji.
9) Płuczka powietrzna ma zastosowanie tam, gdzie są trudności w zaopatrzeniu w wodę. Nadaje się do wiercenia w warstwach suchych i w przypadku zaniku krążenia płuczki ciekłej w skałach porowatych.
4. NAPOWIERZCHNIOWE UKŁADY URZĄDZEŃ DO SPORZĄDZANIA, REGULACJI PARAMETRÓW ORAZ OCZYSZCZANIA PŁUCZKI.
Na osiągnięcie celu wiercenia wpływa jakość zastosowanej płuczki wiertniczej. Materiałem wyjściowym do sporządzania płuczek jest ił. Najlepszym z materiałów ilastych do sporządzenia płuczek jest grupa montmorillonitu, iły pochodzące od tej grupy mają zdolność dużego rozproszenia cząstek w wodzie. Iłem tego typu jest bentonit, który w stanie suchym jest zbity i zwarty, natomiast po zmieszaniu z wodą wchłania ją na swojej powierzchni. Materiał ilasty nie zawsze jest głównym składnikiem płuczki wiertniczej, ale może być użyta jako część składowa. Jakość płuczki jest tym wyższa im więcej jest w niej cząstek koloidalnych. Wielkością charakteryzującą przydatność danego iłu do sporządzania płuczki wiertniczej jest jego wydajność (tzn. ile otrzymamy płuczki w m3 z jednej tony suchego iłu).
Płuczkę sporządza się w dwojaki sposób:
1) mat. do sporządzania pł. Przygotowuje się w wytwórni w postaci proszku, (ił jest suszony, drobno mielony, przesiany przez sita, następnie mieszany wraz dodatkami i workowany).
2)drugi sposób polega na mieszaniu surowego iłu z wodą w specjalnych mieszalnikach bezpośrednio przy otworze lub w wytwórni pł.
Mieszania pł. dokonuje się w specjalnych mieszalnikach, do których zaliczyć należy :
- mieszalniki jednowałowe poziome lub dla uzyskania lepszej wydajności dwuwałowe poziome stosowane do mieszania iłów surowych (w skład mieszalnika wchodzi: kadłub w którym znajduje się wał (wały) z łopatkami służącymi do mieszania iłu z cieczą zarobową)
- mieszalniki lejowe do wykonywania pł. z suchego iłu, (zbudowany jest on z leja pod którym jest komora próżniowa wraz z dyszą przez którą doprowadza się wodę).
- mieszalniki składające się z kilku pionowych mieszadeł (na zbiorniku płuczki zamocowane są mieszadła, w tymże zbiorniku znajduje się komora gdzie można mieszać sproszkowany ił z dodatkami ulepszającymi).
Wzory na obl. masy iłu i wody potrzebnej do sporządzenia 1 m3 płuczki o określonej gęstości:
mi – masa iłu suchego
mw – masa wody
(indeksy oznaczają:
p – płuczki, w – wody,
i – iłu).
Oczyszczanie płuczek wiertniczych
Do oczyszczania wypływającej płuczki z otworu ze zwierconych i wynoszonych zwiercin służą specjalne urządzenia umieszczone przy otworze wiertniczym.
Oczyszczenie płuczki wiertniczej ze zwiercin można przeprowadzić hydraulicznie, mechanicznie i chemicznie. Oczyszczanie hydrauliczne odbywa się w takich urządzeniach jak zbiorniki i koryta płuczkowe, oczyszczanie mechaniczne zaś na sitach wibracyjnych, sitach transporterach, w separatorach i hydrocyklonach.
Osadzanie się zwiercin w czasie przepływu płuczki przez koryta i zbiorniki zależy głównie od prędkości jej przepływu przez koryta, od długości koryt oraz od typu zastosowanych przegród osadników lub zbiorników.
Do oczyszczania płuczki wiertniczej można stosować koryta składające się z dwóch koryt równoległych, połączonych ze sobą co parę metrów. Płuczkę można skierować jednym lub obydwoma równoległymi korytami. Przegrody o wysokości 12-30 cm dzielą koryta na sekcje.
Zwierciny z płuczki mogą się również osadzać w osadnikach, które wbudowane są poziomo w korytach płuczkowych.
Do właściwego oczyszczania płuczki ze zwiercin służą urządzenia mechaniczne i hydrauliczne. Jednym z takich urządzeń jest sito wibracyjne. Na sicie pozostają zwierciny, które stopniowo zsuwają się po pochyłej powierzchni siatki do dołu zwiercinowego, płuczka zaś, wstępnie oczyszczona, przepływa do koryt. Sito może być pojedyncze lub podwójne. Sito podwójne ma dwie sekcje, a jego wydajność jest dwukrotnie większa niż wydajność sita pojedynczego.
Oprócz sita wibracyjnego ma także zastosowanie sito obrotowe (separatory).
Innym urządzeniem jest wirówka, która służy do oczyszczania płuczek wiertniczych, zwłaszcza do rozdzielania ciekłych zawiesin lub emulsji zawierających składniki o róźnej gęstości. Podczas pracy tego urządzenia powstaje siła odśrodkowa, wskutek czego większe i cięższe cząstki odrzucane są na ścianę zewnętrznego cylindrycznego stożka. Tylko mniejsze cząstki przenoszone są do wnętrza wirnika razem z oczyszczoną cieczą, większe zaś wypływają na zewnątrz.
Do oczyszczania płuczki wiertniczej zwłaszcza z piasku, oraz materiałów obciążających, stosuje się hydrocyklony. Oczyszczanie płuczki w hydrocyklonie odbywa się wskutek działania siły odśrodkowej wirującej strugi płuczki oddzielającej z niej zwierciny. W celu uzyskania większej wydajności kilka hydrocyklonów łączy się ze sobą równolegle.
Do oczyszczenia płuczki wiertniczej, w zależności od wymaganego stopnia jej oczyszczania, stosuje się urządzenia mechaniczne oczyszczające jedno- lub wielostopniowe. Dwustopniowy system oczyszczania stosowany jest do płuczek wiertniczych konwencjonalnych, o dużej zawartości zwiercin. W przypadku wiercenia z płuczką o małej zawartości fazy stałej można zastosować trójstopniowy system oczyszczania, z wykorzystaniem np. odmulaczy.
Odgazowanie płuczek wiertniczych z gazu ziemnego przedostającego się z przewierconego pokładu ma duże znaczenie dla regulowania parametrów płuczki. Urządzenia do oddzielania gazu z płuczki wiertniczej opierają się na zasadzie mieszania płuczki i rozprowadzania jej cienkimi warstwami, co ułatwia uwolnienie pęcherzyków gazu od cieczy. Drugi sposób to odgazowywanie próżniowe.
5. REGULOWANIE WŁASNOŚCI PŁUCZEK WIERTNICZYCH (GĘSTOŚĆ, LEPKOŚĆ, ZAWARTOŚĆ FAZY STAŁEJ, GRANICY PŁYNIĘCIA i WYTRZYMAŁOŚCI STRUKTURALNEJ, FILTRACJI I PH)
Płuczki powinny być przystosowane do warunków występujących w otworze. Uzyskuje się to przez dodanie do płuczki odczynników chemicznych odczynniki chemiczne można podzielić na trzy grupy:
1) Odczynniki stabilizatory (peptyza-tory)– środki powierzchniowo-aktywne
2) Odczynniki strukturotwórcze, przyczyniające się do tworzenia struktury w płuczce wiertniczej
3) Odczynniki · koagulatory– obojętne lub kwaśne sole lub kwasy,
LepkośćNajprostszą metodą obnażania lepkości płuczki jest rozrzedzenie jej wodą lub wodą z dodatkiem bentonitu. Wodę do płuczki dodaje się wówczas, jeśli lepkość wzrosła na skutek wzrostu koncentracji fazy ilastej
lepkość płuczki reguluje się najczęściej za po-mocą chemicznych środków rozrzedzających. Fosforany:
a. kwaśny pirofosforan sodu
b. heksametafosforan sodu
...