Twoim problemem jest to, że powszechną NICOŚĆ mylisz z osobistą PUSTKĄ
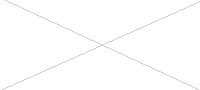
1. Cechą charakterystyczną każdego zbiegu jest: -niezmienność obrabianego elementu -niezmienność narzędzia lub zespołu narzędzi
-niezmienność warunków skrawania (nie dotyczy to zmiennej prędkości skrawania przy przecinaniu elementów na tokarce lub toczeniu czoła).
2. Jakie układy stanowisk występują przy produkcji: -jednostkowej: rodzajowe (tokarki ,frezarki ,wiertarki itp.) -seryjnej: gniazda obróbkowe
-masowej: linie obróbkowe.
3. Pod pojęciem technologiczności konstrukcji rozumiemy:
Takie zaprojektowanie przedmiotu ,aby przy zachowaniu wymaganej dokładności ,jakości i możliwościach zakładu koszt jego wykonania był jak najniższy.
4. Główne czynniki powstawania pęknięć w czasie hartowania to: -zmiany objętości struktury materiału niejednorodnego
-nagłe zmiany przekrojów przedmiotu
-nierównomierne nagrzewanie i stygnięcie elementu i towarzyszące im naprężenia cieplne.
5. Jaka jest największa masa odkuwek:
-swobodnych-do 180 ton
-foremnikowych kutych na
młotach-do 1000 kg
-foremnikowych kutych na
prasie-do 50 kg.
6. Jakim wymaganiom powinny odpowiadać surówki dostarczone do obróbki skrawaniem: -oczyszczenie odlewów z masy formierskiej
-oczyszczenie odkuwek ze zgorzeliny -jednorodność struktury materiału -bez naprężeń własnych
-twardość utrzymana w założonych granicach
7. W jaki sposób zapobiegamy tworzeniu się nalepów na powierzchni prowadnic narzędzi do wykonywania długich otworów?
Przez stosowanie tulejek drewnianych lub tulejek z tworzyw sztucznych
.8. Jakie sposoby stosowane są w celu zmniejszenia ujemnego wpływu ciepła na dokładność obróbki?
-bieg luzem obrabiarki przed
praca
-unikanie dłuższych przestojów
obrabiarki
-intensywne chłodzenie
,stosowanie płynów
obróbkowych oraz termostatów
lub oleju przy napędach
hydraulicznych
-klimatyzacja pomieszczeń
-zamocowanie półwyrobów w
sposób umożliwiający
kompensację powstających
odkształceń liniowych np.:
jednostronne mocowanie
przedmiotów długich w celu
umożliwienia im swobodnego
wydłużania się.
9.W jaki sposób określamy zdolność współpracy dwóch powierzchni? Jakim wymaganiom powinny odpowiadać powierzchnie łączone na stałe ,a jakim pow którym stawiamy specjalne wymagania np.: co do szczelności lub przenoszenia dużych obciążeń?
O zdolności współpracy dwóch powierzchni decyduje udział pow nośnej. W praktyce ocenia się go na podstawie liczby i średniej wielkości pkt przylegania. Powierzchnię wzorcowa pokryta tuszem przykłada się do pow badanej a następnie zlicza się ilość pkt styku i mierzy ich wielkość. Dla pow
łaczonych na stałe dopuszcza się mniejszą liczbę śladów ale o większej powierzchni (Fp=0.25 ,średnica śladów=6-8mm ,liczba śladów =3 - 5) Dla pow szczelnych lub przenoszących duże obciążenia (Fp= ,średnica śladów = 4 - 5mm ,liczba śladów = 26 - 40) .Fp=Fn/F ,gdzie Fp-udział nośny powierzchni ,Fn suma pól styku, F pow. Całkowita
10.Ująć w grupy ważniejsze cechy warstwy wierzchniej.
-Odnoszace się do struktury geometrycznej pow: chropowatość ,falistość ,odchyłki kształtu ,wady (rysy ,pęknięcia itp.)
-odnoszace się do materiału przedmiotu usytuowanego między pow rzeczywista a rdzeniem np.: grubość ,struktura ,naprężenia w warstwie wierzchniej ,wady (wtracenia pochodzenia obcego ,pęcherze itp.).
1l. Dlaczego dążymy do tego aby bazą była baza właściwa.
Ponieważ kiedy baza pokrywa się z baza konstrukcyjna to żądany wymiar otrzymujemy bez żadnych przeliczeń i można wykorzystać cały zakres tolerancji danego wymiaru.
12. Jakie warunki powinny być spełnione aby dociski mimośrodowe spełniały swoje zadanie. Podstawowym warunkiem jest samohamowność ,która jest konieczna ,żeby po usunięciu zewnętrznej siły mocującej docisk nie zluzował się pod wpływem sił skrawania. Uzyskuje się to przez odpowiedni dobór stosunku mimośrodowości "e" do promienia "r" e/r<mi.
13. Podać ogólne zasady dotyczące normowania pracy metodą analityczną uproszczony.
Istota tej metody polega na uproszczeniu sposobów obliczania czasu głównego oraz na ustalaniu dla typowych prac stosunku pozostałych składników czasu wkalkulowanego do czasu głównego. Uproszczenie wzorów do obliczenia Tg otrzymuje się w wyniku przyjęcia na podstawie danych statystycznych średnich parametrów skrawania stosowanych w produkcji oraz wyznaczenia współczynnika "k" umożliwiającego sprowadzenie wzoru na Tg do postaci prostego iloczynu.
14. Wyjaśnić różnicę między typizacją a metodą obróbki grupowej.
Typizacja jest to podobieństwo procesów technolog różnych części maszyn (odnosi się do całych partii elementów), natomiast metoda obróbki grupowej polega na łączeniu jednakowych operacji różnych części (odnosi się do pojedyńczych operacji).
15. Różnice między koncentracją mechaniczną ,a technologiczną.
Koncentracja technologiczna polega na jednoczesnej obróbce kilku pow kilkoma narzędziami. Powoduje skrócenie czasu głównego.
Koncentracja mechaniczna polega na stosowaniu specjalnych uchwytów i przyrządów wielopozycyjnych,
które ograniczaja liczbę zamocowań przedmiotu i narzędzi. Powoduje skrócenie czasu pomocniczego.
16. Metody uzyskiwania połączeń między : miedź z niklem ,molibdenem ;materiałów porowatych.
Miedź z niklem ,molibdenem-zgrzewanie dyfuzyjne w komorze próżniowej.
Materiały porowate-prasowanie z proszków i spiekanie (metale z metalami lub niemetalami).
18. Jak zapobiegać drganiom podczas obróbki?
Zwiększać sztywność obróbki zwłaszcza suportu i łożysk wrzeciona przez zmniejszenie do min wszelkich luzów.
Stosować kły o dużej sztywności Zmniejszać do min wysięg noża.
Stosować tłumiki drgań na nożach tokarskich. Mocować przedmioty silne i bez luzów.
Przy większych smukłościach przedmiotu I/d>10 stosować podtrzymki.
Ustawiać nóż i ustalać warunki skrawania tak aby następowało zmniejszenie drgań lub ich tłumienie.
19. Normowanie czasu metodą analityczną badawczą.
Pomiar czasów wykonywania poszczególnych czynności ,a następnie przez ich sumowanie określenie czasu operacji.
20. Kiedy stosujemy połączenia klinowe. Gdy chcemy uzyskać:
-Dokładne pozycjonowanie -łatwość i szybkość mocowania -zwielokrotnienie siły mocującej
-zmianę kierunku działania siły mocującej.
21. Cele typizacji przedmiotów:
-Skrócenie okresu technologicznego opracowania i użycie do tego celu pracowników o niższych kwalifikacjach
-ujednolicenie procesów obróbki i podniesienie na wyższy poziom procesów słabiej opracowanych -zastosowanie wydajniejszych środków produkcji w wyniku czego wzrost ich godzinowego obciażenia tak że opłacalne staje się zakupienie urzadzeń drogich.
22. Cel podziału operacji na elementy składowe:
-Zwiazanie zabiegów i przejście z parametrami skrawania w wyższe zakresy i obliczenie na tej podstawie czasu trwania operacji.
-odpowiednie rozplanowanie robót w czasie na poszczególnych stanowiskach
-opracowanie dokumentacji ,która w czasie trvvania operacji stanowi podstawę przestrzegania dyscypliny technologicznej.
23. Wymienić przyczyny stosowania do produkcji wałów prętów ciągnionych ,juszczonych ,szlifowanych zamiast tańszych walcowanych.
-Łatwość zasilania w materiał automatów prętowych
-Pow tych prętów (zwłaszcza szlifowanych) moga być pow nie podlegajacymi dalszej obróbce)
24. Ogólne wytyczne do wyboru obrabiarek narzędzi i uchwytów.
-Możliwość zapewnienia wymagań dotyczacych dokładności wymiarowej i jakości powierzchni. -jak najmniejszy koszt obróbki
-kryterium wydajnościowe ,mocy
-odpowiednia sztywność obrabiarki i jej uniwersalność.
25. Jakie są powody zmuszające nas do stosowania odpuszczania
po hartowaniu? -likwidacja austenitu szczątkowego
-relaksacja naprężeń hartowniczych -poprawienie ciągliwości.
26. Jaka jest największa masa odlewów? -Z form piaskowych do 100 ton
-kokilowych do 100 kg -ciśnieniowych do 5 kg -odśrodkowych do 1000 kg
27. W jaki sposób łagodzimy ujemny wpływ narostu podczas przeciągania ?
-Stosowanie prędkości przeciagania poza zakresem powstawania narostu -stosowanie odpowiednich cieczy smarująco chłodzących.
28. Do jakich zadań technolog wykorzystuje występujące w kompletach kół zmianowych gitary koła zębate o liczbie zębów:
-127 toczenie gwintów calowych
-71 i 113 lub 13 i 29 - toczenie gwintów modułowych.
29. Co rozumiemy pod pojęciem warstwy wierzchniej? Jakie jest znaczenie tej warstwy dla pracy części maszyn?
Jest to zewu warstwa materiału ograniczona pow rzeczywista przedmiotu obejmujaca ta powierzchnię oraz część materiału w głąb ,która wykazuje zmienione właściwości chemiczne i fizyczne w stosunku do cech mat rdzenia. Powinna się ona charakteryzować brakiem mikropęknięć ,przypaleń ,ak najmniejsza
chropowatoście powinny ,a naprężenia w niej występujące powinny być ściskające.
30. Wymienić rodzaje krzywek stosowanych w części roboczej docisków mimośrodowych oraz ich zalety i wady:
-Krzywki mimośrodowe: docisk nie jest proporcjonalny do siły ,ale najłatwiej je wykonać. -krzywki logarytmiczne: docisk jest proporcjonalny do siły ,trudne do wykonania
-krzywki archimedesa: docisk prawie proporcjonalny do siły ,stosunkowo łatwe do wykonania.
31. Elementy procesu technologicznego.
Zasadnicze: operacje ,zabiegi
Pomocnicze: towarzyszace czynnościom głównym (np.: zdejmowanie ,zakładanie przedmiotów na obrabiarce właczenie wyłaczenie posuwu itd.).
Pozycja ,przejście ,czynność ,ruch elementarny.
32. Naprężenia własne- zapobieganie ,usuwanie.
Konstrukcja części zapewniajacą równomierne stygnięcie.
Odpowiednie dobieranie procesu obróbki (prowadzić tak obróbkę aby czas pomiędzy obróbka zgrubna
i wykańczająca, był jak najdłuższy).
Usuwanie:
-sezonowanie naturalne
-sezonowanie sztuczne (odprężanie ,stabilizowanie)
-sezonowanie mechaniczne (bębnowanie ,śrutowanie ,młotkowanie)
33. Co to jest proces technologiczny?
Jest to część procesu prod ,która wiąże się ze zmiana kształtu ,wymiarów i cech fizykalnych wytwarzanych przedmiotów lub doborem i łączeniem tych elementów w zespoły a zespoły w gotowe maszyny.
34. Dane wyjściowe do projektowania procesu technolog. -Dane konstrukcyjne
-wielkość produkcji
-dane o materiałach i surówkach -dane o parku maszynowym.
35. Wał o cięiżarze 3 tony został po obróbce zmierzony i za pomocą suwnicy przeniesiony na szlifierkę. Które z wymienionych czynności a) pomiar , b)zdjęcie z tokarki , c)transport suwnic , d)zamocowanie na szlifierce należą do procesu technolog ,a które do produkcyjnego.
Proces prod: c) ,technolog a) ,b) ,d).
36.Z jakich procesów powinna składać się obróbka cieplna po nawęglaniu części wysoko_ odpowiedzialnych np.:ślimaków ze stali konstr węglowych wyższej jakości ?
-Dwukrotne hartowanie -niskie odpuszczanie.
37. Na jakie grupy można podzielić części otrzymane przez spiekanie proszków metali? -Elementy z materiałów trudno topliwych (np.: Mo ,Ti)
-pseudostopy -węgliki spiekane
-cermetale (stopy metali z ceramik 38. Wybrać metodę przecinania materiałów: -Stal szybkotnąca - termoelektrolitycznie -guma - wysokoenergetyczny strumień cieczy -azbest - strumień cieczy (pochłanianie pyłów) -węglik spiekany - termoelektrolitycznie
i podać krótkie uzasadnienie wybranej metody.
39. Jakie warunki i dlaczego powinny spełniać osełki w dogładzaniu oscylacyjnym? -długość osełki - ponad długość przedmiotu obrabianego (bez posuwu oscylacyjnego) ,ale nie powinny przekraczać 20 - 25mm
-powinny obejmować kat 40 - 60 stopni
-zmniejszenie siły nacisku przez zastosowanie kilku osełek jednocześnie
-zwiększenie gładkości pow przez utrzymywanie między osełka i przedmiotem warstwy płynu obróbkowego.
40. Czy można szlifować powierzchnie na tokarce karuzelowej? Jeżeli tak to kiedy i jak?
Można szlifować wtedy gdy przedmiot był toczony na tej tokarce ,a przeniesienie go na szlifierkę jest niemożliwe ze względu na jego duże wymiary lub utratę dokładności obróbki. Głowica szlifierska usytuowana jest w miejscu górnego suportu i ma osobny napęd. Posuw realizowany jest przez obrót stołu obrabiarki.
4l. Kiedy stosuje się skrobanie?
Skrobanie polega na ręcznym zeskrobywaniu materiału warstwami o grubości 0.01 mm w miejscach wypukłości pokrytych tuszem przy kontroli dokładności. Stosuje się je w przypadkach gdy:
-mamy doczynienia z bardzo wysokimi wymaganiami dotyczącymi nośności powierzchni -obrabiamy prowadnice bardzo dużych maszyn-i-nie mamy odpowiedniej sztifierki -obrabia się pow części nietechnologicznych ,których konstrukcja uniemożliwia zast obróbki mechanicznej.
42. Wyjaśnić na przykładzie obróbkę w stanie naprężonym i powody jej stosowania.
Obróbkę tą stosuje się w celu uniknięcia obróbki części po hartowaniu (o b dużej twardości) ,które mogą ulec wypaczeniu pod wpływem naprężeń hartowniczych. Często ten rodzaj obróbki stosuje się do prowadnic łóż obrabiarek.
Przebieg: a. wprowadzenie napięcia wstępnego
b. obróbka zgrubna w stanie naprężonym c. zdjęcie obciążenia
d. obróbka cieplna (zanik odkształcenia z powodu naprężeń wewnętrznych).
43. Określić wymiary międzyoperacyjne dla wykonania otworu fi50+0.030 w ściance korpusu. Otwór jest wstępnie odlany ,a kolejność obróbki wiórowej jest następująca: roztaczanie ,rozwiercanie wstępne i rozwiercanie wykańczające. Założenia: naddatek na rozwiercanie wstępne - 0.6 mm ,naddatek na rozwiercanie wykańczające - 0.4 mmm ,tolerancja roztaczania 0.15 ,tolerancja rozwiercania zgrubnego 0.1 mm.
-Po odlaniu fi = 46 mm
-po roztaczaniu fi = 49 + 0.15 mm
-po rozwiercaniu wstępnym fi = 49.6 + 0.1 mm
-po rozwiercaniu wykańczającym fi =50 + 0.03 mm
44. Wykazać strony dodatnie i ujemne strugania płaszczyzn w porównaniu z frezowaniem. Wady:
-obróbka mało wydajna przy stosowaniu jednego noża (wydajność zwiększamy przez zastosowanie obróbki wielonożowej)
-szybkie zużywanie się narzędzi. Zalety:
-stosunkowo duża dokładność przy zastosowaniu skrawania "szerokim nożem" -korzystne rozchodzenie się ciepła (na całej długości strugania)
-mniejsze koszty inwestycyjne związane z prostotą budowy -krótkie czasy przygotowawczo zakończeniowe
-mała wrażliwość na różnice grubości warstwy skrawanej
45. Jaki powinien być tok postępowania podczas obróbki na wiertarko-frezarce pięciu otworów o średnicy fi50 H7 każdy ,rozstawionych względem siebie w korpusie w odległości 100 0.01 mm ?
Cały rząd otworów obrabiamy jednym lub kilkoma narzędziami. Metody:
-metoda wg trasy odpada z powodu małej dokładności -można zastosować metodę płytek wzorcowych
-metoda współrzędnych prostokątnych - dokładność około 0.02 mm -metoda z zastosowaniem przyrządów optycznych ( najkorzystniejsza ). 46. Kiedy ekonomiczne jest stosowanie szlifowania zgrubnego płaszczyzn? -Przy obróbce bardzo twardych materiałów takich jak: żeliwo przy naddatku do 5mm -stal przy naddatku do 1 mmWadą tej metody jest duże zużycie tarcz ściernych i wysoka energochłonność. 47. Wymienić strony dodatnie i ujemne gniazda obróbkowego.
Zalety: -znaczne skrócenie czasu transportu międzyoperacyjnego
-możliwość zatrudnienia kadry pracowniczej o mniejszych kwalifikacjach wady:
-mała elastyczność
48. Czym należy kierować się przy doborze materiału na ślimak i ślimacznicę? Z jakich materiałów sporządzamy te elementy przy dużych średnicach i małych obciążeniach?
Należy się kierować małym wsp tarcia pomiędzy współpracującymi elementami.
Ślimaki wykonujemy ze stali ,ślimacznice z brązu ,ślimaki z żeliwa - ślimacznice z brązu tub oba elementy z żeliwa.
...