Twoim problemem jest to, że powszechną NICOŚĆ mylisz z osobistą PUSTKĄ
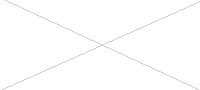
W zależności od zasięgu działania naprężenia własne można podzielić na:
·        naprężenia pierwszego rodzaju (makronaprężenia). Są to naprężenia międzystrefowe, tj. powstające między poszczególnymi strefami przekroju i między częściami wyrobu. Im większy jest gradient temperatur na przekroju, jak też gradient między poszczególnymi częściami wyrobu (zależny od prędkości i równomierności chłodzenia), tym większe wartości przybierają naprężenia pierwszego rodzaju;
·        naprężenia własne drugiego rodzaju. Powstają one wewnątrz ziarn lub między ziarnami sąsiadującymi ze sobą. Przyczyną powstawania tych naprężeń są różne współczynniki rozszerzalności liniowej faz występujących w obrabianych wyrobach lub też powstawanie nowych faz o różnej od wyjściowej objętości właściwej;
·        naprężenia własne trzeciego rodzaju. Naprężenia te powstają wewnątrz obszarów nie przekraczających kilku komórek elementarnych sieci krystalicznej metalu.
Głównymi przyczynami powstawania naprężeń własnych i wywołanych przez nie odkształceń są:
·        gradient temperatury na przekroju podczas grzania, a zwłaszcza chłodzenia, powodujący nierównomierne dylatacyjne zmiany objętości i wymiarów, czyli naprężenia cieplne,
·        przemiany fazowe i związane z nimi zmiany objętości właściwej, tzw. naprężenia strukturalne.
Najmniejszą objętość właściwą ma austenit, a największą martenzyt. Z tego względu procesowi przemiany austenitu w inne struktury towarzyszy wzrost objętości, największy przy przemianie austenitu w martenzyt, a najmniejszy przy przemianie w struktury perlityczne lub bainityczne. Zmiany objętościowe ze względu na swoją wartość, która może wynosić 0,5 ÷ l,5% oraz szybkość, z jaką zachodzą, powodują ogromne naprężenie, przewyższające naprężenia pochodzące od zjawisk rozszerzalności cieplnej i dlatego uważane są za główny powód odkształceń i pęknięć hartowniczych.
Na wartość naprężeń wewnętrznych, a zatem także na skłonność do pęknięć i odkształceń przy hartowaniu, wywierają wpływ następujące czynniki:
·        Skład chemiczny, tj. zawartość węgla i składników stopowych oraz struktura, jakość i hartowność stali. Wzrost zawartości węgla, a także dodatków stopowych sprzyja wzrostowi naprężeń. Niejednorodna struktura stali, obecność wtrąceń niemetalicznych są często powodem powstawania i rozprzestrzeniania się pęknięć.
·        Wielkość ziarna austenitu; im stal jest bardziej gruboziarnista, tym wyższe powstają w niej naprężenia.
·        Temperatura początku chłodzenia; im wyższa, tym większe powoduje naprężenie.
·        Rodzaj ośrodka chłodzącego; im szybciej dany ośrodek chłodzi w zakresie temperatur przemiany martenzytycznej, tym większe jest prawdopodobieństwo powstawania naprężeń i pęknięć; natomiast szybkość chłodzenia w zakresie austenitycznym nie odgrywa większej roli.
·        Niesymetryczne grzanie i chłodzenie sprzyja również powstawaniu naprężeń.
·        Kształt i wielkość przedmiotu; im większy przedmiot, a kształt jego bardziej złożony, tym większa skłonność do powstawania naprężeń.
Ograniczenie naprężeń wewnętrznych:
·        poszczególne elementy hartowanego przedmiotu powinny mieć możliwie równomierny przekrój (należy unikać skupień materiału i gwałtownych przejść pomiędzy poszczególnymi częściami przedmiotu),
·        należy unikać ostrych pocięć i naroży (działanie karbu),
·        przedmioty powinny mieć możliwie symetryczne rozmieszczenie mas,
·        należy unikać otworów nieprzelotowych w przedmiotach hartowanych.
Sposoby pomiaru naprężeń:
nieniszczące metody pomiaru: w tej grupie badań ważne miejsce zajmują metody rentgenograficzne wykorzystujące dyfrakcję promieniowania rentgenowskiego, gdzie stosowana jest różnorodna aparatura pomiarowa, np. dyfraktometry rentgenowskie lub specjalne goniometry. Powszechnie stosowana jest metoda sin2φ, która polega na określaniu zmian międzypłaszczyznowych w sieci krystalicznej materiału pod wpływem wewnętrznych sił występujących w elemencie konstrukcyjnym (próbce), a same naprężenia wylicza się ze specjalnych wzorów. Metoda sin2φ umożliwia pomiar i orientację głównych naprężeń, a także przy odpowiednim oprzyrządowaniu – pomiar mechanicznych stałych sprężystości.
Niszczące: metoda Waismana i Phillipsa. Polega ona na pomiarze zmian strzałki ugięcia próbki w funkcji grubości usuwanych warstw materiału. Usuwanie kolejnych warstw materiału odbywa się na drodze trawienia elektrolitycznego lub chemicznego. Wartości naprężeń własnych wylicza się zgodnie z wzorami podanymi przez Waismana i Phillipsa.
Do kontroli pęknięć hartowniczych najczęściej stosowana jest defektoskopia: magnetyczna, ultradźwiękowa i radiograficzna. Metoda magnetyczna służy do wykrywania wad powierzchniowych o grubości większej od 10-4 do l0-3 [mm], leżących na głębokości do 5 [mm]; metoda radiograficzna do wykrywania wad wewnętrznych niezbyt dużych przedmiotów, zaś metoda ultradźwiękowa do badania przedmiotów o większych przekrojach
Zapobieganie pęknięciom hartowniczym:
·         Wyeliminowanie lub zmniejszenie do możliwego minimum przerwy czasowej w ciągłości procesu
·         Dostosowanie składu atmosfery do gatunku stali
·         Dostosowanie konstrukcji osprzętu do kształtu części, stosowanie przekładek między częściami
·         Zmniejszenie szybkości grzania i zróżnicowanie temperatury w przestrzeni roboczej pieca
·         Zmiana konstrukcji lub zmniejszenie asymetrii; należy unikać dużego zróżnicowania przekrojów i jednostronnych wcięć
Â
Â