Twoim problemem jest to, że powszechną NICOŚĆ mylisz z osobistą PUSTKĄ
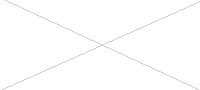
Metody statystyczne - procesy eksploatacyjne powtarzają się cyklicznie.
Metody techniczne - obliczaniu wskaźników zapasów na podstawie technicznych charakterystyk użytkowanych maszyn i założonej intensywności eksploatacji w planowanym okresie.
Metody techniczno-ekonomiczne - ustala się ekonomiczną wielkość partii dostaw, która powinna być taka, aby dla rzeczywistych wielkości zużycia, możliwości transportowych i magazynowych oraz określonych właściwości materiału, zapewnić minimalny koszt związany z zaopatrzeniem.
założenia metodzie planowania zapasów Wilsona
1) zużycie zakupywanego asortymentu jest stałe i niezmienne w czasie,
2) wielkość jednorazowej dostawy q jest stała w całym rozpatrywanym okresie,
3) koszt jednorazowej dostawy kz jest stały i niezależny od wielkości partii dostawy q dostarczanego towaru, Kz – koszt dostaw w okresie T,
4) koszt zakupu Q jednostek towaru jest niezależny od częstości dostaw i wynosi C,
5) koszt magazynowania km jednostki towaru jest stały, zaś całkowity koszt magazynowania Km jest proporcjonalny do ilości jednostek towaru w magazynie i do czasu magazynowania,
6) koszt zaopatrzenia, zwany też kosztem zapasu K jest sumą kosztu zakupu C, kosztu dostaw Kz (koszt dostawy + koszt zakupu Q jednostek towaru) i całkowitego kosztu magazynowania Km,
7) kolejne dostawy towaru następują w jednakowych odstępach czasu t,
8) średni zapas z w magazynie
metoda ABC planowania zapasów-uwzględnia się dwa kryteria podziału zapasów: udział danego asortymentu w ogólnej ilości i wartości zapasów, częstotliwość dokonywania zamówień. Całość zapasów dzieli się na trzy grupy A, B i C i dla każdej z tych grup prowadzi się odrębny cykl zamówień.
metoda JIT - dostarczanie materiałów i części w ściśle określonych ilościach, dokładnie w czasie kiedy firma ich potrzebuje. System taki można stosować dla dostaw wewnątrz zakładu jak i dla dostaw zewnętrznych. Główne założenia i zarazem zalety tej metody to: brak zapasów, krótkie cykle realizacji zamówienia, mała ilość dostarczanych materiałów i części, wysoka jakość produkcji.
korzystne efekty: redukcja zapasów materiałów i środków o 50 do 70%, wyrobów gotowych o ponad 30%, skrócenie cyklu produkcyjnego o około 40%, synchronizacja zaopatrzenia z produkcją w granicach 4 godzin do 2 dni, wzrost produktywności o 25%, poziomu obsługi klienta.
Przeglądy techniczne mają na celu określenie zakresu najbliższego remontu i ewentualne podjęcie decyzji o konieczności jego natychmiastowego przeprowadzenia. Przeglądy nie powinny eliminować maszyny z użytkowania dłużej niż na jedną zmianę, i o ile to możliwe, przeprowadza się je na trzeciej zmianie.
Remont bieżący polega na wymianie szybko zużywających się części. nie wymaga zwykle poważniejszego demontażu maszyny i przeprowadzany jest na miejscu jej pracy.
Remont średni też prowadzi się zwykle na miejscu pracy maszyny, choć ma on już znacznie szerszy zakres. Jego koszt może sięgać do 30% wartości remontowanego obiektu.
Naprawa główna, czyli remont kapitalny maszyn stacjonarnych wiąże się zwykle ze zdjęciem maszyny z fundamentów i całkowitym jej demontażem. W przypadku obrabiarek jego efektem jest nie tylko wymiana lub regeneracja zużytych części układu strukturalnego obrabiarki, ale również jej modernizacja, oraz wymiana lub naprawa współpracujących z nią układów pomocniczych. Po remoncie kapitalnym dokonuje się odbioru technicznego maszyny, która powinna odpowiadać normom ustalonym dla nowej maszyny. Koszt remontu kapitalnego nie powinien przekroczyć 70% wartości nowej, równoważnej pod względem wydajności i możliwości technologicznych maszyny.
Remonty planowo-zapobiegawcze. Główne zasady i sekwencja czynności konserwacyjno-remontowych dla cyklu remontowego obrabiarek.
Opiera się on na czterech głównych zasadach:
a) przestrzeganie norm prawidłowego użytkowania maszyn i wykonanie w czasie użytkowania niezbędnych czynności konserwacyjnych, b) wykonanie remontów po określonej z góry liczbie godzin pracy i w kolejności wynikającej z przyjętego cyklu remontowego, c) ustalenie i wykonanie rzeczowego zakresu planowanych remontów tak, aby przywracały one maszynie pierwotny resurs pracy, d) ustalenie statystycznych normatywów remontowych, tak pod względem zakresu robót, ich pracochłonności, jak i kosztu - jako wielkości wyjściowych przy ustalaniu planu remontów.
W systemie PZR podstawowe znaczenie planistyczne i organizacyjne ma cykl remontowy, który jest okresem między dwoma remontami kapitalnymi, lub od zainstalowania nowej maszyny do pierwszej jej naprawy głównej. Długość cyklu TCR oblicza się wychodząc z nominalnej trwałości (tn), przewidzianej dla danej maszyny. Długość cyklu remontowego TCR będzie zwykle odmienna od nominalnej trwałości tn
system remontów inspekcyjno-zapobiegawczych polega na zwiększeniu liczby planowych czynności kontrolno-pomiarowych, konserwacyjnych i regulacyjnych, zwanych inspekcjami zapobiegawczymi. Mogą one nawet być przeprowadzane w rytmie cotygodniowym.
Zalety: redukcja do minimum zaistnienia nieprzewidzianych awarii, remontów przedwczesnych, technicznie nieuzasadnionych.
Wady: duża pracochłonność i konieczność zapewnienia stosownych przestojów inspekcyjnych, zakłócających proces produkcyjny.
System remontów poprzeglądowych-głównie w zakładach przemysłowych o ruchu ciągłym. Zapewnia on ciągłość bezawaryjnego ruchu maszyn oraz odpowiednie przygotowanie organizacyjne i techniczne do wykonania remontu w jak najkrótszym czasie. polega na okresowej weryfikacjno- remontowej kontroli maszyn i wymianie w czasie remontu kompletnych zespołów lub podzespołów. Procedura postępowania: 1. Na podstawie informacji od operatora maszyny, lub pochodzącej z badań diagnostycznych, typuje się maszynę do przeglądu. 2. W czasie przeglądu określa się zakres i rodzaj niezbędnych działań profilaktyczno-remontowych, dokonując jedynie drobnych napraw. 3. Maszynę dalej się użytkuje, przygotowując w tym czasie niezbędne części zamienne i materiały do remontu oraz podejmuje odpowiednie przygotowania organizacyjne dla jego sprawnego przeprowadzenia, ustalając między innymi termin remontu. 4. Remont poprzeglądowy polega na szybkiej wymianie zakwestionowanych w czasie przeglądu kompletnych zespołów. Wymianę tą dokonuje się w miejscu pracy maszyny. Wymieniane mogą też być inne zespoły lub części, niż te które ustalono w trakcie przeglądu, o ile taka konieczność wyniknie w trakcie remontu. 5. Poza maszyną przeprowadza się weryfikację i remont wymienionych części, podzespołów i zespołów, co ma na celu przygotowanie ich jako zapasu do następnych remontów.
system remontów modułowych wymaga przeprowadzenia rozległych badań eksploatacyjnych, pod kątem niezawodności złożonych obiektów technicznych, które tym systemem remontowym mają być objęte. założenie, że o niezawodności decyduje na ogół niezbyt liczna grupa elementów. Podzespół lub zespół zawierający taki element nazwano modułem. opiera się na założeniu że:
- znany jest rozkład prawdopodobieństwa czasu poprawnej pracy istotnych niezawodnościowo elementów, wchodzących w skład danego modułu,
- koszty i straty związane z remontem prewencyjnym są mniejsze od kosztów i strat ponoszonych przy remoncie poawaryjnym,
- czas remontu, polegający na wymianie modułu jest krótszy niż czas samej naprawy, regeneracji, lub regulacji uszkodzonego modułu.
Stosowanie go będzie polegało na:
- wytypowaniu maszyn, które mają nim być objęte,
- zidentyfikowaniu w tych maszynach istotnych niezawodnościowo elementów i statystyczne wyznaczenie ich charakterystyk niezawodnościowych,
- sporządzenie harmonogramu remontów modułowych, przy założonym prawdopodobieństwie poprawności działania modułów,
- kontrolowaniu realizacji remontów i stanu zapasu części (zespołów) zamiennych.
Gdzie wykonuje się remonty kapitalne
- w zakładzie producenta maszyny. Dostarczoną do remontu maszynę rozbiera się na części, które poddawane są selekcji, regeneracji lub złomowaniu. Części odpowiadające normom technicznym oraz te po regeneracji, uzupełnione o nowe części, wcześniej złomowanych elementów, wchodzą na linię montażu i posłużą do budowy nowej maszyny. Pracochłonność i koszty remontu są stosunkowo niskie. Maszyna po wykonaniu remontu musi spełniać warunki jej odbioru technicznego (WOT), takie same jak maszyna nowa.
- w specjalistycznych bazach remontowych specjalistyczne bazy remontowe, zorganizowane pod kątem ściśle określonych typów maszyn. Potrzebne do remontu części zamienne powinny być dostarczone przez producenta remontowanych maszyn i tylko w ostateczności mogą być wytwarzane we własnym zakresie. Remonty połączone są z reguły z modernizacją. Zakłady remontowe bazują na WOT-ach producenta remontowanej maszyny, udzielając takiej samej gwarancji jaka obowiązuje dla nowej maszyny. Zapewniają też one serwis gwarancyjny i pogwarancyjny, a także prowadzą szkolenie personelu użytkownika.
- wykonywane przez wydziały remontowe zakładów przemysłowych. Wydziały takie są nastawione na remonty kapitalne wszystkich typów maszyn i urządzeń, pracujących w danym zakładzie. Remonty wykonuje się w technologii produkcji jednostkowej, a w mniejszych zakładach nawet systemem rzemieślniczym. Efektywność i koszty remontów kapitalnych przy takich uwarunkowaniach w danym zakładzie zależą w dużym stopniu od typizacji maszyn.
Ekonomiczna opłacalność remontu kapitalnego według granicznej wielkości maszyn niezamortyzowanych. 1. Kp £ Wn 2. Kp £ Km, Km £ Wn
maksymalna wartość nakładów na remont kapitalny może co najwyżej być równa nie zamortyzowanej części Wp. R = 1 - n/tn określa się mianem współczynnika ekonomicznej opłacalności remontu nie zamortyzowanych maszyn. Remont kapitalny będzie opłacalny gdy różnica DK=Km-Kp>0
dodatkowe kryteria należy uwzględnić przy obliczaniu opłacalności remontu kapitalnego
połączenie remontu kapitalnego z możliwością modernizacji obiektu, stopień moralnego zużycia maszyny, stopę inflacyjną, wartość likwidacyjną maszyny, wykorzystanie maszyny zgodnie z przeznaczeniem, organizacyjno-techniczny poziom gospodarki konserwacyjno-remontowej.
uproszczona metoda oceny opłacalności remontu kapitalnego polega na rejestracji rocznych kosztów utrzymania Ko obiektu i dodawaniu ich do kosztu nabycia maszyny Wp, co pozwala, w dowolnym czasie od rozpoczęcia użytkowania maszyny, na określenie przeciętnych rocznych kosztów utrzymania Kop. Jeżeli bieżące koszty utrzymania Ko(n) zrównają się z przeciętnym, rocznym kosztem utrzymania Kop(n), to dalsza eksploatacja maszyny staje się nieopłacalna.
Regeneracja przez zamianę par kojarzonych stosowana jest do elementów współpracujących ze sobą w dokładnie skojarzonych parach, o niewielkich rozmiarach, których czynne powierzchnie zużywają się równomiernie. Należą do nich elementy rozdzielaczy w pneumatycznych i hydraulicznych układach sterowania, tłoczki pomp wtryskowych, elementy toczne łożysk i par prowadnicowych itp. U podstaw tej metody leży kojarzenie parami współpracujących ze sobą elementów, dla zapewnienia określonej - zwykle bardzo małej - wartości luzu. Selekcję części dokonuje się w zbiorach elementów tworzących parę.
Regeneracja przez stosowanie wymiarów remontowych polega na odtworzeniu poprzez obróbkę mechaniczną prawidłowych kształtów, tego samego rodzaju pasowania oraz chropowatości powierzchni, przy jednoczesnej zmianie wymiaru nominalnego, ważnej funkcjonalnie pary roboczej. Wymiary remontowe nadaje się nowym częściom zamiennym oraz częściom zdemontowanym podczas remontu zespołu. Zużytą powierzchnię poddaje się obróbce skrawaniem, w wyniku której element otrzymuje nowy wymiar, nazywany wymiarem remontowym.
Regeneracja z zastosowaniem elementów dodatkowych
elementy dodatkowe kompensujące zużycie- tulejki, listwy, nakładki, a także nieregularne fragmenty części. Łączenie za pomocą wtłaczania, połączenia skurczowego, spawania, nitowania i połączenia gwintowego. Tulejowaniem można regenerować czopy, otwory i otwory gwintowane. Grubość tulejki określa się nie tyle z uwagi na wielkość zużycia ile z uwzględnieniem jej wytrzymałości na zgniot pod wpływem sił stosowanych do jej wtłoczenia w otwór lub osadzenia na czopie Dodatkowe elementy połączeniowe stosuje się również w przypadku usuwania skutków pęknięć, odłamań, gdy rodzaj materiału ogranicza stosowanie innych metod regeneracji. Jedną z najstarszych metod likwidacji skutków pęknięć w niespawalnych elementach metalowych jest szycie. Poza tym możliwe jest stosowanie pierścieniowych i kotwicowych elementów zaciskowych, których efektywność można podwyższyć stosowaniem różnego typu klejów
Regeneracja z zastosowaniem obróbki plastycznej Zastosować ją można wyłącznie do regeneracji części maszyn wykonanych z plastycznych metali. Polega ona na wywołaniu takiego stanu naprężenia w regenerowanym elemencie, który spowodowałby przekroczenie Re, a tym samym płynięcie materiału w kierunku zużytej powierzchni i przywrócenie jej pierwotnego kształtu, kosztem ubytku tego materiału w strefach mniej istotnych, gdzie ubytek nie przekreśla dalszego wypełnienia funkcji przez daną część. obróbka objętościowa: spęczanie, rozpieranie, roztłaczanie, wyciąganie i zwężanie. Do metod regeneracji poprzez obróbkę plastyczną zalicza się również prostowanie i gięcie. Można je wykonywać na zimno lub na gorąco, statycznie lub dynamicznie. Regenerację tego typu stosuje się najczęściej do przedmiotów cienkościennych Popularna metodą regeneracji polegającej na obróbce plastycznej jest nagniatanie. W procesie nagniatania uzyskuje się zmianę wymiaru, utwardzenie, a także zwiększenie gładkości powierzchni.
Regeneracja przez klejenie i kitowanie oraz nanoszenie warstw na zimno
Materiały kompozytowe wykorzystuje się jako materiały łączące elementy, do uzupełniania ubytków, powłoki w węzłach tarcia oraz powłoki narażone na erozyjno-korozyjne działanie czynników agresywnych. Typowe zastosowania materiałów kompozytowych to:
- naprawa pękniętych korpusów, bloków, pokryw, zbiorników,
- uszczelnienie przecieków w instalacjach wodnych, powietrznych, technologicznych,
- regeneracja zużytych czopów wałów i wybitych gniazd łożyskowych,
- uzupełnianie ubytków oraz uszczelnianie odlewów,
- odbudowa zużytych erozyjnie i korozyjnie elementów maszyn i instalacji (korpusy pomp, zawory, wirniki), regeneracja rowków wpustowych,
- uszczelnianie złączy zbiorników i spoin, osadzanie tulei (panwi),
- regeneracja zużytych połączeń gwintowych, usuwanie wżerów erozyjnych i korozyjnych
Regeneracja metodami klejenia lub nanoszenia warstw na zimno charakteryzują się niezwykłą prostotą z uwagi na to, że przeprowadzić je można w temperaturze otoczenia, w dowolnym warsztacie lub miejscu pracy maszyny. Kitowanie polega na uzupełnianiu lub wypełnianiu ubytków materiałowych za pomocą substancji, mającej właściwość trwałego łączenia się z materiałem regenerowanej części. Stosowane jest do poprawy szczelności skorodowanych połączeń kołnierzowych, wżerów na powierzchniach prowadnicowych lub kraterów będących efektem wad odlewniczych na częściach maszyn. Do metod regeneracji na zimno można zaliczyć także wszelkie metody galwanicznego uzupełniania ubytków, spowodowanych procesami zużycia ściernego. Są to metody kosztowne, wymagające uprzedniego przywrócenia regenerowanej części pożądanego kształtu geometrycznego, najczęściej na drodze obróbki mechanicznej.
Regeneracja przez spawanie i napawanie-niezwykle rozpowszechnione z uwagi na ich prostotę, wydajność, niskie koszty, dostępność energii elektrycznej i urządzeń. W spawaniu, a zwłaszcza napawaniu, stosuje się specjalne dodatki stopowe, pozwalające na uzyskiwanie napoin o wymaganych właściwościach. Szeroko rozpowszechnione jest napawanie regeneracyjne elektrodami proszkowymi zużywających się szybko części maszyn górniczych i drogowych. Aby zmniejszyć naprężenia termiczne, towarzyszące napawaniu stosuje się napawanie elektrowibracyjne lub napawanie elektroimpulsowe. Do metod regeneracji na gorąco zalicza się również napawanie plazmowe polegające na nakładaniu powłok regeneracyjnych przy użyciu generatora strumienia plazmy, napylającego stopiony proszek metalowy lub stopiony metal drutu wprowadzanego do łuku plazmy, na zużytą powierzchnię części maszynowej.
Metalizacja natryskowa polega na tym, że roztopiony materiał powłokowy w postaci drutu lub proszku pod działaniem strumienia sprężonego powietrza lub gazu obojętnego, zostaje rozpylony w pistolecie metalizacyjnym na drobne cząstki, które w stanie ciekłym lub plastycznym, padając na odpowiednio przygotowaną powierzchnię sczepiają się z nierównościami tej powierzchni podlegając gwałtownemu stygnięciu. Proces natryskiwania cieplnego prowadzi się z użyciem specjalnych pistoletów. Powłoki natryskiwane cieplnie mają szereg cennych zalet: są bardzo twarde i niejednorodne pod względem chemicznym (tlenki), są porowate, co podnosi walory tribologiczne tych powłok, są odporne na obciążenie zmęczeniowe i korozję.
Napawanie elktrowibracyjne Elektroda w postaci drutu zwiniętego na bębnie wysuwana jest za pomocą podajnika. Ślizg wykonuje ruch impulsowy dla uzyskania kontaktu z elektrodą i jest podłączony do dodatniego bieguna źródła prądu, napawany przedmiot zaś do ujemnego. W periodycznie powstającym i zanikającym łuku elektrycznym drut stapia się i płynny metal osadza się na napawanym przedmiocie w postaci cienkiej warstwy. Periodyczne zbliżanie i oddalanie elektrody jest wywołane za pomocą wibratora mechanicznego lub elektromagnetycznego. Proces napawania może zachodzić w powietrzu, w atmosferze gazu ochronnego, w emulsji wodnej lub pod topnikiem. Proces napawania zachodzi cyklicznie a pojedynczy cykl składa się ze zwarcia elektrody z napawanym przedmiotem, oderwania elektrody, wytworzenia krótkotrwałego łuku oraz przesunięcia elektrody w celu dokonania ponownego zwarcia.
Do zasadniczych zadań diagnostyki technicznej zaliczać się będzie:
- ustalenie, klasyfikowanie i badanie niesprawności obiektów oraz symptomów ich występowania,
-opracowanie metod i aparatury do mierzenia parametrów diagnostycznych,
-ocena stanu technicznego obiektów na podstawie zmierzonych parametrów diagnostycznych i porównanie ich z wyznaczonymi wcześniej wartościami granicznymi,
-ustalenie charakteru i zakresu czynności profilaktycznych, lub resursu poprawnej pracy.
Współzależność procesów mierzenia, diagnozowania i nadzorowania
Monitorowanie- okresowe pozyskiwanie i gromadzenie mniej lub bardziej przetworzonych wyników pomiarowych (tabele, wykresy) Jeżeli na podstawie wyników monitorowania przeprowadzi się stosowną ich analizę, polegającą zazwyczaj na porównaniu zmierzonych wielkości ze znanymi wzorcami i na tej podstawie dokona klasyfikacji stanu badanego obiektu, to mamy już do czynienia z procesem zwanym diagnozowaniem. Jeżeli w wyniku przeprowadzonej diagnozy, stosowne układy logiczne automatycznie podejmują właściwe decyzje, dotyczące zarówno maszyny jak i realizowanego przez nią procesu, to mamy do czynienia z procesem nadzorowania.
Aspekty diagnostyczne w procesie konstruowania maszyn
Projekty współczesnych maszyn powinny również uwzględniać potrzebę prowadzenia okresowych diagnozowań, np. w czasie przeglądów i napraw, środkami uniwersalnymi i specjalistycznymi. Bardzo przydatne dla użytkowników maszyn jest opracowanie na etapie konstruowania odpowiedniej dokumentacji dotyczącej sposobu diagnozowania obiektu w okresie jego eksploatacji. Dotyczy to również wzorców i określenia wartości dopuszczalnych i granicznych dla wybranych parametrów diagnostycznych. Przykładem efektów „diagnostycznego myślenia” w procesie projektowania może być współczesny serwis diagnostyczny w branży motoryzacyjnej. W specjalistycznych stacjach diagnostycznych sprzęga się, wbudowane w nowoczesnych silnikach samochodowych, środki diagnozowania z elektroniczną aparaturą, współpracującą z systemem komputerowego przetwarzania wyników z pomiarów diagnostycznych, co wyklucza wszelki subiektywizm w ocenie stanu badanego obiektu.
Diagnostyka kontrolna jakości wykonania Śledzenie rozkładu przypadkowości tych cech będzie domeną diagnostyki kontrolnej, stanowiącej ostatnie ogniwo całego - jak i cząstkowych procesów wytwarzania. Jej wynikiem będzie nie tylko zakwalifikowanie badanego obiektu do klasy zdatny lub niezdatny, ale także oddziaływanie na te elementy procesu wytwarzania, które spowodowały niepożądane odchylenia. Można tą drogą stosunkowo wcześnie eliminować z dalszego montażu wadliwe zespoły i tym samym nie tylko przyczynić się do podniesienia jakości maszyn, ale również do obniżki kosztów ich wytwarzania.
Diagnostyka procesów produkcyjnych Diagnostyka procesowa jest wprost nieodzowna wszędzie tam gdzie pracują urządzenia bez - lub tylko z częściowym nadzorem operatorskim. Przykładem takich maszyn są nowoczesne, elastyczne systemy produkcyjne, składające się z wielu mechanicznych urządzeń i maszyn, sprzężonych ze sobą systemami transportu i sterowania. Diagnostyka ta obejmuje, poza diagnozowaniem poprawności pracy samych obrabiarek i czuwaniem nad przebiegiem realizowanych na nich procesów skrawania, także funkcjonowanie urządzeń peryferyjnych i układów sterowania. Ma to na celu wykluczenie niepożądany...