Twoim problemem jest to, że powszechną NICOŚĆ mylisz z osobistą PUSTKĄ
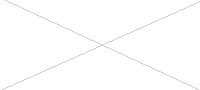
KOMPOZYTY (COMPOSITES) 2(2002)4
Marek Galanty
1
Akademia Górniczo-Hutnicza, Wydział Metali Nieżelaznych, al. Mickiewicza 30, 30-059 Kraków
WYCISKANIE NA ZIMNO METALICZNYCH MATERIAŁÓW POROWATYCH
Przedstawiono wybrane wyniki badań związane z wyciskaniem na zimno metalicznych materiałów porowatych na przykła-
dzie rozpylanego proszku aluminiowego RAL 1 dla wyraźnie zróżnicowanych frakcji ziarnowych 30, 110 i 450
μ
m. Wyko-
rzystano specjalnie przygotowany wsad wstępnie dwustronnie prasowany w szerokim zakresie ciśnień oraz proszek sypki
frakcji 450
μ
m. Wyciskanie prowadzono na prasie hydraulicznej 3MN o stabilizowanej prędkości ruchu stempla.
Badano wpływ ciśnienia prasowania na charakterystykę siłową procesu, a poprzez ustalenie poziomu siły oceniano wpływ zasto-
sowanego smaru, prędkości wyciskania, stopnia odkształcenia i kształtu matrycy. Określono zmiany gęstości wsadu
i wyrobu w zależności od parametrów procesu. Uzyskane wyniki pozwalają dokonać oceny możliwości wyciskania na zimno róż-
nymi metodami metalicznych materiałów porowatych i ustalić właściwy dobór warunków prowadzenia tego procesu.
COLD EXTRUSION OF POROUS METALLIC MATERIALS
The well known advantages of P/M technology focus our attention also on manufacturing long products of complicated
cross-section. The extrusion process is capable of producing such products, and additionally, due to the favourable state
of stress in the deformation zone, the high degree of material consolidation can be obtained. This influences in a positive way the
mechanical properties of the product. The two extrusion techniques are possible in practice. First one (Fig. 1a,b) is
similar to the conventional extrusion of solid feedstock; it consists in forward or backward extrusion of compacted samples. The
second case consists in extrusion of a loose powder (Fig. 1d) material poured directly into the extrusion container, in which the
opening (die) is covered with a metallic disk. The loose powder pressed by the punch undergo densification, next pushes out the
disk and flows out through the die in the form of a solid extrudate. The second technique can be performed only in a room tem-
perature without using of binders, that are usually added to the metal powder to enhance it densification. In this case the deci-
sive role play the adhesive forces between the powder particles. The attraction of this procedure is
shortened way from the powder to finished product, by eliminating compaction and sintering from the processing route.
The aim of this work was to perform the extensive experiments on the cold extrusion of compacts and loose metallic pow-
ders. Three selected fractions of technical purity (99.5 wt.%) atomised aluminium powder RAL1 of 0
÷
30, 110 and
450
μ
m were used to prepare compacts of different green density (Fig. 2) for cold extrusion (Figs 3-5). Additionally, the loose
fraction of 450
μ
m was used directly in the extrusion. The extrusion was performed on a 3MN capacity vertical hydraulic press.
The container of 35 mm in diameter was equipped with a dies having different opening diameter within the range
of 16÷9 mm. Before filing the container the die opening was covered with aluminium disks of various thickness. Due to this fact
the extrusion was initiated at different loads, so that, the powder in the container was consolidated prior to extrusion to differ-
ent density. At the stable state of the extrusion the process was interrupted and the rest of the feedstock was taken out of the
container. The rests were next submitted to hardness examination on their axial cross-section (Fig. 6) to determine
the mode of the material flow within the container. The density and hardness at different locations of the extruded rods were
also examined.
The extrusion load in dependence on the ram displacement was recorded during experiments (Figs 3, 7). The samples from
different locations of the extrudate were submitted to mechanical testing. The obtained results enabled to determine
the influence of the extrusion mode on the load required, on the material flow and on the distribution of mechanical pro-
perties along the extrudate length.
WSTĘP
Wykorzystywane w praktyce metaliczne materiały
porowate (MMP) są wykonywane głównie z proszków
metali na drodze prasowania wstępnego wypraski
o konkretnie wymaganym kształcie lub przez walcowa-
nie albo wyciskanie, umożliwiające uzyskanie wyrobu o
znacznej długości i stosunkowo małym przekroju po-
przecznym, np. druty, taśmy i kształtowniki. Obok uzy-
skania pożądanego kształtu finalnego ważnym zadaniem
jest również możliwie duże i jednorodne zagęszczenie
materiału, inaczej mówiąc, uzyskanie kontrolowanej
niskiej porowatości w całej masie wyrobu.
Podstawowym celem pracy jest doświadczalna wery-
fikacja możliwości wykorzystania wyciskania MMP na
zimno i przygotowanie założeń do opracowania takiej
technologii. W klasycznej technologii produkcji stosuje
się prasowanie proszku w zamkniętych matrycach lub
wyciskanie mieszaniny proszków na gorąco wraz z tzw.
środkami poślizgowymi. Środki te usuwane są z półwy-
robu w trakcie dalszej operacji spiekania
w podwyższonych temperaturach [1-3]. Zastosowanie
wyciskania MMP na zimno pozwoli uzyskać duże stop-
nie zagęszczenia (ok. 95% gęstości teoret.) wskutek
1
dr inż.
136
M. Galanty
działających sił adhezyjnych, a także wyeliminować
stosowanie środków poślizgowych i skrócić czas wyko-
nania wyrobu. Duże odkształcenie objętościowe zapew-
nia dobrą zagęszczalność i poprawia równomierność
własności wyrobu, a proces prowadzony na zimno za-
bezpiecza przed utlenianiem składniki wsadu.
Wyciskanie, jako proces technologiczny przeróbki
plastycznej, charakteryzuje się korzystnym stanem na-
prężenia, sprzyjającym formowaniu półwyrobów, szcze-
gólnie dla materiałów mało plastycznych i trudno od-
kształcalnych, do których zalicza się powszechnie
MMP. Próby wykorzystania tej techniki bazują głównie
na doświadczeniach z materiałami metalicznymi litymi i
przynoszą dobre efekty w przypadku materiałów kom-
pozytowych i proszkowych wyciskanych na gorąco.
Jednak obniżone własności wytrzymałościowe gorącego
wyrobu wychodzącego z matrycy często sprzyjają wy-
stępowaniu powierzchniowych pęknięć, wskutek działa-
jącego poza paskiem kalibrującym narzędzia naprężenia
rozciągającego. Temperatura jest też powodem koniecz-
ności stosowania operacji odgazowania wsadu i stoso-
wania ochronnych atmosfer redukujących, zabezpiecza-
jących wsad przed utlenieniem. Usunięcie tych proble-
mów technicznych wydaje się być możliwe w przypadku
technologii wykluczającej wpływ temperatury na etapie
formowania przy wyciskaniu
Sam proces wyciskania może być prowadzony na
trzy sposoby. Pierwszy polega na wyciskaniu wstępnie
sprasowanych na zimno wyprasek (rys. 1A, B) i nie
różni się technicznie od wyciskania litych metali.
W drugim sposobie stosuje się jako wsad tzw. „nabój”,
czyli sypki proszek zamknięty w metalowej osłonie (rys.
1C). Wreszcie można wyciskać sypki proszek zasypy-
wany bezpośrednio do recypienta (pojemnika) prasy,
zamykając otwór matrycy krążkiem metalu
(rys. 1D). Ostatni sposób, realizowany wyłącznie na
zimno, umożliwia też jednoczesne platerowanie wyrobu,
a poprzez zmianę grubości krążka - różne warunki wy-
ciskania i stąd różne własności wyrobu.
OPIS BADAŃ
W pracy pokazano wybrane wyniki badań wyciska-
nia metalicznych materiałów proszkowych na zimno na
przykładzie wsadu z rozpylanego proszku aluminiowe-
go RAL1 dla trzech wyraźnie zróżnicowanych frakcji
ziarnowych 30, 110 i 450 μm. Wykorzystano specjalnie
przygotowany wsad wstępnie dwustronnie prasowany w
szerokim zakresie ciśnień 25÷900 MPa oraz proszek
sypki frakcji 450 μm. W tym drugim przypadku stoso-
wano zamknięcie matrycy krążkami blachy aluminiowej
o grubości 0,5÷3,0 mm. Wyciskanie prowadzono z peł-
ną rejestracją parametrów procesu na prasie hydraulicz-
nej pionowej 3MN o stabilizowanej prędkości ruchu
stempla, używając stale recypienta ∅35 mm x 150 mm.
Zarówno wyroby, jak i częściowo wyciśnięty wsad pod-
dano ocenie gęstości średniej oraz rozkładu gęstości na
przekroju poprzecznym i wzdłużnym, w niektórych
przypadkach wykonano pomiary twardości, szacując
w ten sposób zmiany gęstości i własności wytrzymało-
ściowych.
A B
C
WYNIKI BADAŃ
Wyciskanie MMP ze wsadu wstępnie zagęszczonego
Wsad wstępnie zagęszczony przygotowany poprzez
prasowanie dwustronne charakteryzował się zróżnico-
waną porowatością, a przez to również różną gęstością
i twardością. Gęstość i twardość wyprasek rośnie ze
wzrostem ciśnienia prasowania. Krzywa zależności
twar- dości HB w funkcji ciśnienia prasowania ma prze-
bieg podobny do krzywej zagęszczalności proszków
(rys. 2).
Wyniki wpływu zagęszczenia wstępnego materiału
porowatego na proces wyciskania na zimno pokazano na
rysunkach 3-5. Krzywe zmiany siły w trakcie procesu są
typowe dla wyciskania na zimno, gdzie wskutek ruchu
stempla wraz z postępującym skróceniem wsadu zmniej-
szeniu ulegają siły tarcia (zmniejszenie powierzchni
styku z narzędziami), ale jednocześnie wzrastają wła-
D
Rys. 1. Ogólne schematy wyciskania metalicznych materiałów proszko-
wych: A, B - wyciskanie profilu pełnego i wyciskanie rur z wsadu
proszkowego wstępnie sprasowanego, C - wyciskanie materiału
proszkowego w osłonie („nabój”), D - wyciskanie sypkiego mate-
riału proszkowego [1, 3]
Fig. 1. General modes of extrusion of metallic powders
137
Wyciskanie na zimno metalicznych materiałów porowatych
sności wytrzymałościowe wsadu (umocnienie odkształ-
ceniowe).
W pierwszym etapie wyciskania występuje powolny
wzrost siły związany z „dogęszczaniem” wsadu [4].
Etap ten jest różny dla różnych ciśnień wstępnego pra-
sowania wsadu i ulega silnemu wydłużenie dla niższych
ciśnień. Charakterystyki siłowe procesu wykazują wy-
raźną zależność od wartości ciśnienia prasowania wsadu
(rys. 3), a wraz ze wzrostem tego ciśnienia podnosi się
maksymalny poziom siły konieczny do uzyskania wyro-
bu. Dzieje się tak jednak tylko dla mniejszych zagęsz-
czeń, po osiągnięciu ciśnienia krytycznego dalsze za-
gęszczanie wsadu powoduje wyraźne obniżenie siły
maksymalnej wyciskania, a dalej jej stabilizację (rys. 4).
Bardzo podobne charakterystyczne zmiany sił maksy-
malnych uzyskano w przypadku wszystkich badanych
wielkości odkształceń (dla współczynników wydłużenia
λ
= 4,9÷15,5), jedynie ich poziom był wyraźnie różny i
silnie wzrastał wraz ze wzrostem odkształcenia. Powyż-
sze wyniki znajdują potwierdzenie we wcześniejszych
publikacjach [5, 6].
Inne czynniki wpływające na siłę wyciskania to
wielkość ziarna proszku, z którego przygotowano wsad,
prędkość ruchu stempla, rodzaj smarowania oraz kształt
matrycy [5]. Zmiana prędkości w badanym zakresie
15÷120 mm/min praktycznie nie wywołała dodatkowych
efektów siłowych. Natomiast bardzo wyraźny jest
wpływ rodzaju proszku, a wzrost nawet o 50% siły wy-
ciskania (rys. 5) dla proszku 30 μm można tłumaczyć
ogólnie gorszą odkształcalnością takiego proszku, ale
również znacznymi trudnościami technicznymi przy
prowadzeniu próby.
710
700
690
680
670
660
650
60
0
150
300
450
600
Rys. 4. Wpływ ciśnienia prasowania wstępnego na wartość maksymalnej
siły wyciskania wsadu porowatego (średnica wyrobu 14 mm, frak-
cja 110 μm)
Fig. 4. The influence of compaction pressure on the maximum extrusion load
Ciśnienie prasowania pw, MPa
40
20
900
0
0
300
600
900
800
Ciśnienie prasowania p
w
, MPa
Rys. 2. Zależność twardości HB wsadu do wyciskania od ciśnienia pra-
sowania wstępnego
p
w
(RAL1, frakcja 30 μm)
Fig. 2. The influence of the compaction pressure on the compacts hardness
700
600
500
400
900
300
0
100
200
400
500
Wielkość ziarna, um
Rys. 5. Wpływ frakcji ziarnowej proszku RAL1 na wielkość maksymalnej
siły wyciskania współbieżnego na zimno (ciśnienie prasowania
wstępnego
p
w
= 75 MPa, średnica wyrobu 14 mm, prędkość stem-
pla 60 mm/min)
Fig. 5. The influence of the powder fraction on the load in the cold forward
extrusion
750
600
pw, MPa
450
25
300
75
150
150
Wyciskanie MMP ze wsadu sypkiego
Proszek zasypany bezpośrednio do recypienta prasy
jest poddawany w pierwszej fazie ruchu stempla jedno-
stronnemu prasowaniu. Wzrost siły jest powolny aż do
uzyskania poziomu umożliwiającego wyciskanie. W tej
fazie procesu dochodzi do ciasnego ułożenia ziaren,
zależnego m.in. od ich kształtu i wielkości tarcia między
nimi. Powstała wtedy nierównomierność zagęszczenia
(pokazana poprzez rozkład twardości HB na prze- kroju
0
0
15
30
45
Droga stempla, mm
Rys. 3. Wpływ ciśnienia prasowania wstępnego
p
w
na wielkość siły wyci-
skania wsadu z proszku RAL1 (matryca płaska, średnica wyrobu
11 mm, frakcja 110 μm)
Fig. 3. The influence of the compaction pressure on the extrusion load of
RAl 1 powder
138
M. Galanty
wsadu - rys. 6) nie ma istotnego wpływu na zmien- ność
tej własności na długości wykonanego wyrobu.
Natomiast zauważalne jest zwiększenie twardości na
przekroju poprzecznym przy powierzchni wyrobu
w stosunku do jego środka [7].
Poziom sił wyciskania
proszku sypkiego zależy od wielkości stopnia odkształ-
cenia i grubości krążka Al zamykającego otwór matrycy
(rys. rys. 7, 8), przy czym dobór grubości krążka ma
dodatkowe znaczenie dla jakości powierzchni wyrobu.
775
750
725
700
675
650
1,5
2
2,5
0
0,5
1
3
3,5
grubość krążka Al g, mm
Rys. 8. Wpływ grubości krążka zamykającego matrycę na wielkość siły
maksymalnej przy wyciskaniu na zimno sypkiego proszku RAL1
(frakcja 450 μm, średnica wyrobu 14 mm,
V
S
= 60 mm/min)
Fig. 8. The influence of the thickness of the die closing disk on the maxi-
mum extrusion load during cold extrusion of a loose Al powder
UWAGI KOŃCOWE
Przeprowadzone próby otrzymywania długich wyro-
bów z metalicznych materiałów porowatych na drodze
wyciskania bez udziału podwyższonej temperatury dały
zachęcające rezultaty. Korzystny wpływ wysokich trójo-
siowych naprężeń ściskających pozwala wykonywać
wyroby z materiałów trudno odkształcalnych,
a nawet sypkich. Szczególnie interesująca jest tu tech-
nika użycia jako wsadu mieszaniny różnych sypkich
proszków o składzie celowo dobranym pod kątem dal-
szych zastosowań.
Porównanie obu omawianych technologii pod kątem
wymaganych sił wyciskania nie wykazuje wyraźnych
różnic. Jednak wstępne prasowanie wsadu przed wycis-
kaniem umożliwia użycie smaru technologicznego, co
wydaje się istotne dla materiałów drobnoziarnistych,
natomiast materiały gruboziarniste (a nawet granulaty,
drobne ścinki itp.) zaleca się poddawać wyciskaniu
w stanie sypkim. Wpływ wyciskania na zimno na włas-
ności wyrobu zarówno pod względem ich poziomu,
jak i jednorodności jest korzystny, a dalsza ich zmiana
jest możliwa na drodze typowej obróbki cieplnej
w zależności od rodzaju stosowanego wsadu i przezna-
czenia.
Rys. 6. Rozkład twardości HB na wzdłużnym przekroju częściowo wyci-
śniętego wsadu z proszku RAL 1 (450 μm) sypkiego
Fig. 6. Distribution of hardness on the longitudinal cross section of partly
extruded compacts from the loose powder
1000
750
średnica wyrobu 16mm
14 mm
12 mm
10 mm
500
250
0
0
20
40
60
80
droga stempla,
mm
Rys. 7. Charakterystyki siłowe procesu wyciskania na zimno sypkiego
proszku RAL 1 (frakcja 450 μm, grubość krążka zamykającego
matrycę
g
= 1 mm ,
V
S
= 60 mm/min)
Fig. 7. Force characteristics of cold extrusion of loose aluminium powder
Praca finansowana ze środków KBN
(grant nr 7 T08B 002 17).
LITERATURA
[1]
German R.M., Powder Metallurgy Science, 2
nd
Edition,
Metal Powder Industries Federation, Princeton 1994.
[2]
Ishizaki K., Komarneni S., Nanko M., Porous Materials.
Process technology and applications, Kluwer Academic
Publishers, Dordrecht 1998.
[3]
Rutkowski W., Projektowanie właściwości wyrobów spie-
kanych z proszków i włókien, PWN, Warszawa 1977.
139
Wyciskanie na zimno metalicznych materiałów porowatych
[4]
Galanty M., Libura W., Compresibility of Metals Powder in
various
Journal of Materials Proccesing Technology, Special Issue -
Proc. of the Conf. Metal Forming 2002, Birmingham, Sep-
tember 2002 (w druku).
Modes
of
Deformation,
Mater.
Konfer.
EUROMAT’95, Padwa-Wenecja, Symp. G, 151-156.
[5]
Galanty M., Libura W., Zasadziński J., Evaluation of Force
Parameters for Aluminium Powder Extrusion, Advanced
Technology of Plasticity, Vol. III, Proc. 6
th
ICTP, Norym-
berga, Sept. 19-24, 1999, 1871-1876.
[6]
Galanty M., Zasadziński J., Prasowanie i wyciskanie mate-
riałów proszkowych o silnie zróżnicowanych własnościach
mechanicznych, Rudy i Metale Nieżelazne 1999, 44, 12,
672-675.
[7]
Galanty M., Kazanowski P., Kansuwan P., Misiolek W.Z.,
Consolidation of Metal Powders during Extrusion Process,
Recenzent
Marcin Leonowicz