Twoim problemem jest to, że powszechną NICOŚĆ mylisz z osobistą PUSTKĄ
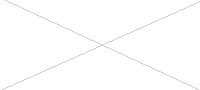
1.Co to jest maszynoznastwo. Maszyna ,urzadzenie
Maszynoznawstwo- jako dziedzina wiedzy technicznej zajmuje się teorią, konstrukcją, wykonawstwem maszyn i urządzeń oraz elementów, z których zostały zbudowane. Obejmuje zasady budowy i działania maszyn oraz niektórych związanych z nimi urządzeń technicznych. Maszyny i urządzenia zaliczamy do obiektów maszynoznawstwa.
Maszyna- to urządzenie do wykonywania pracy użytecznej, kosztem dostarczanej energii, lub przetwarzania jednego rodzaju energii na inną. Dzielimy na: silniki i maszyny robocze.
Urządzenie- to rodzaj mechanizmu lub zespół części służący do wykonania określonych czynności lub zadań.
2. Obserwacja zjawisk, podzial sygnałów
Obserwacja zjawisk- pole zjawiskowe jako zbiór sygnałów informujących o właściwościach obiektu wykorzystywane jest tylko w pewnych zakresach, gdyż pewne wiadomości o obiekcie są znane przed przystąpieniem do jego identyfikacji, a niektóre są zbędne. Zbiór informacji konieczny do identyfikacji obiektu będzie tym liczniejszy, im większa złożoność obiektu, im jest on bardziej nowoczesny, im mniej posiadamy o nim informacji wstępnych. Obserwacji obiektu można dokonać bezpośrednio lub pośrednio. Obserwacja bezpośrednia jest wtedy, gdy obiekt emituje sygnały, które mogą być bezpośrednio przyswojone przez obserwatora, przy czym informacje te mogą być zniekształcone innymi wielkościami pochodzącymi z samego źródła lub z innych obiektów, których pola zjawiskowe zachodzą na pole lub współdziałają z polem zjawiskowym badanego obiektu. Wielkości wpływowe powodują zakłócenia we właściwym odbiorze informacji i dlatego noszą też nazwę wielkości zakłócających. Zakłócenia mogą wpływać zarówno na obiekt, jak i na obserwatora. Obserwacje mogą być prowadzone przez jednego lub więcej obserwatorów, przy czym obserwatorzy mogą między sobą wymieniać informacje o badanym obiekcie. Może się jednak zdarzyć, że szybkość lub ilość informacji jest zbyt duża, by mogła być zarejestrowana przez obserwatora (obserwatorów). W tej sytuacji konieczna jest rejestracja sygnałów, a następnie przegląd przebiegu sygnałów w odpowiednio dobranym czasie.
Podział sygnałów- zdeterminowane i niezdeterminowane. Zdeterminowane mogą być opisane w sposób ścisły za pomocą zależności matematycznych. Są jednak sygnały, których nie można nawet w przybliżeniu opisać za pomocą ścisłych zależności matematycznych. Tego typu sygnały, nazywane niezdeterminowanymi, zwane również losowymi lub przypadkowymi są jedynie opisane za pomocą wielkości statystycznych. Sygnały te są sygnałami niepowtarzalnymi i dla każdego przypadku uzyskuje się inny przebieg ze zbioru nieskończonej liczby możliwych realizacji tego sygnału. Sygnały uzyskane w procesie losowym można podzielić na stacjonarne i niestacjonarne. Dla przypadków, w których wartości funkcji zmieniają się w czasie, proces losowy jest niestacjonarny. Natomiast wszędzie tam, gdzie wartości funkcji zmieniają się nieznacznie w czasie, mamy o czynienia z procesem losowym stacjonarnym.
3.Trwałość i niezawodność obiektów technicznych
Trwałość- to zdolność obiektu do zachowania w czasie eksploatacji wymaganych własności w określonych granicach, przy ustalonych warunkach użytkowania. Zdolność obiektu do zachowania jakości nosi nazwę niezawodności.
Niezawodność- prawdopodobieństwo, że w danych warunkach i w określonym czasie urządzenie będzie spełniało swoją funkcję bez wystąpienia uszkodzeń.
Muszą być spełnione następujące wymagania:
1) niezawodność określona musi być ilościowo za pomocą prawdopodobieństwa,
2) muszą być określone kryteria poprawnego funkcjonowania urządzenia,
3) muszą być ustalone warunki środowiskowe działania urządzenia ,
- należy określić może być
4) wymagany czas sprawnego działania urządzenia.
WZORY i wykres
4. Materiały konstrukcyjne.( Metalowe)
Na elementy maszyn (konstrukcje) stosujemy materiały metalowe: stal, żeliwo, staliwo, stopy metali nieżelaznych oraz materiały niemetalowe np. tworzywa sztuczne. Metale w licznych przypadkach wykazują w stanie stałym dobrą plastyczność, umożliwiając zmianę kształtu przedmiotu pod wpływem działania na niego sił zewnętrznych.
Stal- przerobiony plastycznie stop żelaza z węglem oraz innymi pierwiastkami, zawierającym do 2% węgla i otrzymywany w procesach stalowniczych w stanie ciekłym. Takie stopy przed obróbką plastyczną, a więc tylko odlane, nazywamy staliwami. Staliwo znajduje zastosowanie na odlewy niektórych części maszyn i urządzeń.
Podział stali:
-stale węglowe konstrukcyjne zwykłej jakości (oznacza się symbolem St i cyframi 0 lub 3-7),
-stale węglowe konstrukcyjne wyższej jakości,
-stale konstrukcyjne stopowe do nawęglania,
-stale konstrukcyjne do azotowania,
-stale konstrukcyjne stopowe do ulepszania cieplnego,
-stale sprężynowe (resorowe),
-stale na łożyska toczne.
Żeliwo- jest materiałem o bardzo dobrych właściwościach odlewniczych, odpornym na ściskanie i ścieranie, ale o stosunkowo niskiej wytrzymałości na rozciąganie i zginanie. Głównym składnikiem żeliwa jest węgiel oraz pewna ilość domieszek pochodzących z procesu hutniczego, takich jak: krzem, mangan, fosfor i siarka. Niekiedy do żeliwa wprowadza się dodatkowo składniki stopowe np. chrom, nikiel, miedź, w celu uzyskania specjalnych własności.
Spieki metaliczne wykonuje się metodami określanymi głównie jako metalurgia proszków. Przedmioty z proszków metali prasuje się pod wysokim ciśnieniem, a następnie spieka przez wyżarzenie w odpowiedniej temperaturze.
Z proszków spiekanych wytwarza się:
-koła zębate, panewki łożyskowe,
-porowate łożyska samosmarujące,
-materiały cierne- zawierające składniki zwiększające tarcie,
-nakładki na narzędzia skrawające oraz na części przyrządów pomiarowych wykonywane głównie z węglików wolframu i tytanu oraz kobaltu jako materiału wiążącego,
-elementy urządzeń elektronicznych.
Stopy metali niezależnych spośród których na elementy maszyn najczęściej stosuje się stopy miedzi, aluminium oraz cyny lub ołowiu.
5.Tworzywa sztuczne
Tworzywa sztuczne- wielkocząsteczkowe organiczne substancje, które mogą wykazywać właściwości plastyczne tylko przejściowo podczas ich wytwarzania lub przechodzić w stan plastyczny w przypadku ich podgrzewania. T.sztuczne są materiałami pochodzenia organicznego o złożonej budowie chemicznej, jak żywice syntetyczne lub żywice naturalne modyfikowane, celulozy oraz wiele innych związków chemicznych. Zależnie od własności chemicznych żywic wchodzących w skład tworzyw sztucznych rozróżniamy tworzywa termoplastyczne i termoutwardzalne oraz chemoutwardzalne (tworzywa termo- i chemoutwardzalne noszą wspólną nazwę duroplastów)
Tworzywa sztuczne termoplastyczne po podgrzaniu do określonej temperatury (150-2000C) przechodzą w stan plastyczny, ciastowaty lub ciekły, a przy chłodzeniu twardnieją; proces ten
wielokrotnie.
Tworzywa sztuczne termoutwardzalne po podgrzaniu do określonej temperatury (180-2500C) również przechodzą w stan plastyczny lub ciekły, ale tylko jeden raz; po utwardzeniu i ostygnięciu nie mogą być powtórnie przetwarzane (jest to proces nieodwracalny).
Żywice dzielimy na:
-naturalne (występują w przyrodzie- bursztyn, szelak) lub są otrzymywane w wyniku nieskomplikowanej przeróbki (asfalty, bitumity, kalafonia),
-sztuczne- otrzymuje się w wyniku polimeryzacji lub polikondensacji substancji prostych.
Cechy tworzyw sztucznych:
-mała gęstość,
-znaczna wytrzymałość mechaniczna, np. wytrzymałość na rozciąganie do 60 Mpa,
-dobre własności przeciwcierne,
-znaczna odporność na działanie czynników atmosferycznych,
-dobre własności elektroizolacyjne,
-dobre własności dielektryczne,
-dobra plastyczność,
-estetyczny wygląd.
Z tworzyw wykonuje się: koła zębate, panewki łożysk ślizgowych, wykładziny prowadnic ślizgowych, koszyczki łożysk tocznych, okładziny sprzęgieł i hamulców, śruby, nakrętki.
6. Metody oceny wytrzymałości konstrukcji, metody projektowania, podstawowe wzory
Metody oceny wytrzymałości konstrukcji - metody projektowania, podstawowe wzory.
Znane są dwie metody oceny wytrzymałości konstrukcji:
1. Metoda projektowania na dopuszczalne naprężenia; Najprostszą metodą oceny wytrzymałości konstrukcji i odkształcenia jest porównanie naprężeń w najbardziej obciążonych przekrojach elementu konstrukcyjnego z naprężeniami dopuszczalnymi. Musi być spełniona zależność:
σ = F/A ≤ σdop (k)
F – uogólnione obciążenie; A – uogólniony wskaźnik przekroju; σdop (k) – naprężenie dopuszczalne
σdop (k) = R/n
R – naprężenia niszczące; n – współczynnik bezpieczeństwa.
W metodzie tej, aby ocenić wytrzymałość, porównujemy zmienne w czasie naprężenia wynikające z obciążenia zewnętrznego, ze stałymi wartościami naprężeń dopuszczalnych. Z tego powodu przy tej metodzie oceny wartości naprężeń dopuszczalnych zależą one od sposobu i charakteru obciążenia.
2. Metoda projektowania na nośność graniczną; Nazywana również metodą projektowania na dopuszczalny udźwig. Metoda ta polega na określeniu obciążenia granicznego, przy którym następuje utrata możliwości przenoszenia odciążenia przez konstrukcję z powodu „dojścia” do granicznego stanu wytrzymałości. Metoda ta zezwala na pojawienie się w konstrukcji odkształceń plastycznych, czyli trwałych, a więc przekroczenie naprężeń dopuszczalnych w warstwach zewnętrznych elementów konstrukcyjnych, natomiast w warstwach zewnętrznych materiału naprężenia nie osiągają wartości granicznych. W tej metodzie, przyjmując jako obciążenie graniczne siłę powodującą płynięcie całego przekroju materiału, zakłada się „wyrównanie” naprężeń w stanie granicznym. Metoda na dopuszczalny udźwig nie nadaje się więc do stosowania w przypadkach zmęczenia materiału, gdyż tam nie następuje „wyrównanie” naprężeń, a o zniszczeniu decyduje największe naprężenie, zresztą znacznie niższe od naprężenia na granicy plastyczności. Ta metoda nie może być stosowana w zagadnieniach stateczności(wyboczenia).
Dobór odpowiedniej metody projektowania jest uzależniony między innymi od rodzaju obciążeń, charakteru obciążenia, stateczności konstrukcji, a także wymogów optymalizacyjno – ekonomicznych.
7. Wytrzymałośc zmęczeniowa, podstawowe wzory, wykres Wolera
Wytrzymałość zmęczeniowa, podstawowe wzory, wykres Wóhlera.
Zmęczeniem materiału nazywamy zjawisko pękania, czyli złomu ciała
powtarzany spowodowane działaniem zmiennego w czasie obciążenia (naprężenia).
Wytrzymałość zmęczeniowa jest to największe naprężenie σmax , dla danego cyklu naprężeń, przy którym element nie dozna zniszczenia po osiągnięciu umownej granicznej liczby cykli naprężeń NG.
Cykl naprężeń jest to zmiana ciągła naprężeń w czasie jednego okresu zmiany T.
Średnie naprężenie cyklu σm określa wzór:
σm = σmax+ σmin/2
Amplitudę cyklu naprężeń obliczamy z równania:
σa= σmax - σmin/2
Zakres zmian naprężeń przedstawia zależność:
2σa= σmax - σmin
Liczba asymetrii cyklu jest równa:
R= σmin / σmaxRównanie określające liczbę stałości obciążeń ma postać:
k= σm/ σa; gdzie k=1+R/1-R
Wykres ten przedstawia zależność pomiędzy wartością zmiennego naprężenia σ, a liczbą zmian N tego naprężenia, po których nastąpiło zniszczenie próbki.
8. Tarcie ( podział tarcia oraz zuzycie materiału
Tarcie (podział tarcia) oraz zużycie materiału.
Tarciem nazywamy zjawisko fizyczne, które przeciwdziała ruchowi względnemu elementów ciał skojarzonych w miejscu ich styku.
Klasyfikacja tarcia odbywa się na podstawie następujących kryteriów:
-ruchu,
-styku części trących,
-czynników pośredniczących w procesie tarcia.
Podział tarcia:
1. wewnętrzne: w ciałach stałych, w cieczach, w gazach
2. zewnętrzne: a).spoczynkowe: toczne
b).ruchowe: ślizgowe: suche, półsuche, mieszane, płynne
Zużyciem materiału nazywamy ubytek materiału z powierzchni ciał trących i postępujących zmian budowy warstwy wierzchniej w wyniku tarcia. Proces zużycia mierzony jest ubytkiem materiału lub zmianami własności warstwy wierzchniej.
9. Podział połączeń
Podział połączeń.
Połączenia części maszynowych dzielimy na:
- rozłączne
- nierozłączne
Połączenia nierozłączne dają się rozłączyć bez uszkodzenia przyłączy i łączników, a w połączeniach nierozłącznych, aby je rozłączyć, trzeba uszkodzić przyłącza lub łączniki.
Połączenia rozłączne dzielą się na:
- cierne
- kształtowe
- gwintowe
Połączenia nierozłączne dzielą się na:
- spajane
- kształtowane plastycznie
10. Połączenia cierne ( wciskowe)
Połączenia cierne (wciskowe).
Połączenia cierne możemy podzielić na:
- wtłaczane
- skurczowe
Połączenia wtłaczane: uzyskuje się przez wtłoczenie czopa w oprawę. W zależności od wymiaru przedmiotu i wartości wcisku nacisk poosiowy wywiera się za pomocą prasy hydraulicznej lub prasek ręcznych, a w przypadku małych przedmiotów – za pomocą młotka.
Połączenia skurczowe: powstają w wyniku zastosowania odpowiednich zabiegów cieplnych przed montażem połączenia: podgrzania oprawy lub oziębienia czopa wału. Zastosowanie jednego z tych zabiegów umożliwia swobodne wsunięcie czopa w oprawę, a po osiągnięciu temperatury otoczenia przez część ogrzaną (oziębioną) – uzyskanie odpowiedniego docisku części łączonych.
Połączenia cierne wtłaczane i skurczowe stosowane są powszechnie w budowie maszyn ze względu na ich prostotę i duże zalety.
Zalety połączeń ciernych (wciskowych):
- dokładna współosiowość (środkowanie) części łączonych;
- brak elementów dodatkowych (w połączeniach bezpośrednich);
- proste i tanie wykonanie;
- duża obciążalność połączeń (nawet przy obciążeniach zmiennych i udarowych;
Wady połączeń ciernych (wciskowych):
Znaczne naprężenia
- montażowe, grożące zniszczeniem części, zwłaszcza wykonanych z materiałów kruchych;
- Trudność uzyskania żądanego wcisku, zależnego (przy seryjnej produkcji) m.in. od uzyskanych wymiarów części – różnych w granicach tolerancji wykonania;
Konieczność stosowania dodatkowych zabezpieczeń przy przewidywanych przeciążeniach o nieustalonej wielkości