Twoim problemem jest to, że powszechną NICOŚĆ mylisz z osobistą PUSTKĄ
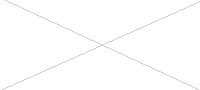
Istota jakości- twórcy koncepcji zarządzania jakością: Najważniejszymi prekursorami rozwoju koncepcji zarządzania jakością są:Walter Shewhart. Wynalazł najważniejsze narzędzie, jakim posługujemy się dziś w sterowaniu jakością- kartę kontrolną. Cykl Shewharta to zespół działań, polegający na wykrywaniu i usuwaniu poszczególnych czynników zakłócających przebieg procesu technologicznego. Wiliam Edwards Deming był pierwszym amerykańskim specjalistą, który w sposób metodyczny przekazywał japońskim menedżerom wiedzę na temat jakości. Upowszechnił w japońskich firmach statystyczne techniki kontroli jakości, a także ideę, którą pózniej nazwano TQM-em. Był zdecydowanym wrogiem kontroli, a swoje podejście do jakości totalnej określił w 14 tezach. Koncepcja Deminga opierała się na sterowaniu jakością procesów i produktów, które przebiegają w cyklu działań, zwanym „kołem Deminga”. Joseph Juran. Dla Jurana kompromis jest rzecza naturalną w przeciwieństwie do Deminga. Jednak 10 kroków do TQM-u ma ten sam sens, co 14 zasad Deminga, są tylko inaczej wyrażone. Wyakcentował dwie grupy działań w zakresie jakości:Czynności o charakterze kierowniczym i ekonomicznym, czynności o charakterze technicznym. Koncepcja Jurana opiera się na trzech aspektach: Kontroli jakości, Poprawy jakości, Planowaniu jakości Philip Crosby. Autor 4 podstaw zarządzania jakością, określanych absolutami: Jakość określa się jako zgodność ze specyfikacją, a nie jako dobry produkt. Jakość osiąga się przez profilaktykę, a nie poprzez ocenianie. Standard jakości oznacza brak usterek. Jakość mierzy się kosztem braku zgodności ze specyfikacją, a nie wskaźnikami. Tengchi Taguchi, stworzył min teorię zarządzania przez kompleksowe wyniki. Jednak główną jego teorią była funkcja strat jakości oparta na projektowaniu eksperymentów. Idea ta polega na takim dopasowaniu procesów i produktów do krzywych jakości, aby straty związane z ich niepokrywaniem się były jak najmniejsze. Genichi Taguchi wniósł wiele do nauki o jakości. Szczególnymi jego osiągnięciami są: Funkcja strat jakości. Sterowanie jakością off-line. Projektowanie eksperymentów Środowisko zarządzania jakością- kontrola jakości, sterowanie jakością, zapewnienie jakości, TQM, Kaizen, 5S. Zarządzanie jakością obejmuje planowanie strategiczne, rozmieszczenie zasobów i inne systematyczne działania na rzecz jakości, takie jak: planowanie jakości, sterowanie jakością oraz doskonalenie czyli ciągłą poprawę. System zapewniania jakości to ramy, które ukierunkowują i ułatwiają działania zmierzające do najwyższej jakości. TQM to sposób zarządzania organizacją skoncentrowany na jakości. TQM składa się z 3 elementów: Koncentracji działalności przedsiębiorstwa na potrzebach klienta. Kompleksowego stylu myślenia. Oraz współdziałania wszystkich pracowników przedsiębiorstwa. TQM jest to przede wszystkim rodzaj kultury przedsiębiorstwa bazującej na umiejętności pracy zespołowej. Juran opracował 10 zasad przejścia do TQM: Uświadomienie potrzeby i szansy doskonalenia jakości. Ustalenie celów ciągłego doskonalenia. Stworzenie organizacji, która pomoże w realizacji tych celow, poprzez powołanie rady do spraw jakości, określenie problemów, wybranie odpowiedniego projektu stworzenie zespołów i wybór koordynatorów. Przeszkolenie wszystkich pracowników. Przydzielenie zadań problemowych. Informowanie o przebiegu prac. Okazanie uznania. Ogłoszenie wyników. Odnotowanie sukcesów. Włączenie usprawnień do normalnie stosowanych systemów i procesów firmy, co zapewnia podtrzymanie zapału pracowników. Kaizen. Można ją scharakteryzować jako: metodę ciągłego doskonalenia, niekończące się poszukiwanie doskonałości, proces stałej poprawy jakości produktów, dążenie pracowników do doskonalenia wszystkich aspektów działalności organizacji. Stosowanie Kaizen koncentruje się na ciągłym doskonaleniu wyrobów, procesów zachodzących w organizacji. Proces Kaizen obejmuje: Ciągłą obserwację i poszukiwanie problemów, Analizę i definiowanie problemów, Poszukiwanie przyczyn, Przygotowanie rozwiązania, Wypróbowanie w praktyce i poszukiwanie nieprawidłowości, Wdrożenie i kontrola wyników, Standaryzację. Filozofię Kaizen określa 10 zasad: Problemy stwarzają możliwości. Pytaj 5 razy „Dlaczego” Bierz pomysły od wszystkich. Myśl nad rozwiązaniami możliwymi do wdrożenia. Odrzucaj ustalony stan rzeczy. Wymówki, że czegoś nie da się zrobić są zbędne. Wybieraj proste rozwiązania- nie czekając na te idealne. Użyj sprytu zamiast pieniędzy. Pomyłki koryguj na bieżąco. Ulepszenie nie ma końca. 5S. zamiarem 5S jest spowodowanie wzrostu produktywności poprzez wprowadzenie powszechnego w firmie nawyku porządku i czystości. Interpretacja 5S: Selekcja, Systematyka, Sprzątanie, Schludność, Samodyscyplina. Znormalizowane systemy zarządzania, przegląd norm i zakres ich stosowania. System zarządzania jakością: ISO 9000 Normy wspomagające zarządzanie: ISO 10000 Wewnętrzny system kontroli: ISO 19000 Systemy zarządzania środowiskowego: ISO 14000 Bezpieczeństwa i higieny pracy-BHP: PN-N 18000 Przemysł motoryzacyjny: ISO/TS 16949 Przemysł zbrojeniowy: NATO-AQAP, ANSI-N 45-2 Przemysł lotniczy: EN 9100 Przemysł medyczny: EN 46000, ISO 15378, ISO 13480 Przemysł spożywczy: ISO 22000, ISO 15161, ISO 24276 Transport: PN-EN 12798 Bezpieczeństwo informacji: BS 7799 Normy międzynarodowe ISO: ISO 27000 Społeczna odpowiedzialność: FTC 101 Zarządzanie jakością w przedsiębiorstwie- pomiary i ocena, wpływ na niezawodność i bezpieczeństwo wyrobu. W inżynierii produkcji jakość akcentowana jest przede wszystkim jakością wyrobu, z silnym podkreśleniem, że konsument jest głównym weryfikatorem tej jakości i określa, w jakim stopniu spełnia ona jego oczekiwania. W kontekście jakości produktu najczęściej wymieniane są cechy jakości technologicznej: Funkcjonalność. Praktyczność. Niezawodność. Trwałość. Bezpieczeństwo użytkowania. Jakość, jak każdą działalność zarządzania, należy oceniać i mierzyć. Ocenianie jakości jest najczęściej dokonywane przez audity wewnętrzne i zewnętrzne, natomiast do bezpośredniego pomiaru stosuje się tzw instrumenty doskonalenia jakości. Narzędzia pomiaru: tradycyjne: schemat blokowy, diagram Ishikawy, diagram Pareto, histogram, karty kontrolne, wykresy zmiennych, arkusze kontrolne; nowe: diagram pokrewieństwa, dagram relacji, macierzowa analiza danych,diagram systematyki, diagram macierzowy, wykres decyzji, wykres sieciowy. Proces pomiaru jest kluczowym elementem wykorzystywanym podczas prowadzenia procesu oceny jakości produktu programowego oraz procesów jego wytwarzania. Niezawodność określana jest jako prawdopodobieństwo zdarzenia, które polega na tym, że wyrób użytkowany w określonych warunkach, będzie zachowywał zdolność do spełnienia stawianych mu wymagań w określonym przedziale czasu użytkowania. Za bezpieczeństwo wyrobów wprowadzonych na rynek odpowiada bezpośrednio zarówno producent jak i dystrybutor. Bezpieczeństwu służą też przepisy prawne, za przestrzeganie, których odpowiadają instytucje państwowe Podejście nowe i globalne do harmonizacji technicznej i normalizacyjnej- dyrektywy oraz normy zharmonizowane. . Zniesienie barier technicznych w handlu jest bardzo istotnym elementem w skali globalnej. Przepisy techniczne dotyczą zazwyczaj ochrony dóbr publicznych np. zdrowie, bezpieczeństwo, ochrona środowiska. Przepisy techniczne zawierają ogólne specyfikacje dotyczące: wyrobów, procesów i usług, sposobu ich wytwarzania, parametrów eksploatacji. Są obowiązkowe i muszą być spełnione przed wprowadzeniem wyrobu do obrotu i oddaniem do użytku na rynku UE. Filozofia nowego podejścia pozwala na utrzymanie aktualnego poziomu techniki i rozwój nowych technologii. Nowe podejście zostało uzupełnione dodatkowymi zasadami, ustanawiającymi Globalne Podejście do badań i certyfikacji, co pozwoliło na wprowadzenie spójnego podejścia do procedur oceny zgodności. W globalnym podejściu określono wytyczne dotyczące stosowania ocen zgodności w dyrektywach harmonizacji oraz zdefiniowano zasady: Nanoszenia i stosowania oznakowania zgodności CE wraz z formą graficzną. Stosowania norm dotyczących zapewnienia jakości. Promowania i stosowania systemu akredytacji. Dyrektywy NP dotyczą zagadnień związanych z bezpieczeństwem użytkowania, ochroną zdrowia i ochrona środowiska. Określają zagrożenia, które producent powinien wykryć i wyeliminować. W dyrektywach nowego podejścia nie zawarto szczegółowych specyfikacji technicznych dla wyrobów, są one opracowane na gruncie normalizacji, jako normy zharmonizowane. Norma zharmonizowana. Norma może zawierać inne przepisy, nie tylko te związane z zasadniczymi wymaganiami. Norma zharmonizowana nie koniecznie obejmuje wszystkie zasadnicze wymagania danej dyrektywy w odniesieniu do wybranego wyrobu. Zastosowanie norm zharmonizowanych i odwołanie się do nich jest najłatwiejszym i najprostszym sposobem zapewnienia zgodności wyrobu z zasadniczymi wymaganiami określonej dyrektywy. Wprowadzenie wyrobu do obrotu towarowego wyrobów oraz nadzorowanie i monitorowanie rynku. Oddanie do użytku ma miejsce w momencie, gdy wyrób jest po raz pierwszy użyty przez konsumenta. Wyrób w momencie wprowadzania do obrotu lub oddania do użytku musi być zgodny z zasadniczymi wymaganiami ustanowionymi w dyrektywach, mających do niego zastosowanie. Łańcuch dostaw jest istotny ze względu na podział odpowiedzialności różnych podmiotów działających na rynku. Na łańcuch dostaw składają się: producent, upoważniony przedstawiciel, dystrybutor, importer, operatorzy gospodarczy. Z założenia nadzór rynku odnosi się jedynie do wyrobów obecnych na rynku. Celem nadzoru rynku jest zapewnienie, że przepisy odpowiednich dyrektyw mają zastosowanie na terenie całej UE. Obywatele państw członkowskich mają prawo do tego samego poziomu ochrony na terenie całego wspólnego rynku, niezależnie od pochodzenia wyrobu. Ponadto, nadzór rynku jest bardzo ważny dla interesu podmiotów gospodarczych, gdyż pomaga w zwalczaniu nieuczciwej konkurencji. Celem monitorowania wyrobów wprowadzonych do obrotu jest sprawdzenie, że są one zgodne z wymaganiami odpowiednich dyrektyw w momencie, gdy są wprowadzane do obrotu oraz, jeżeli to właściwe, gdy są oddawane do użytku. Modułowe systemy oceny zgodności, deklaracja zgodności oraz obowiązki i odpowiedzialność producenta. Ocena zgodności powinna przebiegać w sposób, który zależy od ryzyka związanego z wyrobem. Procedury oceny zgodności- moduły, które mają zostać zastosowane powinny być wybrane przez producenta spośród modułów: wewnętrzna kontrola produkcji- obejmuje wewnętrzną kontrolę projektowania i produkcji. Badanie typu WE- obejmuje fazę projektowania i musi zostać uzupełniony modułem przewidującym przeprowadzenie oceny w fazie produkcji. Zgodność z typem- obejmuje fazę produkcji i uzupełnia moduł B. obejmuje zapewnienie zgodności z typem opisanym w certyfikacie badania typu WE. Zapewnienie jakości produkcji- obejmuję fazę produkcji i uzupełnienia moduł B. system jakości na etapie produkcji oraz kontroli końcowej i badań wyrobu. Zapewnienie jakości wyrobu. Weryfikacja wyrobu. Weryfikacja jednostkowa. Pełne zapewnienie jakości. Proces oceny zgodności może być przeprowadzony przez stronę pierwszą- producenta lub przez stronę trzecią- jednostkę notyfikowaną. Przed wprowadzeniem wyrobu na rynek producent jest zobowiązany do: Sporządzenia dokumentacji technicznej wymaganej dla wyrobów. Dokonać analizy zagrożeń i oceny ryzyka. Wykonać tłumaczenie dokumentacji oraz czas jej dostępności. Jeżeli wymaga dyrektywa, uzyskać certyfikat ocenie zgodności, badania typu WE, w jednostce notyfikowanej. Stworzyć deklarację producenta, tzw deklarację zgodności WE. Dokumentacja techniczna wymagana dla wyrobów. Dokumentację musi sporządzić producent, gdyż jest jedyną osobą znającą wyrób od fazy projektowej po produkcję i użytkowanie. Analiza zagrożeń i ocena ryzyka. Ocena ryzyka jest kluczową częścią procedury zastosowanej przez producenta w celu zapewnienia, że jego wyrób nie niesie ze sobą niemożliwego do zaakceptowania poziomu ryzyka dl zdrowia i bezpieczeństwa osób, zwierząt domowych oraz mienia.
Etapy wdrażania Systemu Zarządzania Jakością wg ISO 9001 Wdrożenie SZJ można podzielić na dwie fazy:
przygotowanie do wdrożenia SZJ, wdrożenie SZJ
Do głównych etapów fazy przygotowawczej należy zaliczyć:
Powołanie odpowiedniego zespołu ds. realizacji przedsięwzięcia -ok. 2 dni
Ustalenie jakie są wymagania odnośnie wdrażanego systemu - ok. 2 dni
Przeprowadzenie analizy funkcjonowania aktualnego systemu zarządzania dla firm już istniejących na rynku- 3-7 dni
Ustalenie różnic pomiędzy stanem faktycznym a założonymi wymaganiami systemu - ok. 3 dni
Identyfikacja procesów w przedsiębiorstwie - 5-7 dni
Faza przygotowawcza to najważniejsza część podczas wdrażania Systemu Jakości zgodnego z wymaganiami , ponieważ determinuje ona termin wdrożenia systemu oraz jego skuteczność.
Fazie wdrożeniowej towarzyszą:
Opracowanie planu wdrożenia - 2 dni
Realizowanie działań założonych w planie ok. 6-10 miesięcy):
pierwsze szkolenie dla zarządu i kadry
szkolenia dla zespołu wdrożeniowego
szkolenia kandydatów na auditorów wewnętrznych
szkolenie pracowników (łącznie ok. 13 dni)
nadzór i weryfikacja wdrożenia SZJ -minimum 3 :miesiące
Zorganizowanie i przeprowadzenie pierwszego auditu wewnętrznego - 1-3 dni
szkolenie po wykryciu niezgodności - ok. 3 dni
przeprowadzenie działań korygujących - w zależności od wagi - ok. 1-15 dni
Przygotowanie do procesu certyfikacji ( wybór jednostki certyfikacyjnej) - 2-4 dni
Audit certyfikujący - 1-3 dni