Twoim problemem jest to, że powszechną NICOŚĆ mylisz z osobistą PUSTKĄ
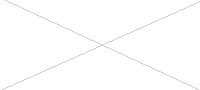
Kotły parowe
Opis urządzenia kotłowegoGłówne elementy urządzenia kotłowego. Podstawową częścią każdej siłowni parowej jest urządzenie kotłowe, zwykle nazywane wprost kotłem parowym. Właściwy kocioł jest to naczynie zamknięte, w którym pod działaniem ciepła woda, zmienia się w parę wodną o ciśnieniu wyższym od atmosferycznego, użytkowaną na zewnątrz kotła. Ciepło potrzebne do wytwarzania pary uzyskuje się wskutek spalarnia paliwa w palenisku. Gorące gazy spalinowe unoszą ciepło z paleniska i płyną wzdłuż, tzw. powierzchni ogrzewalnej kotła, której oddają ciepło, ogrzewając wodę w kotle i powodując jej parowanie.Wytwarzanie pary w kotle jest więc związane z trzema zjawiskami: ze spalaniem paliwa, wymianą energii w postaci ciepła oraz parowaniem wody. Kocioł powinien być stale zasilany wodą, paliwem i powietrzem. Produktem głównym kotła jest para wodna o określonym ciśnieniu, produktami ubocznymi, które należy usuwać, są spaliny, popiół i żużel.W skład nowoczesnego urządzenia kotłowego wchodzą następujące główne elementy:1. Parownik, zbudowany w postaci jednego lub kilku cylindrycznych naczyń stalowych, zwanych walczakami, albo z układu rur. W parowniku tworzy się para. mokra nasycona o znacznym stopniu suchości.2. Palenisko, którego zadaniem jest możliwie zupełne spalanie doprowadzonego paliwa z udziałem powietrza jednocześnie doprowadzanego do paleniska. Budowa paleniska zależy od rodzaju paliwa i od budowy kotła.Z paleniskiem związane są: urządzenie zasilające je paliwem; ruszt, na którym leży spalane paliwo stałe; palniki do spalania paliwa ciekłego, guzowego lub pyłowego; urządzenie doprowadzające powietrze potrzebne do spalania: komora paleniskowa; wewnątrz której następuje spalanie części lotnych oraz paliw ciekłych, gazowych i pyłowych; urządzenie do usuwania popiołu i żużla; urządzenie do obsługi i czyszczenia paleniska; obmurze tworzące obudowę paleniska kotła i kanałów spalinowych; izolacja cieplna.3. Przegrzewacze pary i podgrzewacze wody d powietrza, których rolę poznamy później.Oprócz wymienionych elementów urządzenia kotłowego wchodzą w jego skład również inne urządzenia pomocnicze potrzebne do pracy kotła, jak urządzenie do wytwarzania ciągu, do zasilania kotła wodą i paliwem, do usuwania popiołu i żużla, do oczyszczania wody zasilającej i spalin, osprzęt, armatura, aparatura kontrolno-pomiarowa : automatyka.Parametry techniczne. Podstawowymi wielkościami, które charakteryzują każdy urządzenie kotłowe, są: wydajność kotła, ciśnienie i temperatura pary, natężenie powierzchni ogrzewalnej i sprawność kotła.Wydajnością kotła nazywamy ilość pary wytworzonej w ciągu godziny. Wydajność kotła oznaczamy literą D, wyrażamy w kg/h lub t/h i mierzymy za pomocą paromierza. Zawiera się ona w szerokich granicach od kilkudziesięciu kg/h w bardzo małych kotłach, do ok. 3000 t/h w kotłach największych.Ciśnienie p pary zawiera się również w szerokich granicach: od 0,5 at nadciśnienia w małych kotłach centralnego ogrzewania, aż do350 at w wysokoprężnych kotłach specjalnych. Temperatura t pary sięga od niewiele ponad 100C aż do 550700C dla pary wysoko przegrzanej.Powierzchnią ogrzewalną kotła nazywamy powierzchnię ścian kotła z jednej strony ogrzewaną spalinami, a z drugiej strony omywaną wodą Powierzchnię tę mierzy się po stronie spalin; oznacza literą H i wyraża w m2. powierzchni ścian podgrzewaczy i przegrzewaczy nie zalicza się do powierzchni ogrzewalnej kotła. Powierzchnia ogrzewalna najmniejszych kotłów centralnego ogrzewania wynosi kilka metrów kwadratowych, a w największych kotłach energetycznych dochodzi do około 20 000 m2.Natężenie powierzchni ogrzewalnej (D/H) jest to stosunek wydajności: kotła do jego powierzchni ogrzewalnej i wyraża się liczbą kg pary wytworzonej w ciągu 1 h z 1 m2 powierzchni ogrzewalnej kotła.Natężenie powierzchni ogrzewalnej charakteryzuje jej wykorzystanie a zależy głównie od konstrukcji paleniska i kotła, jak również od rodzaju paliwa oraz od warunków pracy urządzenia kotłowego. Zawiera się ona w granicach od 8 kg/m2 h w małych kotłach o prymitywnej budowie do 150 kg/m2 h w dużych kotłach opromieniowanych, opalanych pyłem węglowym, a przekracza nawet 600 kg/m2  h w kotłach specjalnych. Przy obliczaniu natężenia powierzchni ogrzewalnej wydajność kotła należy przeliczyć na tzw. Parę normalną ,.tj. parę suchą nasyconą o ciśnieniu 1 at nadciśnienia i entalpii ok. 640 kcal/kg.W sposób przybliżony możną ocenić jakość procesu wytwarzania pary w kotle, obliczając tzw. wielokrotność odparowania D/B(odparowalność kotła). Jest to stosunek wydajności kotła (przeliczonej na parę normalną) do ilości B kg węgła spalonego w ciągu godziny (przeliczonego na paliwo umowne). Wielokrotność odparowania wyraża, ile kg pary otrzymuje się w kotle przez spalanie 1 kg węgla, i wynosi zwykle 59 kg/kg .Najściślejszą ocenę pracy kotła uzyskuje się przez wyznaczenie jego sprawności. Z energii dostarczonej do paleniska w postaci energii chemicznej paliwa tylko część przechodzi do wytworzonej pary, a reszta zostaje rozproszona w otoczeniu jako tzw. straty cieplne w kotle.Sprawnością  kotła nazywamy stosunek ilości ciepłą wyzyskanego użytecznie na wytworzenie w kotle pary - do całkowitej ilości energii dostarczonej do paleniska w postaci energii chemicznej paliwa gdzie: D - wydajność kotła w kg/h;i - entalpia pary pobieranej z kotła w kcal/kg; iw -entalpia wody zasilającej kocioł w kcal/kg; B -zużycie paliwa w ciągu godziny w kg/h;Qd - wartość opałowa. paliwa w kcal/kg.Sprawność kotłów parowych zawiera się w szerokich granicach zależnie od konstrukcji, staranności wykonania i obsługi kotła oraz od jego obciążenia i wynosi 0,500,70 w małych i prymitywnych urządzeniach kotłowych, 0,700,85 w urządzeniach większych z paleniskiem mechanicznym oraz 0,850,94 w urządzeniach dużych. Sprawność egzergetyczna kotłów parowych wynosi 0,400,60 d może być powiększona przez podwyższenie ciśnienia i temperatury produkowanej pary.Klasyfikacja kotłów parowych. Pod względem ciśnienia pary możemy podzielić .kotły na cztery rodzaje:1 - kotły niskoprężne - do 15 at nadciśnienia; 2 - kotły średnio prężne - do 40 at nadciśnienia; 3 - kotły wysokoprężne - do 150 at nadciśnienia;4 - kotły na najwyższe ciśnienia - ponad 150 at nadciśnienia. Ze względu na przeznaczenie rozróżniamy następujące trzy grupy kotłów parowych:1 - kotły ogrzewnicze - o wydajności do 2 t/h, wytwarzające parę nasyconą o ciśnieniu do 3 at nadc,2 - kotły przemysłowo-ogrzewnicze - o wydajności do 10 t/h wytwarzające parę nasyconą lub lekko przegrzaną o ciśnieniu nie przekraczającym 15 at, używaną w przemyśle do celów technologicznych i ogrzewniczych,3 - kotły energetyczne - tj. kotły średnio i wysokoprężne, o dużej wydajności (ponad 10 t/h), wytwarzające parę wysoko przegrzaną do napędu silników parowych, głównie w elektrowniach cieplnych możemy również podzielić kotły na: 1) stałe (nieruchome) i 2) ruchome - lokomobilowe, parowozowe, okrętowe, samochodowe. Ze względu na cechy konstrukcyjne rozróżniamy następujące rodzaje kotłów parowych: 1 - walczakowe, 2- płomienicowe; 3- kombinowane, 4- wodnorurkowe (opłomkotwe), 5- specjalne .       Symbole kotłów najczęściej używanych w kraju: SR - kocioł sekcyjny z paleniskiem rusztowym, OR- kocioł opromieniowany z paleniskiem rusztowym, OP - opromieniowany z paleniskiem pyłowym, OG - z paleniskiem gazowym; OO- z paleniskiem olejowym, OKR - opromieniowany z powierzchnią konwekcyjną, z paleniskiem rusztowym, OPC opromieniowany z paleniskiem pyłowym, z cyklonem, OPP - przepływowy ż paleniskiem pyłowym, PLM - kocioł parowy typu La Monta, W- kocioł wodny.Pierwsza liczba przy symbolu kotła oznacza jego wydajność w t/h, druga - nadciśnienie pary m at, trzecia - temperaturę pary przegrzanej i wC.       Budowa kotłów w Polsce. W związku z olbrzymim rozwojem przemysłu nastąpiło w naszych siłowniach przejście od niskich parametrów pary do wysokich rzędu 160 at ciśnienia i 540C temperatury .       Szerokie zastosowanie wysokich parametrów pary i nowoczesnych, wydajnych kotłów daje poważne oszczędności paliwa i umożliwia znaczne rozszerzenie produkcji energii elektrycznej. Przemysł kotlarski rozwinął produkcję nowoczesnych; wysokosprawnych kotłów parowych o zmechanizowanej regulacji pracy. Istotne znaczenie w rozwoju budowy kotłów w Polsce miały projekty nowoczesnych kotłów otrzymane z Rosji, jak również dostarczone urządzenia podstawowe i pomocnicze oraz pomoc fachowców ułatwiających montaż i rozruch urządzeń. Obecnie budujemy już niemal wszystkie nowoczesne typy kotłów parowych, a przemysł ten ciągle się rozwija. Przodującą rolę w budowie kotłów parowych w Polsce odgrywa dziś Fabryka Kotłów w Raciborzu. Tu produkuje się nowoczesne kotły stromorurkowę o ciśnieniu pary 110162 at. Tu powstały również .największe na świecie kotły na pył z węgla brunatnego dla elektrowni w Turoszowie.Bilans cieplny kotła Straty cielne. Praktycznie nieuniknione straty energii w postaci ciepła dostarczonej do paleniska kotła można podzielić na następujące grupy.1. Strata popielnikowa powstająca wskutek tego, że część paliwa nie spalona przesypuje się pomiędzy rusztowinami do popielnika. Strata ta jest dość znaczna przy miale nie sortowanym oraz na rusztach częściowo zużytych lub nie dostosowanych do drobnych sortymentów węgla. Wewnątrz żużla znajduje się często zapieczony koks, który nie zdążył się całkowicie spalić i również powoduje stratę ciepła. Rozżarzone popiół i żużel, przechodząc do popielnika, unoszą z sobą .nieznaczną ilość ciepła, która także stanowi część straty popielnikowej . Strata popielnikowi wynosi zwykle 18% wartości opałowej paliwa, a przy miale zwiększa się do 512%.       2. Strata wskutek niezupełnego spalania polegająca na tym, że w spalinach znajdują się jeszcze gazy palne (CO, CH4,H2).Stratę wskutek niezupełnego spalania można zmniejszyć, stosując dostateczny nadmiar powietrza, dużą komorę paleniskową, dobre wymieszanie paliwa z powietrzem, właściwą regulację dopływu powietrza do paleniska i doprowadzenie ponad warstwę paliwa powietrza dodatkowego (wtórnego). Strata niezupełnego spalania wynosi zwykle 0,53%.        3. Strata kominową - wiążąca się z dość wysoką temperaturą spalin, które uchodzą do komina i unoszą z sobą znaczną ilość nie wykorzystanego ciepła. Strata kominowa, największa spośród wszystkich strat ciepła w kotle, rośnie ze wzrostem ilości spalin i ich temperatury (w czopuchu). Ilość spalin, a więc i współczynnik nadmiaru powietrza, powinny być zatem możliwie małe, takie jednak, żeby nie wywołać zbyt dużej straty niezupełnego spalania. Należy również możliwie zmniejszyć zasysanie zbędnego powietrza z otoczenia przez nieszczelność obmurza. W kotłach o dużej wydajności, zaopatrzonych w podgrzewacze wody i powietrza, strata kominowa wynosi 612%, w kotłach bez podgrzewaczy dochodzi do 20%, a niekiedy nawet do 30% wartości opałowej paliwa.        4. Strata w koksiku i sadzy. Koksikiem nazywa się drobne cząstki węgla, które zostają porwane silnym ciągiem z paleniska w stronę komina, a przelatując przez obszar wysokiej temperatury wydzielają części lotne i ulegają skoksowaniu. Duża ilość koksiku występuje przy opalaniu kotłów miałem z węgla chudego oraz niedokładnie zmielonym i wysuszonym pyłem węglowym; przy silnym ciągu sztucznym. Brata w koksiku wynosi 0,56%, a niekiedy dochodzi do 10/a.Sadza powstaje jako produkt niezupełnego spalania węglowodorów, które wchodzą w skład części lotnych paliwa. Przyczyną powstawania sadzy jest niedostateczna ilość powietrza lub zbyt miska temperatura w palenisku. Strata wskutek powstawania sadzy wynosi zwykle 0,53%.       5. Strata wskutek przewodzenia i promieniowania polegająca na tym, że pomimo zastosowania w obmurzu kotła materiałów ciepłochronnych część ciepła z paleniska i gorących części kotła przedostaje się na zewnątrz. Wartość straty przewodzenia i promieniowania w małych kotłach wynosi 510%, w kotłach średnich 25%, a w dużych 0,52%.Bilans cieplny.         Wszystkie wymienione straty ciepła w kotle wyraża się zwykle w procentach i odnosi do wartości opałowej paliwa, tj. do cieple, które można uzyskać w palenisku przez zupełne spalenie 1 kg paliwa. Tę ilość ciepła traktuje się jako 100%. Odejmując od 100% ogólną sumę strat ciepła w kotle, otrzymamy sprawność kotła również wyrażoną w procentach. Szczegółowe zestawienie ilości ciepła otrzymanej w palenisku przez spalenie 1 kg paliwa, jego zużycia na wytwarzanie pary oraz strat z tym związanych nazywamy bilansem cieplnym kotła.Ogólne wiadomości o paleniskach         Klasyfikacja palenisk. Zadaniem paleniska jest możliwie zupełne i całkowite spalenie doprowadzonego paliwa z udziałem powietrza, jednocześnie doprowadzanego do paleniska. Konstrukcja paleniska zależy od czterech czynników: od rodzaju paliwa i sposobu jego spalania, oraz od wydajności kotła i jego konstrukcji.        Ze względu na rodzaj paliwa rozróżniamy paleniska: 1 - na paliwo stałe, 2 - na pył węglowy i drobno zmielony węgiel, 3 - na paliwo ciekłe, 4 - na paliwo gazowe.Zależnie od sposobu spalania dzielimy paleniska na:1 - warstwowe, czyli rusztowe o spalaniu warstwowym, służące do spalania .paliw stałych;2 - komorowe, czyli palnikowe o spalaniu przestrzennym, służące do spalania paliw ciekłych, gazowych, pyłu węglowego i drobno zmielonego węgla.W palenisku warstwowym warstwa paliwa spala się na ruszcie. Powietrze potrzebne do spalania płynie od dołu przez szczeliny w ruszcie i przez warstwę płonącego paliwa..          W palenisku komorowym spalające się cząstki paliwa poruszają się razem ze strumieniem powietrza i spalin, muszą więc być bardzo lekkie i drobne. Olbrzymia powierzchnia ogólna cząstek zapewnia bardzo szybki przebieg spalania.Zależnie od rodzaju obsługi rozróżniamy:1 - paleniska obsługiwane ręcznie, stosowane w kotłach o małej wydajności (do 6 t pary na godzinę);2 - paleniska półmechaniczne, stosowane w kotłach nieco większych w celu częściowego odciążenia palacza;3 - paleniska mechaniczne o całkowicie zmechanizowanej obsłudze, stosowane w kotłach o średniej powyżej 6 t/h) i dużej wydajności. Parametry techniczne. Palenisko kotłowe charakteryzują następujące wielkości podstawowe (parametry techniczne): powierzchnia rusztu i jego natężenie oraz sprawność paleniska.         Powierzchnia rusztu (mierzoną w m2 i oznaczaną literą R) nazywamy całkowitą powierzchnię górnej płaszczyzny rusztu, znajdującą się w palenisku, pokrytą warstwą paliwa i mającą szczeliny do przepływu powietrza.Natężeniem rusztu B/R nazywamy stosunek godzinowego zużycia paliwa B do powierzchni rusztu R. Wielkość ta wyraża, ile kg paliwa może być spalone w ciągu 1 h na 1 m2 powierzchni rusztu. Zależy ona od rodzaju paleniska i paliwa oraz od stopnia obciążenia rusztu: jest tym większa, im silniejszy jest ciąg, im mniejsza wartość opałowa paliwa, im grubsza jego warstwa na ruszcie oraz im większy stopień obciążenia rusztu.                                                     Natężenie rusztuPaliwo                          Rodzaj             paleniska             Natężenie rusztu R/B kg/(m2 h).             Węgiel kamienny             ruszt nieruchomy z obsługą ręczną             60125             Węgiel kamienny             ruszt taśmowy z podmuchem bezstrefowym             70150             Węgiel kamienny             ruszt taśmowy z podmuchem strefowym             130300             Węgiel kamienny             ruszt podsuwowy z podmuchem             130300Węgiel brunatny             ruszt schodkowy             170350Węgiel brunatny(brykiety)             ruszt taśmowy             100200             Torf                          palenisko szybowe             110250W tabl. podano natężenie rusztu dla różnych rodzajów paliwa i różnych palenisk w granicach od wartości najmniejszych do największych. Wartości najmniejsze dotyczą normalnego obciążenia rusztu, które odpowiada pracy kotła przy największej sprawności. Wartości największe można osiągnąć przy wzmożonej trwałej pracy. kotła, lecz przy zmniejszonej sprawności.Paleniska rusztowe Rozpatrzymy następujące paleniska rusztowe:I - obsługiwane ręcznie lub półmechanicznie paleniska rusztem nieruchomym: 1 - płaskim poziomym, 2 - paleniskiem pochyłym i 3 schodkowym. II - paleniska mechaniczne z rusztem ruchomym: 1 - taśmowym (posuwowym), 2- wstrząsanym.Palenisko z poziomym rusztem płaskim. Jest to najprostszy rodzaj paleniska obsługiwanego ręcznie, stosowanego w kotłach płomienicowych, kombinowanych i małych wodnorurkowych niemal na wszystkie, rodzaje paliwa stałego. Rys. 1 przedstawia palenisko z nieruchomym rusztem płaskim poziomym, wbudowane jako palenisko wewnętrzne kotła płomienicowego. Rys.1. Palenisko wewnętrzne z nieruchomym płaskim rusztem poziomym, obsługiwane ręcznie 1  rusztowiny, 2  1belka rusztowa, 3 - płyta ogniowa, 4 - przewał (próg ogniowy), 5- sklepienie ochronne, 6 - drażek regulacji powietrza wtórnego, 7 - rączka drzwiczek popielnika (regulacja ciągu), 8 - drzwiczki ogniowe, 9 - drzwiczki popielnika, 10 - osłona przeciw żarowa drzwiczekRuszt poziomy składa się z rusztowin 1 leżących swobodnie na belkach rusztowych 2. Ruszt znajduje się na wysokości 0,75 m mad podłogą stanowiska palacza i jest nie znaczenie pochylony ku tyłowi, co ułatwia obserwację i obsługę rusztu. Przed rusztem mieści się płyta ogniowa (przed rusztowa) 3, która oddziela ruszt od drzwiczek, oraz płyta czołowa zamykająca palenisko od przodu, w której znajdują się drzwiczki ogniowe 8 i drzwiczki popielnika 9. Na końcu rusztu znajduje .się żeliwny przewal (próg ogniowy) 4, który zapobiega przedostawaniu się paliwa poza ruszt i wywołuje ruch burzliwy i przemieszanie się gazów palnych z powietrzem. Między rusztowinami znajdują się szczeliny umożliwiające przepływ powietrza potrzebnego do spalania oraz przesypywanie się popiołu do popielnika. Powietrze dopływa od dołu przez drzwiczki popielnika: W celu lepszego spalania gazów palnych doprowadza się do paleniska przez próg ogniowy podgrzane powietrze wtórne. Najłatwiejsze do czyszczenia są rusztowiny proste. Przekrój rusztowin zwęża się ku dołowi, ażeby ułatwić przesypywanie żużla i popiołu do popielnika. Szerokość szczelin między rusztowinami jest tym mniejsza,. im mniejsze są kawałki paliwa i im mniejsza jest skłonność do tworzenia żużla. Przy spalaniu miału węglowego stosuje się rusztowiny ze szczelinami wężykowatymi i jodełkowymi albo ruszt płytkowy z otworami (dyszami) o średnicy 24 mm. Ruszt ten wymaga stosowania podmuchu.Przy układaniu rusztowin na belkach rusztowych zostawia się luz na ich wydłużanie i rozszerzanie się pod wpływem ciepła. Aby rusztowiny nie przepalały się zbyt szybko, powinny być chłodzone. Dokonuje tego powietrze, które przepływa przez szczeliny.Palenisko z płaskim rusztem poziomym jest okresowo zasilane paliwem ręcznie przez palacza, który powinien dbać o to, żeby warstwa paliwa na ruszcie miała możliwie jednakową grubość. Przez dziury" w warstwie paliwa przepływa za dużo powietrza, co studzi komorę paleniska i zwiększa stratę kominową, a przez miejsca zbyt grube przepływa za mało powietrza, co zwiększa stratę niezupełnego spalania, Należy narzucać paliwo w małych ilościach, jak najkrócej otwierając drzwiczki, aby zimne powietrze nie ostudziło kotła. Po zaobserwowaniu nierównomiernego spalania się paliwa na ruszcie należy poruszyć warstwę paliwa. Co 24 godz. oczyszcza się ruszt z żużla. Rys.2. Urządzenie do mechanicznego narzucania węgla1 - kosz węglowy, 2 - osłom podajnika, 3 węgiel, 4 - podajnik łopatkowy, 5 - ściana odchylna, 6 - osłona wyrzutnika, 7 - wirnik wyrzutnika, 8 - klapa odbojowa, 9 - drzwiczki paleniskowePowierzchnia płaskiego rusztu poziomego dochodzi w ruszcie zdwojonym do 5 m2, długość rusztu - do 2,5 m.Rysunek 2 przedstawia urządzenie do mechanicznego narzucania węg1a, przymocowane do płyty czołowej paleniska. Węgiel z kosza 1, który znajduje się przed kotłem i napełnia się mechanicznie większymi porcjami, przesypuje się do podajnika 4, którego łopatki przy ciągłym, bardzo wolnym obrocie podają niewielkie porcje węgla na wirnik wyrzutnika 7. Wirnik wykonuje 300=600 obr/min i swymi łopatkami wrzuca węgiel do paleniska. Zasięg rzutu reguluje położenie klapy odbojowej 8, od której odbija się węgiel. Aby zapewnić równomierne narzucanie na całej długości rusztu, klapa wykonuje ruch wahadłowy. Nowsza konstrukcja urządzenia mechanicznego ma zamiast wyrzutnika obrotowego klapę wahadłową, która wykonuje ok. 10 rzutów na minutę i znacznie oszczędniej gospodaruje węglem. Urządzenie mechaniczne usuwa potrzebę otwierania drzwiczek paleniska, zapewnia równomierne narzucanie węgla w małych dawkach i ułatwia pracę palacza.Palenisko z rusztem pochyłym. Ruszt pochyły (rys.3) jest pochylony pod kątem 4045, tak że paliwo z suwa się po nim z odpowiedniego kosza samoczynnie, co znacznie ułatwia obsługę paleniska. Palenisko z rusztem pochyłym służy do spalania odpadków drewna, torfu i nie spiekającego się węgla kamiennego. W miarę zsuwania się po ruszcie ku dołowi paliwo przechodzi kolejno wszystkie fazy spalania, a na płaskim ruszcie żużlowym, położonym poniżej rusztu pochyłego, zachodzi wypalanie się żużla. Długie sklepienie szamotowe w przedniej części paleniska powoduje suszenie i odgazowanie paliwa oraz zapłon części lotnych, Rys. 3. Palenisko z rusztem pochyłym 1 - płyta czołowa, 2 - kosz węglowy, 3 - gardziel, 4 - klapa regulacyjna do nastawiania grubości warstwy paliwa, 5 - belka rusztowa        Palenisko z posuwowym rusztem taśmowym. W kotłach o średniej i dużej wydajności stosuje się już od dawna ruszty ruchome o dużej wydajności cieplnej i o całkowicie zmechanizowanym zasilaniu i oczyszczaniu. Największe rozpowszechnienie pośród nich znalazł ruszt taśmowy(posuwowy, rys.4), który składa się z taśmy okrężnej, napiętej. pomiędzy dwoma wałami. Wał przedni jest .pędny. Napęd przenosi się z silnika elektrycznego przez .skrzynkę przekładniową zmniejszającą prędkość obrotową.Paliwo z kosza zsuwa się na górną część rusztu i unoszone dalej przez taśmę posuwa się razem z nią w głąb paleniska z prędkością 330, a nie kiedy nawet do 50 m/h. Prędkość ta może być regulowana zależnie od prędkości spalania. Reguluje się również grubość warstwy paliwa przez podnoszenie lub opuszczanie zasuwy 2 (tzw. warstwownicy). Powierzchnię rusztu tworzą osobne żeliwne rusztowiny osadzone na belkach rusztowych. W ten sposób ogniwa przegubowego łańcucha pędnego są oddalone od żaru,, a rusztowiny można łatwo wymieniać w czasie ruchu. Ponad rusztem w przedniej. części znajduje się krótkie sklepienie, które ma na celu za pomocą promieniowania cieplnego spowodowanie zapłonu paliwa na ruszcie. Na końcu tylnej. ścianki komory paleniskowej, zakończonej żeliwną belką chłodzoną wodą, jest zawieszony zgarniacz wahliwy, który oczyszcza ruszt .z żużla i spiętrza coraz cieńszą warstwę paliwa na ruszcie.Nowoczesne palenisko z rusztem taśmowym ma tzw. podmuch strefowy, tj. pod .górną częścią taśmy rusztu jest kilka komór ,otwartych od góry, a do każdej komory doprowadza się z wentylatora powietrze pod niewielkim nadciśnieniem, regulując jego dopływ oddzielnie do każdej komory. W ten sposób każda strefa rusztu otrzymuje ilość powietrza odpowiednią do miejscowego zapotrzebowania.Szerokość rusztów taśmowych dochodzi do 2,5 m, długość do 5 m. Ruszty z podmuchem strefowym buduje się szerokości do 9 m (ruszty podwójne do 12 m) i długości do 7,5 m. Palenisko z rusztem taśmowym umożliwia zatem uzyskanie powierzchni rusztu do 90 m2, co odpowiada ponad 150 t/h wydajności kotła, może więc być stosowane nawet w dużych instalacjach kotłowych.Palenisko z rusztem wstrząsanym. W dużych kotłach energetycznych. opalanych paliwem tanim, jak węgiel brunatny, przerosty, muł węglowy; stosuje się paleniska o ruszcie wstrząsanym mechanicznie. Jest to ruszt pochyły, którego rusztowiny wykonują mechanicznie krótkie ruchy przesuwne na przemian w przód i w tył. Gdy. jeden rząd rusztowin wykonuje ruch w przód, jednocześnie inny rząd rusztowin porusza się w tył. Rys. 4. Palenisko z rusztem taśmowym 1 - krążek łańcuchowy wału pędnego, 2 - zasuwa regulująca grubość warstwy paliwa, 3- belka chłodzona wodą, 4 - zgarniacz wahliwy; 5 - przeciwwaga zgarniacza, 6 - koła jezdne. 7 - krążki podpierające, 8 - popielnikPaleniska pyłowe i cyklopowePaleniska pyłowe. Odgazowanie, zapłon i spalanie pyłu węglowego, tj. zmielonego węgla, zachodzi w locie - w strumieniu powietrza wdmuchującego. pył do paleniska. Mieszanka pyłu i powietrza zostaje wprowadzona do paleniska za pomocą palników podobnie jak paliwo ciekłe i gazowe. Zależnie od rodzaju i sposobu rozmieszczenia palników rozróżniamy trzy rodzaje palenisk pyłowych:1 - .paleniska z palnikami szczelinowymi o płomieniu w kształcie litery U;2 - paleniska z palnikami wirowymi o płomieniu w kształcie litery L;3 - paleniska z palnikami szczelinowymi narożnymi.Rysunek 5 przedstawia palnik szczelinowy, a rys. 6a rozmieszczenie palników szczelinowych w palenisku. Palnik ma w dolnej części kształt spłaszczonej rury o otworze wylotowym w postaci szczeliny. Ustawia się go pionowo lub niemal pionowo, a mieszanina pyłu węglowego z powietrzem dopływa doń z góry ku dołowi. Liczba palników, ustawionych rzędem w palenisku, wynosi 310 zależnie od wielkości kotła.        Pył węglowy, zmieszany z tzw. Powietrzem nośnym (pierwotnym), płynie rurą 1 do palnika (rys. 4) i wpływa do kamery paleniskowej wy prostokątną szczeliną pyłową. Powietrze nośne stanowi ok. 15% zapotrzebowania powietrza do spalania i jest chłodne lub podgrzane do Ok. 150C. Pozostała część powietrza (powietrze dodatkowe) wpływa do. palnika pierścieniowym kanałem 2, otaczającym rurę palnika. W komorze paleniskowej następuje dokładne wymieszanie obu strumieni. Rys. 5. palnik szczelinowy 1- wlot mieszaniny pyłu węglowego i powietrza nośnego 2- wlot powietrza dodatkowego 3-wziernikZapłon mieszanki pyłowo- powietrznej następuje od żaru ścian paleniska w odległości kilkudziesięciu centymetrów od wylotu palnika. Długość płomienia, który zakreśla drogę w kształcie litery. U, dochodzi do 9 m. Powietrze wtórne podgrzane do 300400C jest wtłaczane przez okienka w przedniej ściance komory paleniskowej (rys.6a). Ściany komory chłodzi się za pomocą ekranów wodnych, a jej dno tworzy również rząd rur chłodzonych wodą (ruszt granulacyjny), który chłodzi i zestala w ziarenka żużel ściekający kroplami z płomienia. Palniki szczelinowe są używane w średnich i mniejszych kotłach do spalania palia o dużej zawartości części lotnych. Paliwo o małej zawartości .części lotnych lepiej się spala w paleniskach z nowoczesnymi .palnikami wirowymi. Rys.6. Umieszczenie palników pyłowych: a) umieszczenie stropowe palników szczelinowych, płomień w kształcie litery U, b) umieszczenie przyścienne palników wirowych, płomień w kształcie litery L, c) umieszczenie narożne palników szczelinowych, śrubowy kształt drogi powietrza1- palnik, 2 - powietrze wtórne, 3 - ruszt granulacyjnyPalnik wirowy (rys. 7) ma kształt rury stożkowej z wewnętrznymi żebrami śrubowymi, które powodują nadanie mieszaninie pyłu węglowego z powietrzem nośnym ruchu wirowego i należyte wymieszanie się jej z dopływającym z boku powietrzem dodatkowym, ogrzanym do temperatury 300400C. Umożliwia to użycie grubszego pyłu i skraca długość płomienia do 45 m, a zatem zmniejsza. objętość komory paleniskowej. Palniki są ,ustawione poziomo w przedniej ścianie komory, a promień zakreśla .drogę w kształcie litery L, (rys. 6b).Bardzo intensywny ruch wirowy mieszanki .pyłu i powietrza, sprzyjający całkowitemu spalaniu pyłu węglowego, zachodzi w palenisku ze szczelinowymi palnikami narożnymi rys. 6c. Ciąg w palenisku powoduje śrubowy ruch mieszanki ku górze, wskutek czego uzyskuje się dobre wymieszanie gazów i długą drogę spalin w palenisku:Dużą zaletą palenisk pyłowych jest wielka wydajność cieplna, która umożliwia ich stosowanie nawet w największych kotłach parowych. Paleniska pyłowe umożliwiają spalanie taniego miału węglowego i zapewniaj dużą sprawność kotła ze względu na mały nadmiar powietrza, zupełne i całkowite spalanie, wysoką temperaturę spalania oraz wykorzystanie promieniowania cieplnego. Poza tym paleniska te odznaczają Się łatwością zapalania, gaszenia i regulacji ognia. Wadą palenisk pyłowych jest duży koszt przygotowania pyłu, niebezpieczeństwo wybuchu przy jego przechowywaniu i transporcie oraz duża ilość popiołu unoszonego do komina, co wymaga dodatkowych odpylaczy spalin.W paleniskach pyłowych z palnikami poziomymi ,stosuje się dość często odprowadzanie żużla w stanie ciekłym. Palniki pochyla się nieco ku dołowi i umieszcza ,tak nisko, że ogrzewają żużel utrzymując go w stanie ciekłym Rys. 7. Palnik wirowy 1 - wlot, z - klapy regulacyjne powietrza dodatkowego, 3 - kółko ręczne napędu klap, 4 - komora powietrza dodatkowegow specjalnej wannie umieszczonej na spodzie paleniska. Ciekły żużel spływa bez przerwy przez przelew cienką strugą do zbiornika wody, gdzie granuluje się na drobne kawałki, skąd usuwany jest pompą razem z wodą.Przygotowanie pyłu węglowego. Na przygotowanie pyłu węglowego składają się następujące czynności kolejne:1 - rozdrabnianie większych brył węgla na kawałki o wymiarach 1020 mm w kruszarkach walcowych lub młotkowych (czynność ta odpada, gdy kotłownia jest zasilana miałem);2 - oddzielanie przedmiotów żelaznych za pomocą elektromagnesów; 3 - suszenie węgla w suszarkach bębnowych ogrzewanych pąrą odlotową lub spalinami. Suszenie jest potrzebne w celu ułatwienia przemiału, transportu i zapłonu węgla;4- mielenie węgla na pył w specjalnych młynach.        Gotowy pył węgłowy składa się z drobnych cząstek o rozmiarach 2050 m i zawiera ok. 20% wilgoci. Jest to sypka, pulchna mączka, ulatująca przy lada podmuchu i łatwo rozpływająca się" pod wpływem lekkich wstrząsów. W zasobniku z pyłem węglowym można utonąć i udusić się, dlatego wejście do niego jest zabezpieczone kratą. Pył węglowy zmieszany ze sprężonym powietrzem płynie jak woda, co umożliwia wygodny transport mieszanki do paleniska.Rysunek 8 przedstawia schemat urządzenia do przygotowania pyłu węglowego. Węgiel z zasobnika 1 spada na samoczynną wagę 2, a następnie do podajnika 3, który podaje go do młyna kulowego 4. Z komory 12 dopływa do młyna gorące powietrze, które częściowo osusza węgiel podczas mielenia. Otrzymany w młynie pył dostaje się wraz z powietrzem nośnym do. odsiewacza 5, gdzie następuje oddzielenie pyłu od większych cząstek węgla powracających do młyna. Mieszanka pyłowo-powietrzna jest następnie zasysana do urządzenia 6, zwanego cyklonem, które oddziela ok. 96% pyłu od powietrza. Pył gromadzi się w zasobniku 8 (pojemność 46 godzin pracy kotła), a stąd podajnikiem ślimakowym jest doprowadzamy do palników 10. Inny podajnik ślimakowy 14 może przenieść pył do zasobnika sąsiedniego kotła.Nieznacznie zapylone powietrze zostaje wyssane z cyklonu 6 za pomocą wentylatora 9 i również skierowane do palników 10. Gorące powietrze potrzebne do spalania jest pobierane z komory 12. Aby wentylator 9 mógł działać także w czasie postoju młyna, stosuje się osobne doprowadzenie powietrza 13. Pył węglowy ma dużą skłonność do samozapłonu i wybuchu. W celu zabezpieczenia urządzenia pyłowego przed zniszczeniem stosuje się zawór bezpieczeństwa 11. W przewodach instalacji są wbudowane zasuwy 7. Rys.8. Schemat urządzenia do przygotowania ,pyłu węglowego Rys. 9. Schemat paleniska cyklonowegoW odsiewaczu odśrodkowym strumień mieszanki pyłowo-powietrznej zostaje skierowany stycznie do ścianek komory odsiewacza. wskutek wirowego ruchu strumienia siła odśrodkowa powoduje uderzenie większych cząstek pyłu ścianki odsiewacza i z suwanie się ich w dół. W cyklonie następuje wytrącanie pyłu ze strumienia mieszanki pyłowo-powietrznej. Mieszanki zostaje w powadzona z dużą prędkością stycznie do ścianki cyklonu. cząstki pyłu kierują się ku ściance, uderzają w nią i zsuwają się po niej w dół, a powietrze wznosi się ku górze.Paleniska cyklonowe, ostatnim wyrazem postępu w budowie kotłów parowych jest spalanie węgla w paleniskach cyklonowych (rys.9) z odprowadzaniem żużla w stanie ciekłym. Palenisko cyklonowe ma kształt poziomego, ukośnego lub pionowego walca, do którego węgiel i powietrze wdmuchuje się z dużą prędkością stycznie do ścianek tak, że cząstki węgla są zawirowywane i odrzucane na ścianki pokryte lepkim, ciekłym żużlem, gdzie się całkowicie spalają.W palenisku cyklonowym można spalić dowolny gatunek węgla kamiennego, brunatnego i torfu oraz mieszanki węgla z mułem, pospółką koksową. przerostami i koksikiem lotnym. Węgiel miele się na ziarno wymiarach poniżej 6 mm. Podajniki podają zmielone paliwo do dysz, które za pomocą strumienia powietrza wtłaczają je do palników. Palniki na paliwo ciekłe i gazowePalniki na paliwo ciekłe. Paliwo ciekłe jest używane jako paliwo główne de opalania kotłów parowych w tych krajach, które mają własne źródła ropy naftowej, oraz do opalania kotłów okrętowych, a jako paliwo dodatkowe w paleniskach. w których spala się paliwo małowartościowe, jak również podczas rozruchu i pokrywania chwilowych zapotrzebowań szczytowych pary. Paliwo ciekłe spala się zwykle w stanie rozpylonym, a im dokładniejsze jest rozpylenie, tym lepsze są warunki parowania i zapłonu paliwa. Rozpylania paliwa ciekłego i wymieszania go z powietrzem dokonuje się za pomocą palników, przy czym rozpylanie może być parowe, powietrzne lub mechaniczne.Przy rozpylaniu parowym, stosowanym do paliw gęstych, przed doprowadzeniem do palnika podgrzewa się paliwo do temperatury 5070C, aby zmniejszyć jego lepkość. Para dopływa do palnika (rys. 10) pod ciśnieniem. 212 at i wydostaje się do paleniska z bardzo znaczną prędkością 15500 m/s przez dyszę s zakończoną otworem pierścieniowym, otaczającym. dyszę paliwową 4. Paliwo dopływa do palnika kanałem 1 i przedostaje się do otworu leżącego w osi palnika i zaopatrzonego w, kanalik spiralny, który wprawia ciecz w ruch wirowy. Strumień pary porywa z sobą paliwo, rozpyla je na drobniutkie kropelki i wdmuchuje do paleniska. Ilość dopływającego paliwa można regulować za pomocą iglicy umieszczonej w osi palnika. Rys. 10. Palnik na paliwo ciekłe z rozpylaniem parowym 1 - dopływ paliwa, 2 - dopływ pary, 3 - kanalik spiralny, 9 dysza paliwowa, 5, - dysza parowa, 6- chwyt, 7 - rączka regulacyjnaDo rozpylania powietrznego stosuje się zamiast pary nieznacznie sprężone, niekiedy podgrzanie powietrze. W kotłach okrętowych jest stosowane rozpylanie mechaniczne. Paliwo ogrzane do ok. 150C doprowadza się do palnika pod ciśnieniem wywieranym przez pompę paliwową (420 at). Paliwo, przepływając przez spiralny kanalik palnika, uzyskuje ruch wirowy i dzięki sile odśrodkowej ulega rozpyleniu przy wyjściu z dyszy palnika.Do zalet paliwa ciekłego w opalaniu kotłów parowych należą: bezdymne spalanie, brak iskier, popiołu i żużla, duża sprawność paleniska, łatwa obsługa i regulacja. Do wad niemal 3-krotnie wyższy koszt paliwa w porównaniu z węglem i niebezpieczeństwo wybuchu.Palniki gazowe. Paliwa gazowego używa się do opalania kotłów parowych tylko wówczas, gdy rozporządza się tanim paliwem, jak gaz ziemny, wielkopiecowy, koksowniczy, albo jeżeli wytwarza się paliwo gazowe do opalania palenisk przemysłowych.Palniki gazowe powinny zapewniać należyte przemieszanie gazu z powietrzem oraz dość znaczną prędkość wypływu gazu, aby uniemożliwić cofnięcie się płomienia w głąb palnika i wybuch gazu. Ciśnienia gazu zasilającego palniki wynosi 0,11,5 at nadciśnienia. Kotły walczakowe i płomienicoweKotły walczakowe. Najprostszym rodzajem kotła parowego jest kocioł walczakowy, dziś już nie budowany, jako urządzenie prymitywne a przestarzałe. Składa się on z walczaka o średnicy 9002200 mm, długości 5 do 18 m, częściowo wypełnionego wodą. Palenisko z rusztem płaskim znajduje się pod walczakiem i jest obsługiwane ręcznie. Spaliny przepływają pod walczakiem i po jego bokach.Ponieważ walczak jest częścią podstawową wielu innych rodzajów kotłów parowych, omówimy dokładniej jego budowę i pracę. Składa się on (rys. 11 i 12) z kilku pierścieniowych członów, zwiniętych z miękkiej blachy ze stali węglowej, oraz z dwóch lekko wypukłych dennic, wykonanych z tego samego materiału. Poszczególne części walczaka są ze sobą połączone za pomocą nitowania, zgrzewania lub spawania.W górnej części walczaka znajduje się kołpak parowy, którego zadaniem jest zmniejszenie wilgotności pary mokrej nasyconej, wytworzonej w walczaku. Na kołpaku jest osadzony zawór zamykający, łączący go z rurociągiem parowym, oraz zawór bezpieczeństwa. W dolnej części walczaka znajduje się zawór spustowy do opróżniania, płukania i odmulania kotła. Zasilanie kotła wodą odbywa się przez zawory zwrotny i zasilający. Woda wypełnia dolną część walczaka, zwaną przestrzenią wodną. Ponad nią znajduje się przestrzeń parowy, gdzie zbiera się para. Obie przestrzenie rozdziela zwierciadło wody, stanowiące powierzchnię parowania. Im większy jest stosunek powierzchni parowania do powierzchni ogrzewalnej kotła, tym spokojniejsze jest parowanie i większy stopień suchości pary.Poziom wody w kotle jest zmienny, zależny od ilości doprowadzanej wody i pobieranej pary. Do zasadniczych obowiązków palacza należy obserwacja za pomocą wodowskazu poziomu wody i utrzymywanie go w dopuszczalnych granicach. Najniższy poziom wody powinien się stale znajdować powyżej tzw. linii ogniowej, tj. górnej granicy powierzchni ogrzewalnej kotła. Zejście poniżej grozi wybuchem kotła. Poziom wody nie powinien być za wysoki ze względu na niebezpieczeństwo porywania wody przez parę do rurociągu parowego.Przestrzeń pomiędzy najniższym a najwyższym poziomem wody nazywana jest przestrzenią zasilania.Walczak jest zaopatrzony w owalny otwór zwany włazem, zamknięty od wewnątrz pokrywą, który umożliwia wejście do wnętrza walczaka w celu oczyszczenia go z kamienia kotłowego i mułu.Kocioł płomienicowy składa się z walczaka, wewnątrz którego wzdłuż osi przechodzą 1 lub 2 rury o dość dużej średnicy, zwane płomienicami. W płomienicy znajduje się palenisko wewnętrzne z rusztem płaskim poziomym albo palnik na paliwo ciekłe lub gazowe. Zależnie od liczby płomienic rozróżniamy kotły jedno płomienicowe (rys.11) i dwu płomienicowe (rys. 12a). Rys. 11kocioł jedno płomienicowy1- płomienica falista 2- palenisko 3- drugi przelot spalin 4- trzeci przelot spalin 5- stojaki oporowe 6- kołpak parowy 7- zawór spustowy 8- linia ogniowa Rys.12. Kotły z dwiema płomienicami: a) kocioł dwu płomienicowy zwykły, b) kocioł dwu płomienicowo płomieniówkowy 1 - człony walczaka, 2 - dennice, 3 - płomienice, 4 - stojak oporowe, 5 - obmurze, 6 czopuch, 7 - zasuwa kominowa, 8 - drzwiczki do czyszczenia kanałów spalinowych, 9 kołpak parowy, 10 - właz, 11 - zawór odcinający, 12 - zawór bezpieczeństwa, 13 - króciec zasilający, 14 - wodowskaz, 15 - zawór spustowy, 16 - przewód parowy; 17 - izolacja cieplna, I - pierwszy przelot spalin (przez płomienice), II - drugi przelot spalin, III - trzeci przelot spalinPłomienice wykonuje się przeważnie faliste, wskutek czego zwiększa się nieco powierzchnia ogrzewalna i sprężystość wzdłużna, co zapobiega odkształcaniu się dennic wywołanemu nierównomiernym ogrzewaniem. walczaka i płomienicy. W przedniej części płomienicy mieści się palenisko. Pierwszy przelot najgorętszych spalin odbywa się wzdłuż płomienicy, która stanowi najwydajniejszą część powierzchni ogrzewalnej kotła. Dzięki palenisku wewnętrznemu mączna część ciepła zostaje przekazana ściankom kotła przez promieniowanie. W kotle jedno płomienicowym płomienica jest nieco przesunięta w stosunku do osi walczaka i wskutek a symetrii ogrzewania wody w walczaku uzyskuje się żywsze jej krążenie.Do zalet kotłów płomienicowych zaliczamy: tania i prostą konstrukcję, łatwą obsługę ,i dużą pewność ruchu, dużą przestrzeń wodną, łatwe czyszczenie i remont, niewrażliwość na twardą wodę; dużą sprawność, zwłaszcza z podgrzewaczem wody oraz duże natężenie powierzchni ogrzewalnej. Wadami kotłów płomienicowych są: duży ciężar i duże zapotrzebowanie miejsca, powolne rozgrzewanie się, niskie ciśnienie pary i mała wydajność, małe rozmiary paleniska, które utrudniają zastosowanie paliwa niskogatunkowego, słabe krążenie wódy w kotłach dwu płomienicowych, niebezpieczeństwo uszkodzenia wskutek cienkiej warstwy wody nad płomienicami.Kotły płomienicowe znajdują częste zastosowanie w mniejszych zakładach przemysłowych, gdy jest zmienne zapotrzebowanie pary, zła jakość wody i wystarczająco duża powierzchnia kotłowni. Powierzchnia ogrzewalna kotłów 1-płomienicowych dochodzi do 70m2 2-płomienicowych - do 160 m2.Natężenie powierzchni ogrzewalnej wynosi 1830 kg/(m2  h), wydajność dochodzi do 4 t/h, największe ciśnienie pary - do 15 at nadciśnienia, sprawność kotła. - 5265%.Kotły kombinowaneZamiast płomienic o dużej średnicy, zawierających paleniska, można zastosować wiązkę rur gładkich o małej średnicy, tzw. płomieniówek, dzięki czemu uzyskuje się znacznie większą powierzchnię ogrzewalną niż w kotle płomienicowym o tych samych wymiarach walczaka. Płomieniówki przebiegają wzdłuż walczaka i są umocowane (rozwalcowane) w płaskich ścianach, zwanych ścianami sitowymi. Płomieniówki stanowią część składową używanych powszechnie kotłów kombinowanych, jak kotły płomienicowo płomieniówkowe, lokomobilowe, parowozowe, mniejsze okrętowe i stojące:Kocioł płomienicowo-płomieniówkowy (rys. 12b wykonanie całkowicie spawane) składa się z płaszcza, płomienicy i płomieniówek. Spaliny z płomienicy płyną do komory nawrotnej (I ciąg), następnie przez płomieniówki do przedniej części kotła (II ciąg), po nawrocie w komorze przedniej obmywają płomieniówki ód przodu do tyłu koda (III ciąg) i przez dymnicę uchodzą do komina.Kotły tego typu buduje się o powierzchni ogrzewalnej do 150 m2 i średnicy do 3 m; ciśnienie pary do 20 at, natężenie powierzchni ogrzewalnej 2030 kg/(m2 h), sprawność 60=75%. Zajmują mniej miejsca niż kotły płomienioowe, mają stosunkowo dużą przestrzeń wodną i nie wymagają kosztownego obmurza, gdyż wystarcza lekka izolacja. Ich wadą jest sztywność konstrukcji i skłonność do zanieczyszczania płomieniówek lotnym popiołem.Lokomobila składa się z kotła parowego i umieszczonego na nimi tłokowego silnika parowego, który czerpie parę do napędu bezpośrednio z kotła. Lokomobile .znajdują jeszcze niekiedy zastosowanie w rolnictwie, w młynach, tartakach, cegielniach, pompowniach i mniejszych zakładach przemysłowych, a także do napędu walców drogowych itp. Kocioł lokomobilowy, którego przekrój przedstawiono na rys. 3, nie ma obmurza, gdyżwszystkie jego kanały spalinowe są wewnętrzne. Jest on jedynie otulony materiałem izolacyjnym, ma więc ciężar i wymiary niewielkie, może być zatem umieszczony na podwoziu, jak w lokomobili przewoźnej. Są również lokomobile stałe ustawione na fundamencie, jak przedstawiona na rys.3. Kocioł ma jedną krótką płomienicę gładką lub falistą z umieszczonym wewnątrz płaskim rusztem poziomym. Przedłużeniem płomienicy jest wiązka płomieniówek o pochyleniu w dół, w kierunku paleniska. Spaliny przechodzą przez płomienicę i płomieniówki do dymnicy, znajdującej się na końcu kotła, a następnie uchodzą do komika. Rys. 3. Kocioł lakomobilowy stały z tłokowym silnikiem parowym1 - palenisko, 2 - płomieniówki, 3 - przegrzewacz pary, 4 - dymnica, 5 - kołpak parowy, 6 - komin, 7 - silnikW dymnicy umieszcza się zwoje rur przegrzewacza pary. Woda w walczaku ogrzewa się do temperatury wrzenia i zamienia w parę nasyconą, która zbiera się i osusza w kopałku parowym, następnie jest odprowadzana do przegrzewacza pary, gdzie osusza się ostatecznie i przegrzewa, a wreszcie zasila silnik parowy.Kotły wodnorurkowe (opłomkowej)Ogólna charakterystyka. Powierzchnia ogrzewalna kotłów wodnorurkowych okłada Się z rur o małej średnicy, którymi przepływa odparowywana woda, a które są ogrzewane. z zewnątrz spalinami. Noszą one nazwę rurek wodnych albo opłomek i stanowią nie jako odwrócenie płomieniówek, które są otoczone wodą i przez które przepływają spaliny. Zmiana ta wywołuje znaczne zwiększenie wytrzymałości kotła, gdyż opłomki wskutek małej średnicy wytrzymują duże ciśnienie wewnętrzne, nawet przy cienkich ściankach.W kotłach wodnorurkowych odparowanie wody zachodzi w opłomkach, a oddzielanie pary od wody w walczaku kotła. Z walczaka do opłomek, w których zachodzi odparowywanie, woda dopływa bądź specjalnymi rurami opadowymi, bądź słabo ogrzewanymi opłomkami. Takie rozwiązanie zapewnia bardzo szybki ruch wody przepływającej wewnątrz opłomek, co zwiększa wymianę energii w postaci ciepła w kotle, a więc i wydajność kotła. Rys.14. Kocioł sekcyjny z walczakiem wzdłużnym1 - walczak, 2 - palenisko, 3 - drzwiczki paleniska, 4 - czopuch, 5 skrzynki sekcyjne, 6 - opłomki, 7 - przegrzewacz pary, 8 - wodowskaz, 9 - manometr, 10 - obmurze, 11  na mulnik (zbiornik odmulający)     Układ opłomek umożliwia budowę wysokich komór paleniskowych, co zapewnia dobre spalanie i umożliwia zastosowanie wydajnych palenisk mechanicznych oraz wyzyskanie promieniowania cieplnego. Kotły wodnorurkowe umożliwiają wytwarzanie pary o wysokim ciśnieniu, zajmują stosunkowo małe miejsca przy wielkiej powierzchni ogrzewalnej, dużym natężeniu tej powierzchni i wysokiej sprawności ,odznaczają się krótkim czasem rozpalania i umożliwiają spalanie różnego rodzaju paliwa. Wadą kotłów wodnorurkowych jest duża wilgotność pary, co wymaga specjalnych urządzeń do jej osuszania. Do zasilania tych. kotłów jest potrzebna woda dokładnie oczyszczona i zmiękczona ze względu na trudność oczyszczania opłomek z kamienia kotłowego.Rozróżniamy dwa rodzaje kotłów wodnorurkowych: pochyło rurkowe o płomkach nieznacznie pochylonych względem poziomu (pod kątem 1015) i stromo rurkowe o dużym kącie nich pochylenia (6090). Pochylenie opłomek jest potrzebne do zwiększenia krążenia wody. Kotły pochyło rurkowe mają opłomki proste, a stromo rurkowe zakrzywione.Charakterystykę kotłów wodnorurkowych podano w tabeli.Charakterystyka kotłów wodnorurkowych (opłomkowych,)                   Wielkość             Oznaczenie wielkości i wymiar                          Kotły pochyło rurkowe sekcyjne             Kotły stromo rurkowe                          z walczakiem wzdłużnym             z walczakiem poprzecznym                          Po...