Twoim problemem jest to, że powszechną NICOŚĆ mylisz z osobistą PUSTKĄ
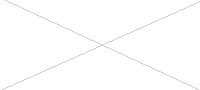
1. Klasyfikacja maszyn:
a) Technologiczne - służą do zamiany kształtu obrabianych przedmiotów (np. obrabiarki, walcarki) lub fizycznych własności i stanów obrabianych materiałów i przedmiotów (np. maszyny budowlane, ceramiczne, hutnicze, górnicze, rolnicze, przemysłu chemicznego, spożywczego).
b) Transportowe - maszyna robocza przenosząca przedmioty lub istoty żywe bez dokonywania w nich przemian. Dzielą się na maszyny transportowe o zasięgu ograniczonym (np. przenośniki, dźwignice), o zasięgu nieograniczonym (np. samoloty, samochody)
c) Energetyczne - służą do zamiany jednego rodzaju energii w drugi np. silniki, prądnice lub zwiększenia energii czynnika np. pompy, wentylatory, sprężarki.
2. Układy napędowe maszyn technologicznych, transmitancja energii:
Moc z silnika poprzez przekładnię pasową przenoszona jest na wał szybkoobrotowy reduktora. Przekładnia pasowa zmniejsza prędkość obrotową, a tym samym zwiększa moment M1n1 = M2n2. Drugi stopień zwiększenia momentu występuje na reduktorze, gdzie następuje zmniejszenie prędkości do wartości odpowiadającej zapotrzebowaniu. Sprzęgło służy do połączenia wału wyjściowego reduktora z wałem roboczym maszyny (pełni również funkcje bezpieczeństwa).
10. Kształtowanie na etapie projektowania oraz wytwarzania wysokiej trwałości elementów maszyn technologicznych narażonych na intensywne zużywanie.
-w dziedzinie konstrukcji - przez należyty dobór materiałów i ich kształtów do obciążeń, kształtowanie nacisków jednostkowych, dobór materiałów i tworzyw na pary trące,
wyeliminowanie tarcia suchego, szerokie stosowanie odpowiednich uszczelnień , zapewnienie
odpowiedniej temperatury;
-w dziedzinie technologii - przez wybór optymalnego rodzaju obróbki, kształtowanie
optymalnej warstwy wierzchniej, wybór właściwej obróbki cieplnej i cieplno-chemicznej,
prawidłowy montaż i regulacje;
Wzrost wymogów charakterystyk technicznych wymusza zwiększenie odporności materiałów na działanie czynników fizycznych, chemicznych i zużyć od obciążeń. W związku z tym stosuje się lepsze materiały lub zwiększ odporność warstwy wierzchniej.
Materiały o dużej wytrzymałości, małym przewodnictwie cieplnym, dużej zdolności do
umocnienia podczas obróbki plastycznej są materiałami trudno obrabialnymi. Z tego powodu czasami trzeba stosować materiały gorsze o lepszej obrabialności.
Algorytm kształtowania własności powierzchni:
1. Dobór rodzajów i wartości liczbowych własności użytkowych dla znanych parametrów fizycznych, chemicznych i przewidywanych obciążeń;
2. Dobór wartości liczbowych poszczególnych cech warstwy wierzchniej dla założonych własności użytkowych;
3. Dobór takich sposobów obróbki zapewniających uzyskanie zakładanych cech warstwy wierzchniej oraz dobór parametrów przewidywanych zabiegów obróbczych;
4. Wybór sposobu obróbki, zapewniającego najniższe koszty wytwarzania oraz możliwego do
zrealizowania w zakładzie przemysłowym przewidzianym do wytwarzania elementów;
5. Badania jakościowe zespołu wytwarzanego według przyjętej technologii;
6. Korygowanie wartości liczbowych własności użytkowych (rezultat badań) i projektowanie
procesu technologicznego według punktów 2-5.
3. Znaczenie scalania oraz rozdrabniania materiałów ziarnistych w technice, ogólna charakterystyka maszyn stosowanych do realizacji tych procesów:
Scalanie materiałów drobnoziarnistych to procesy fizykochemiczne i fizykomechaniczne zapewniające formowanie cząstek określonych rozmiarach, kształcie, strukturze oraz właściwościach fizycznych. W ogólnych przypadkach scalanie składa się z następujących procesów technologicznych:
-przygotowanie wyjściowego surowca
-dozowanie i mieszanie składników
-tworzenie aglomeratu
-utrwalenie struktury aglomeratu
-sortowanie
-rozdrabnianie dużych frakcji i końcowe wyodrębnianie produktu
Główne powody scalania materiałów drobnoziarnistych:
-przygotowanie umożliwiające wykorzystanie ich w określonych procesach produkcyjnych
-przygotowanie odpadowych materiałów drobnoziarnistych związane jest z reguły z koniecznością ich zbrylenia
-poprawa bilansu energetycznego prowadzonego procesu technologicznego
-efektywniejsze wykorzystywanie urządzeń transportowych, magazynowych, składowisk
-zapobieżenie pyleniu materiałów drobnoziarnistych podczas transportu i składowania
-poprawa walorów użytkowych produktu
Przykładowe gałęzie przemysłu oraz materiałów poddawanych scalaniu:
przemysł farmaceutyczny lekarstwa tabletki
wydobywczy scalanie węgla brunatnego, miału
hutniczy osady szlamów, szlamy konwertorowe, pyły wielkopiecowe
metalurgiczny scalanie proszków metalurgicznych
chemiczny nawozy sztuczne
paliwowo-energetyczny węgiel drzewny, torf, trociny, słoma
obróbka metali wióry, szlamy poszlifierskie
Metody scalania: spiekanie(metoda termiczna), brykietowanie (w prasie stemplowej, walcowej),
Grudkowanie( granulatory talerzowy, bębnowy, odśrodkowe, łopatkowe), granulacja dwustopniowa (materiał pylisty-nieregularne wypraski-kruszenie)
Prasa stemplowa jest gorsza od walcowej, ponieważ występuje dużo ruchów jałowych, wycofywanie stempla, wyjmowanie wypraski. W prasie walcowej osiągamy większą wydajność, ciągły charakter pracy, zwartość konstrukcji, mniejsze zużycie energii, dłuższa żywotność elementów formujących.
Rozdrabnianie jest to proces w następstwie którego następuje zmniejszenie rozmiarów ziaren od wyjściowych wielkości do żądanych.
Kruszenie jest to rozdrabnianie grubszych brył i ziaren, na ziarna mniejsze o wymiarach większych niż 1mm. Gdy ziarna mniejsze od 1mm to mielenie.
Maszyny do rozdrabniania działają przez zgniatanie, ścinanie(ścieranie), łamanie, rozłupywanie.
Do skał twardych( skały manganowe, krzemowe) stosuje się kruszarki pracujące na zasadzie ściskania tj. szczękowe i stożkowe.
Do skał średnio twardych (wapienie, dolomity, sól kamienna) stosuje się kruszarki szczękowe, stożkowe, wirnikowe i walcowe.
Do skał miękkich (gliny, sole) kruszarki walcowe uzębione i kołognioty.
4. Podstawy aglomeracji ciśnieniowej materiałów drobnoziarnistych, budowa pras walcowych oraz obszar ich stosowania.
Brykietowanie - aglomeracja ciśnieniowa, w wyniku działania sił następuje zbliżanie się i klinowanie ziarn, powstają wiązania mechaniczne i chemiczne. Powstaje zwarta struktura o określonej wytrzymałości mechanicznej. Innym sposobem jest brykietowanie w prasie stemplowej jednak występuję tam dużo ruchów jałowych poprzez wycofywanie stempla.
Budowa prasy: Dwa walce posiadające tą sama średnice, walce obracają sie w przeciwnych kierunkach. Jeden z walców jest zamocowany na stałe, a drugi może się przesuwać - jest elastycznie podparty. Nad walcami znajduję się podajnik surowca czyli jest to albo zwykły zbiornik lub podajniki wymuszone (ślimakowe).
I – strefa podawania II – strefa spadku swobodnego III – strefa zagęszczenia IV – strefa zgniotu
rozkrusza a część tworzy gotowy materiał
4-strefa sprężystego rozprężania produktu
Prasy walcowe charakteryzuje wysokie ciśnienie prasowania, duża wydajność (liczona w tonach) i sprawność, a także odporność na zużycie narzędzi. Znalazły zastosowanie przy masowym prasowaniu materiałów drobnoziarnistych o właściwościach ściernych. Najczęściej są to materiały pochodzenia górniczego występujące w dużych ilościach, takie jak rudy i koncentraty metali, miał, szlam i pył węglowy.
Zalety takich urządzeń: -zwartość konstrukcji -ciągły charakter pracy -możliwość uzyskania dużej wydajności -mniejsze zużycie energii -dłuższa żywotność elementów formujących w porównaniu z prasami stemplowymi
Efektywność procesów scalania materiału realizowanego w tych urządzeniach określają wskaźniki jakościowe otrzymanych brykietów:
-wytrzymałość na ściskanie
-gęstość
-wytrzymałość na zrzut
-inne,
oraz wskaźniki techniczno-ekenomiczne urządzenia:
-zapotrzebowanie mocy na realizacje procesu
-wydajność prasy
-zużycie energii na jednostkę produkcji finalnej
-trwałość elementów formujących
5. Podstawy aglomeracji nawarstwiającej materiałów pylistych. Budowa i przykłady zastosowań granulatorów talerzowych i bębnowych.
Aglomeracja nawarstwiająca- polega na utworzeniu aglomeratów z równomiernie zwilżonych cząstek lub na nanoszeniu warstw suchych cząstek na wilgotne zarodki - centra granulek. Proces ten zachodzi w wyniku działania kapilarno-adsorbcyjnych sił pomiędzy cząstkami i przez następne zagęszczenie struktury wywołane siłami międzycząsteczkowymi w gęstej warstwie dynamicznej, np granulatorze bębnowym, talerzowym i innych. Produkt po metodzie otaczania ma określony kształt, właściwości i strukturę. Przykłady materiałów scalanych: odpadowy gips, szlamy konwertorowe, szlamy poszlifierskie, surowy tlenek cynku.
Mechanizm tworzenia granulek:
1) zmniejszenie surowego materiału z zawrotami i środkiem wiążącym
2) tworzenie granulek z drobnych cząstek i rozdrabnianie większych bryłek
3) otaczanie i zagęszczenie granulek w wyniku ich przemieszczenia na powierzchni urządzenia
4) utrwalanie wiązań w wyniku przejścia fazy ciekłej w stałą (stabilizacja struktury granulki)
Granulatory:
1) rotacyjne (talerzowe, bębnowe, odśrodkowe, łopatkowe)
2) taśmowe
3) wibracyjne
Możemy wyróżnić ruch wodospadowy oraz ruch spiralny granulatora. Granula na powierzchni prostopadłej wykonuje ruch wodospadowy, natomiast na powierzchni równoległej - spiralny.
Granulator talerzowy:
Granulatory talerzowe z powodu ich naturalnego przystosowania do pracy ciągłej (klasyfikacja wielkościowa granulek) są chętniej stosowane w praktyce przemysłowej. Są one m.in. wykorzystywane do granulacji różnego rodzaju odpadów, które można potem wykorzystać jako surowce wtórne lub nawozy.
Zalety: nie ma konieczności stosowania sztywnych fundamentów, prosta budowa, dobre ustawienie parametrów (kąt pochylenia, prędkość bębna) spowoduje dokładne wymiaru granulki)
Wady: wydajność ściśle powiązana z wielkością.
Granulator bębnowy:
Zalety: bardzo duża wydajność do 600 000 kg/h, scalanie różnych materiałów, segregacja gotowego produktu (dotyczy granulatorów typu Dela)
Wady: bardzo duża masa, wymagają mocnych fundamentów, zajmują dużą powierzchnie, potrzeba dużego silnika, produkt końcowy nie posiada jednolitego rozkładu ziaren.
Granulator bębnowy stawiany jest na równo pod względem wydajności z granulatorem talerzowym.
6. Maszyny do wstępnego, średniego i drobnego kruszenia surowców skalnych, budowa oraz podstawy eksploatacji:
kruszarki szczękowe - stosowane do wstępnego i wtórnego kruszenia materiałów o małej i średniej podatności na rozdrabnianie (granit, bazalt, sjenit, porfir). W kruszarkach szczękowych rozdrabnianie następuje poprzez zgniatanie, ścinanie i zginanie brył nadawy (podawanego materiału) między szczęką stałą a ruchomą, stopień rozdrobnienia 2 – 6;
Charakteryzują się dużą prostotą w budowie i niezawodnością działania. Zasadnicze części: - korpus głównym- wał mimośrodowym- szczęka ruchoma i nieruchoma – korbowód - płyty rozporowe - mechanizm regulacji wielkości szczeliny wylotowej i kół zamachowych
Ze względu na charakter ruchu szczęki roboczej kruszarki dzieli się na:
- kruszarki szczękowe o prostym ruchu szczęki z jedną lub dwoma płytami rozporowymi
- kruszarki i złożonym ruchu szczęki
W kruszarkach o prostym ruchu szczęka jest zawieszona na osi, natomiast dolny jej koniec wykonuje ruch wahadłowy, zbliżając się i odchylając od szczęki nieruchomej. Ruch szczęki realizowany jest od układu napędowego za pomocą wału mimośrodowego i płyty rozporowej. Stosuje się przede wszystkim do wstępnego rozdrabniania. Odznaczają się one dużymi siłami kruszenia i dlatego są stosowane do rozdrabniania materiałów twardych o dużej wytrzymałości na zgniatanie.
W kruszarkach o ruchu złożonym szczęka ruchoma jest zawieszona na wale mimośrodowym i podparta w dolnej części płytą rozporową. Szczęka w punkcie zawieszenia porusza się po kole o promieniu równym mimośrodowi, natomiast dolny punkt podparcia po łuku o promieniu o długości płyty rozporowej. Charakteryzują się mniejszą siłą kruszenia i są stosowane do wstępnego rozdrabniania materiałów oraz do rozdrabniania wtórnego i drobnego.
kruszarki stożkowe - stosowane przeważnie do drobnego kruszenia, produkt kruszenia bardziej regularny niż w przypadku kruszarek szczękowych. Nie stosuje się ich do rozdrabniania materiałów miękkich, lepkich i wilgotnych. Materiał rozdrabniany jest między stożkami: zewnętrznym stałym i wewnętrznym ruchomym wykonującym ruch mimośrodowy, stopień rozdrobnienia 5 – 8;
- kruszarki stożkowe z wałem podwieszonym: charakteryzują się sztywniejszą konstrukcją dzięki dwustronnemu łożyskowaniu wału głównego. Umożliwia to przenoszenie dużych obciążeń stożka wywołanych naciskiem kruszonego surowca.
- kruszarki stożkowe z wałem wspartym: z uwagi na jednostronne zamocowanie wału głównego posiadają znacznie słabszą konstrukcje, stosowane do rozdrabniania średniego
kruszarki walcowe - stosowane najczęściej do kruszenia średniego i drobnego, a także mielenia materiałów średniej i małej twardości. Materiał jest rozdrabniany przez zgniatanie między przeciwbieżnie obracającymi się walcami (najczęściej dwa, choć są rozwiązania z trzema). Powierzchnie walców mogą być gładkie lub zębate, stopień rozdrobnienia 4;
Składa się z dwóch walców stanowiących podstawowy zespół roboczy, napędu i ramy nośnej. Walce są płaszczami wykonanymi z utwardzonego żeliwa, hartowanej stali węglowej lub stali manganowej, zamocowane od piasty lub tarcz zaklinowanych na wale. Wały są ułożyskowane przeważnie na wahliwych łożyskach osadzonych w obudowach wmontowanych w ramę maszyny. Obudowy łożysk są osadzone w prowadnicach, co umożliwia regulację wielkości szczeliny wylotowej oraz przesunięcie walca w przypadku dostania się materiału niezkruszanego.
kruszarki uderzeniowe - stosowane są obecnie do wszystkich stadiów kruszenia oraz mielenia. Są obecnie wykorzystywane do kruszenia najtwardszych skał bazalt, dolomit, wapień, granit itp o niewielkiej ścierności (nie nadają się do piaskowców czy kwarcytów). Rozdrabnianie materiału następuje poprzez uderzenie wirującymi elementami roboczymi, jak również odbicia od nieruchomych płyt korpusu, stopień rozdrobnienia 8 do 32 i więcej;
- kruszarka wirnikowa młotkowa –odrzutowa
7. Maszyny do klasyfikacji ziarnowej materiałów sypkich budowa i obszary zastosowania:
Przesiewanie –zwane także klasyfikacją mechaniczna, jedna z podstaw operacji przeróbczych polegającą na rozdziale mieszaniny ziaren wg ich wielkości.
Przesiewacz załadowczy- kontrolne przesiewanie węgla i koksu przed załadunkiem
Przesiewniki stożkowe
Wygarniacz kołowy- przeznaczony do wygarniania materiałów sypkich oraz kawałków ze stołu zasobnika szczelinowego i przekazywania na współpracujący przenośnik taśmowy.
Podst. Podzespoły:
Rama, koło wygarniające z napędem i mechanizmem wychylenia, mechanizm jazdy, wyposażenie hydrauliczne, elektryczne, instalacje centralnego smarowania
Przesiewacz wałkowy – do wstępnego przesiewania drobnych klas ziarnowych 6-0,15-0, w zakładach przeróbki mechanicznej węgla kamiennego
Przesiewacze wibracyjne – do mech. Klasyfikacji przedwstępnej, końcowej ,odwadniania ,odmulania węgla, spłukiwania magnetyty, klasyfikacji ziarnowej.
Są wyposażone w napęd bezwładnościowy mocowany w ścianach
rzeszota, połączone bezpośrednio z silnikiem elektrycznym.
PRZESIEWACZE WIBRACYJNE KOŁOWE TYPU WK; PWK
Jedno- i dwupokładowe przesiewacze wibracyjne typu WK i PWK są przeznaczone
do klasyfikacji kruszywa i innych materiałów o średnim i drobnym
uziarnieniu. Sprężyście podparte rzeszoto przesiewaczy wykonuje swobodny ruch drgający
o trajektorii kołowej, wywołany napędem bezwładnościowym. Napęd stanowi wał o masach
niewyważonych, ułożyskowany w ścianach rzeszota, połączony przez sprzęgło elastyczne
z silnikiem elektrycznym. Przesiewacze mogą być wyposażone w pokłady sit: blaszanych,
składanych, harfowych, poliuretanowych, gumowych
Przesiewcze rusztowe – trójkątne , do odsiewania sortymentów grubych ziaren ponad ,80,120,200 mm i przy klasyfikacji. Wstępnej w zakładach przeróbki mech. Węgla kamiennego
Przesiewacze rusztowe – do oddzielania z transportowanego węgla lub innego materiału brył o granulacji ponad 200 mm.
Podst. Podzespoły
Motoreduktor, wał napędowy, wały napędzane, koła łańcuchowe , łańcuch tulejkowo- rolkowy, rama z burtami bocznymi
Przesiewniki wstrząsowe- ma zastosowanie przy surowcu zanieczyszczonym długimi skrawkami i obrzynami (”wąsami”) powstałymi podczas cięcia piłami taśmowymi. Przesiewacz posiada szczelny wysyp do przenośnika ślimakowego lub łańcuchowego.
Przesiewniki rezonansowe - Przesiewacze rezonansowe RT są stosowane
do końcowego przesiewania na 3-4 frakcje. Na wejściu górnej skrzyni jest umieszczony lej wsypowy z pełnym dnem, który chroni górną powierzchnię przesiewania przed zużyciem od spadającego materiału. Górna i dolna powierzchnia przesiewania jest łatwo dostępna do kontroli lub wymiany
Przesiewniki łukowe- stosuje sie do odwadniania, odmulania miałów i
mułów surowych w zakładach przeróbki mechanicznej surowców mineralnych. Moga być
stosowane do odmulania i dozowania miału weglowego przed osadzarkami oraz
odwadniania koncentratu po osadzarkach.
Podst. Podzespoły: wyposażono w napęd bezwładnościowy, który poprzez wirujące masy
niewyważone wywołuje siły odśrodkowe, które wzbudzaja ruch harmoniczny o trajektorii eliptycznej zawieszonego elastycznie rzeszota.
Przesiewniki stożkowe
9. Budowa i przykłady zastosowania wybranych urządzeń termicznych – piece obrotowe, piece szybowe.
Piece szybowe
Zastosowanie: W przemyśle cerami...