Twoim problemem jest to, że powszechną NICOŚĆ mylisz z osobistą PUSTKĄ
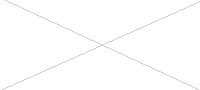
METODA RZ – (czyste rozpylanie) stosowana do wykonywania proszków z materiałów wysokotopliwych (zgorzelina na surowce) głównie do produkcji proszków żelaza. Metoda ta jest dwu stopniowa: 1) rozpylanie i uzyskiwanie proszku 2) wytwarzanie gotowego proszku. Materiał wsadowy: 1) stosujemy żeliwo stopione (1350 – 1400) do 3.5% C 2) złom stalowy (czysty produkt końcowy) Si, Mn, P<1%, S<0.03%. O stopniu utlenienia decyduje odległość od Listra wody materiału wyjściowego, ciśnienie powietrza 5 – 8 atm Nastepnie stosuje się redukcje w temp. 850 – 1150 C, 3fe3O4+10Fe3C – 3Fe+8CO2+2CO2. CO – atmosfera ochronna, wymagana szczelna komora WYGLĄD proszku: - proszki te są tanie (z uwagi na surowiec wyjściowy) – bardzo wydajny proces – kształt kulisty gąbczasty – b. dobre właściwości technologiczne, – Możliwa regulacja kształtu cząstek poprzez : (-napięcie powierzchniowe całego żeliwa -lepkość -skład chemiczny -średnice strumienia wypływającego żeliwa -ciśnienie strumienia powietrza) Zaleca się aby siarki było mniej niż 0.03%. im większa zawartość siarki tym ziarna bardziej zniekształcone – im mniejsza zawartość siarki tym kształt bardziej zbliżony do kuli.
METODA D – do rozpylania proszku żelaza. Dysza obrotowa – im wieksza prędkość tym drobniejszy proszek (6000 obr/min) metoda chetnie stosowana nie – wymagająca redukcji
Rozpylanie proszku w łuku elektrycznym :
Można wytwarzać proszki: Fe, Zn , Mg, Be węgliki, azotki, ceramikę – można uzyskac proszki kuliste i płatkowe (duże zróżnicowanie pod względem kształtu) – zależy to od prędkości obrotowej elektrody dolnej (wieksza prędkość obrotowa i bliższe położenie powoduje powstawanie proszku płatkowego)
Preszpan – zabezpiecza przed przyklejaniem się proszku do ścianek. Proszek produkowany jest ze stopionej elektrody ciekły metal wyrzucany jest przez obracającą się elektrodę i uderza o ścianki i wpada do wody. ATMOSFERY Ar – mały spadek potencjału łuku elektrycznego przypadający na jednostkę łuku (nie wymaga regulacji odległości elektrod) –niska przewodność cieplna (trudno uzyskać kuliste proszki) He – duży spadek potencjału łuku elektrycznego na jednostkę łuku (wymaga precyzyjnej regulacji odległości elektrod) – większa przewodność cieplna (łatwo uzyskać cząstki kuliste) Ar+He – średni spadek potencjału. Metoda opracowana przez Szwedów – nie stosowana w Polsce – strumień gazu jest poddany drganiom o wys. Częstotliwości (generatory Hassmana) – jednostopniowe rozpylanie – bardzo wydajne = można uzyskać różne wielkości cząstek
PROSZKI GĄBCZASTE I STRZĘPIASTE uzyskuje się głównie metodą redukcji np. redukcja wysokotemperaturowa – odpowiedni piec z muflą – najczęściej przeprowadza się redukcje wodzie Stosowanie: - proszki wolframu, molibdenu, kobaltu = proszki wykonywane innymi metodami, dłużej składowane i utleniane
Parametry: - temperatura redukcji – czas redukcji - atmosfera Temperatura i czas – parametry które ze sobą współpracują im krótszy czas tym wyższa temp. i na odwrót. Atmosfery dzielimy na: -gazowe(wodór H2,zdysocjowany amoniak NH3, mieszanina CO I CO2, pary metali alkalicznych) – stałe (magnez Mg, wapń Ca, aluminium Al.) zamyka się proszek z reduktorem w odpowiedniej temp proces reakcji przebiega samorzutnie. Redukcja we wzniosie – fluidyzacja – proszek jest unoszony w odpowiedniej temp. najczęściej przez wodór – bardzo dokładny styk proszku ze środkiem redukującym, Nie występuje zjawisko aglomeracji, szybki proces redukcji, proszek o wielkości 0.1um
REDUKCJA W CIECZY: 1) redukcja w roztworach wodnych 2) redukcja w stopionych solach ad1 otrzymuje się głównie proszek Cu przez wytrącanie metalami stojącymi niżej w szeregu napięciowym *utwarza się proszek Cu, Ni, Co, Pb, Bi przez wytrącenie wodorem lub innymi gazami *redukcja miedzi z roztworu siarczanu ad2 metodę tą stosujemy do wytwarzania głównie proszku Be, Th, Cr, Zr. Schemat wytwarzania proszku żelaza metodą Hegnes Mat. wyjściowy(wapno, węgiel, magnetyt)- piec indukcyjny (1200 C 24 - 40 h) – spieczona gąbka – mielenie (160um) - separacja magnetyczna – mielenie i przesiewanie (100 um) – separacja magnetyczna – wyżarzanie – proszek Fe. Wsadem do tej metody są magnetytowe rudy (żelaza). Ośrodkiem redukującym jest węgiel i koks. Redukcja zachodzi w piecu tunelowym o długości 17m ogrzewanym gazem ziemnym. Czas redukcji do 40 h w wyniku otrzymujemy spieczoną gąbkę (97.5% Fe) Następnie gąbka jest myciu w siarczku wapnia CaS. Po myciu gąbka jest kierowana do mielenia zgrubnego następnie drobne mielenie z przesiewaniem po czym podlega separacji magnetycznej i przesiewane do uzyskania określonej wielkości w celu uzyskania wyższej czystości poddaje się je dodatkowej redukcji. Proszki są gąbczaste i mają b. dobrą zagęszczalność.
WYTWARZANIE WISKERÓW: wiskery – kryształy prawie całkowicie pozbawione defektów sieci krystalicznej. Średnica wiskerów wynosi około 1um o różnej ograniczonej długości. Metody:- redukcja soli metali –kondensacja z par metali –elektrolityczne osadzanie z roztworów. –najczęściej redukcja halogenków metali. Do metod najbardziej rozwijających się należy : 1)rozpylanie metodą ultradźwiękową 2)met. autoparowania i kondensacji 3) met. dysocjacji 4) met. korozji międzykrystalicznej 5)met. samorozpadu proszku 6)met. ZOL-ŻEL 7)met. mechanicznego stopowania
MECHANICZNE STOPOWANIE MA: inaczej mielenie na sucho w młynach wysokoenergetycznych. Podczas mechanicznego stopowania zachodzą oddziaływania w miejscach styku powstają mikronaprężeniaZjawiska
PRASOWANIE PROSZKÓW METALI- (główny proces technologiczny w procesie metalurgii)- jest to zwiększanie gęstości pozornej masy proszku ( zagęszczanie lub zgęszczanie ) z równoczesnym nadaniem kształtu. Wszystko zachodzi w matrycy za pomocą siły F. Zasady prasowania: - siła F ruch posuwisto zwrotny – przynajmniej jeden stempel prasujący uruchamiany przez prace hydrauliczną lub mechaniczną. Efektem jest kształtka lub wypraska – wypychanie – podczas prasowania następuje zakleszczanie wypraski. Proszek podczas prasowania jest to tzw. ciecz niedoskonała (nie stosuje się prawo Pascala dla cieczy) ciśnienie ma straty 0.3 – 0.4 P Straty powoduje tarcie: - proszek – ścianki matrycy; proszek – stempel; proszek – proszek. Zjawiska: -zbliżanie się cząstek na odległość działania sił adhezji – powiększanie się powierzchni styku cząstek przez ich wzajemne zbliżenie -powiększenie powierzchni styku cząstek przez ich odkształcenia trwałe –mechaniczne zazębianie się proszków – usuwanie powłok tlenkowych na powierzchni cząstek – lokale powstawanie wysokich temp. ze względu na ciśnienie – gniot proszku który przy proszkach plastycznych wiąże się z odkształceniem, przy kruchych z pękaniem i kruszeniem proszków.
ZJAWISKA W CZASIE PRASOWANIA WEDLUG MISSOLA: -luźno zasypany proszek (dopasowanie cząstek do siebie poprzez obroty i załamywanie się mostków)- proszek częściowo sprasowany – proszek mocno sprasowany. Przygotowanie proszku do prasowania: 1)przechowywanie proszków: magazynowanie w odpowiednich zasobnikach hermetycznie zamkniętych lub w atmosferach ochronnych (ciemniejszy proszek – większy stopień utlenienia) 2) wyżarzanie redukcyjne – przeprowadza się w atm. Wodoru w temp. zazwyczaj 0,4 – 0,5 Ttop -zbyt wysoka temp. prowadzi do zbrylenia proszku. Cel wyżarzenia redukcyjnego: - redukcja tlenków –rafinacje zanieczyszczeń –usuniecie skutków odkształcenia proszków –rekrystalizacja struktury –wygładzenie powierzchni –odwodorowanie. 3) wyżarzanie dyfuzyjne –ujednorodnianie mieszaniny
METODY KSZTAŁTOWANIA RÓŻNYCH KSZTAŁTÓW WYROBU:
1-stronne prasowanie(spieki, metoda konwencjonalna ) 2-stronne (-nierównomierny rozkład gęstości –ograniczenia co do wielkości i kształtu wyprasek –nie można uzyskać zbyt grubych wyprasek średnica max 35cm) Prasowanie izostatyczne na zimno i na gorąco: (-w ten sposób można uzyskac wypraski charakteryzujące się równomierną gęstością –bez ograniczeń kształtowych i objętościowych –bardzo kosztowna metoda –niebezpieczna metoda Prasowanie na gorąco: (drogie oprzyrządowanie –nadaje się tylko do prasowania dużych wyrobów o prostych kształtach –wysoka gęstość o równomiernym rozkładzie –mała ilość zaprasowanego powietrza) Prasowanie kroczące: (możliwość uzyskania dużej gęstości – właściwości wyrobu zależą od prędkości przesuwu koryta i buta –zależą również od siły nacisku buta –możliwe usunięcie dużej ilości powietrza –możliwość wykonania prętów, taśm) Prasowanie obwiedniowe (-uzyskanie dużej gęstości –stempel wykonuje ruch wahadłowy) Walcowanie proszków – (możliwości prasowania bimetali, trimetali) Odlewanie gęstwy (otrzymuje się produkty bardzo porowate)