Twoim problemem jest to, że powszechną NICOŚĆ mylisz z osobistą PUSTKĄ
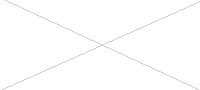
1 Odpylanie spalin:
Do urządzeń odpylających zalicza się:
- zespoły zasilające, urządzenia wentylacyjne pomieszczeń zespołów zasilających i ewentualnie urządzenia grzewcze, w przypadku elektrofiltrów, oraz łączniki i kable.
- ewentualne obiegi wtórne lub inne urządzenia służące do zapewnienia drożności roboczych elementów odpylaczy mechanicznych
- przyrządy pomiarowe do określenia stopnia zapylenia spalin oczyszczonych
Rodzaje odpylaczy:
Elektrofiltr: składa się z 2 zespołów: odpylacza elektrostatycznego i zespołu zasilającego. Działanie: zapylone spaliny przepływają z małą prędkością między elektrodami zbiorczymi (osadczymi). Z elektrod ulotowych (emitujących) po przyłączeniu wysokiego napięcia wydzielają się duże ilości elektronów, które są przyciągane przez elektrody osadcze i poruszają się w ich kierunku z dużą prędkością. W czasie tego ruchu elektrony uderzają w neutralne cząstki spalin, wytracając z nich dalsze elektrony, które z kolei powodują wytrącenie elektronów z innych cząstek spalin. Zjawisko to nz wyładowaniem koronowym zanika w pewnej odległości od elektrody ulotowej, dając w rezultacie duże ilości wolnych elektronów oraz dodatnio naładowane cząstki spalin, które są przyciągane ujemną elektrodę ulotową i osadzają się na niej. Elektrony powstałe w wyniku wyładowania koronkowego powodują naładowanie ujemne ziarenek pyłu które w skutek działania sił pola elektrycznego osadzają się na elektrodzie zbiorczej i wyniku „strzepywania” elektrod opadają do leja elektrofiltru.
Zalety: sprawność do 99,9%; odpylanie w sposób ciągły; minimalna ilość części ruchomych; najmniejsze opory przepływu
Wady: duży koszt wytwarzania; duża czułość na zmiany natężenia przepływu odpylanych spalin; duża czułość na zmiany temp i wilgoci spalin; duża czułość na zmiany charakterystyki pyłu.
Mechaniczne – oparte o zasadę bezwładności sił odśrodkowych
---Cyklony i multicyklony – wprowadzane do nich zapylone spaliny są wprawiane w ruch obrotowy. Powstająca siła odśrodkowa działa na cząstki zawartego w niech pyłu, odrzucając je na ścianki odpylacza, skąd siła ciężkości sprowadza je do leja pyłowego. Na 1 multicyklon składa się 20 cyklonów. Multicyklon składa się z: komory, cyklonów pojedynczych, rur wylotowych oczyszczanych spalin, wieńców łopatkowych wprowadzających spaliny w ruch obrotowy, płyty sitowa, leju pyłowego, wlotu zapylonych spalin, wylotu odpylonych spalin oraz uszczelnienia płyty sitowej. Sprawność ok. 0,4 – 0,7
---Żaluzjowe – do grubszych cząstek pyłu; sprawność ok. 0,7
---Filtry tkaninowe – sprawność ok. 99,5%; max temp spalin 250 stopni Celsjusza (najdrobniejsze cząstki)
---Filtry ceramiczne – max temp spalin 1100 stopni Celsjusza; sprawność ok. 99,9%
Zawartość pyłu lotnego dla kotłów rusztowych EKM – 20%; dla pyłowych – 80%
W kotłach EKM wykorzystywane są multicyklony a w kotłach WP - elektrofiltry
2 Odżużlanie:
Odżużlanie – proces technologiczny w którym niepalne produkty węgla (żużel, popiół drobny i popiół lotny) są odprowadzane z kotła.
Procentowy odpad w postaci żużla:
- kotły wodno WP120i WP 70 – parowe: 20% żużlu, 80% pyły
- kotły rusztowe EKM50 – 80% żużlu
Duży wpływ na skład popiołu mają: AL2O3; SiO2; CaO; MgO; Fe2O3; SO3.
Odżużlanie można prowadzić na 3 sposoby:
- mechanicznie – stosowane w małych kotłach (rusztowych) realizowane jest za pomocą wygarniarek łańcuchowych umieszczonych pod lejami żużlowymi; cechuje się małym zużyciem wody;
- hydrauliczne – najbardziej rozpowszechnione. Zaletą jest zwarta budowa, samoczynne działanie, duża czystość i daleki transport. Wady to duży koszt, duże zużycie wody oraz konieczność budowy osadników
- pneumatyczne ssące lub tłoczące ( trudność z zaopatrzeniem elektrociepłowni w wodę; trudno usuwalne związki); Zalety to prostota, utrzymanie podciśnienia. Wady to duże zużycie energii.
Przebieg procesu odżużlania: pod komorą paleniskową lub na końcu rusztu, żużel zgromadzony w lejach wpada do umieszczonej pod nim wanny. Aby zapobiec przenikaniu zbędnego powietrza do kotła poprzez otwór przez który żużel odprowadzany jest na zewnątrz, musi być on zanurzony w wodzie. Dodatkowo woda chłodzi żużel oraz powoduje zbrylenie. Następnie żużel jest odprowadzany do pojemnika zbiorczego specjalnym kanałami ułożonymi w ten sposób, że na całej długości zachowany jest spadek pozwalający na zapobieganie zapychania się. Z tego osadnika żużel jest wyławiany za pomocą dźwigu umieszczonego na suwnicy i składowany jest na palcu gdzie ulega dalszemu odsączeniu a następnie przenoszony jest do miejsca składowania.
3 Odsiarczanie spalin:
Przy spalaniu węgla uwalniane są znaczne ilości dwutlenku siarki, aby ograniczyć ilość emitowanych do atmosfery zanieczyszczeń stosuje się instalację odsiarczania spalin.
Metody: wapniowe; dwualkaiczne (magnezowe, sodowe, aluminiowe); inne(adsorpcyjne, amoniakalne, radiacyjne) .
Inny podział: suche; mokre; półsuche.
Jeszcze inny podział: proste odpadowe – dodawanie CaCO3, powstaje CaSO3 iCaSO4 w miale węglowym; pół odpadowe – w wyniku np. procesów absorpcji otrzymuje się produkt o użytecznych właściwościach; bezodpadowe – prowadzą do otrzymywania czystego SO2, S lub kwasu siarkowego.
Metoda amoniakalna:
Dwutlenek i trójtlenek siarki są wiązane prze wodny roztwór siarczynu amonu, wodorotlenku amonu i kwaśny siarczan amonu na nawóz sztuczny. Spaliny przed wylotem do absorbera muszą być odpylane i ochłodzone, po wylocie zaś podgrzane. Skuteczność odsiarczania w tym procesie sięga 90 -95%
Problemy związane z usuwaniem SO2:
- wysoka temp gazów po procesie odpylania;
-duża rozdzielczość SO2 w gazach spalinowych (2-4 g/m3 spalin);
- ogromne ilości spalin ok. 2 mln m3/h.
4 Nawęglanie:
Klasa węgla 20/20/12 (wartość opałowa / zawartość popiołu / zawartość siarki)
Analiza węgla: jest istotna dla utrzymania sprawności i poprawnej pracy kotła. EC posada własne laboratorium do badania węgla – pobiera się 3 próbki węgla dostarczanego do paleniska ze środka i skrajnych części podajnika. Próbki te pobiera się co 5 minut w 18 seriach i wyznacza się: wilgotność przemijająca i higroskopijna; ciepło spalania i wyliczenie wartości opałowej; zawartość części palnych; zawartość części lotnych; zawartość popiołu; zawartość siarki.
5 Analiza spalin:
Pełna analiza spalin obejmuje oznaczenie: składu chemicznego spalin; współczynnika nadmiaru powietrza; temp spalania; strat ciepła uchodzącego ze spalinami do otoczenia.
Podstawowymi gazami w spalinach są: tlen O2; tlenek węgla CO;
dwutlenek węgla CO2; tlenek azotu NOx; dwutlenek siarki S02.
Ilość spalin zależy od nadmiaru powietrza Lt. Masę spalin określa Ms = λLt + 1
W wyniku spalania paliwa powstaje para wodna i dwutlenek węgla:
Aparat Orsata: jest przyrządem stosowanym w analizie spalin do oznaczenia zawartości dwutlenku węgla, tlenku węgla i tlenu metodą selektywnej absorpcji. Składa się z biurety połączonej z naczyniem poziomowym, wypełnionej zwykle nasyconym roztworem chlorku sodu oraz 3 płuczek zawierających roztwory odpowiednich absorbentów: 50-procentowy roztwór wodorotlenku potasu KOH (pochłania CO2), zasadowy roztwór pirogalolu (pochłania O2) oraz amoniakalny roztwór chlorku miedzi II (pochłania CO). Próbkę gazu pobiera się do biurety, a następnie przez zmianę położenia naczynia poziomowego wprowadza się kolejno do płuczek. Mierząc w biurecie pierwotną objętość mieszaniny gazowej i objętość po pochłonięciu danego składnika oznacza się zawartość poszczególnych składników.
6 Przygotowanie wody dodatkowej:
EC posiada dwa ujęcia głębinowe. W EC uzdatnianie polega na zmiękczaniu, nie jest to pełna demineralizacja lecz tylko pozbycie się twardości przemijającej głównie węglanowej i magnezowej. Pierwszym etapem jest dekarbonizacja metodą strąceniową przez dodawanie do wody surowej wodorotlenku wapnia w postaci wodnego roztworu. Proces ten zachodzi w reaktorach stożkowych lub powolnych do których doprowadzamy w dolnej części wodę surową i roztwór wodorotlenku wapnia. Strugi tych płynów ulegają tu zawirowaniu i mieszają się. Zdekarbonizowana woda spływa u góry reaktora. Wodorotlenek wapnia reaguje z kwaśnymi węglanami wapnia i kwaśnymi węglanami magnezu. W wyniku reakcji powstaje węglan wapnia i węglan magnezu. Kwaśne węglany są dobrze rozpuszczalne w wodzie, węglany są słabo rozpuszczalne w wodzie, dlatego w wyniku tej reakcji ulegną wytrąceniu w postaci osadu. Podczas dekarbonizacji zastają wytrącone węglany wapnia i magnezu w postaci szlamu bądź w postaci zawiesiny. Szlam opadnie na dno reaktora i zostanie odprowadzony do odstojnika. Zawiesina przepływa wraz z wodą więc musi być ona odfiltrowana w filtrach żwirowych. Po przejściu przez filtry woda trafia do zbiorników wody filtrowanej skąd układ pomp podaje ja do dalszej obróbki na wymienniki jonowe. Jeżeli prze wymiennik przepływa woda zawierająca zdysocjonowane sole wapnia i magnez to ich jony będą przez złoże pobierane (kationy sodowe silnie kwaśne), a na ich miejsce będą podstawiane do roztworu jony sodu. Woda po takim procesie nazywa się zmiękczoną.
Twardość wody można podzielić na:
- twardość ogólną na która składa się twardość węglanowa spowodowana węglanami;
- twardość wapniowa i magnezowa;
- twardość przemijająca i nieprzemijająca.
7 Badanie generatora, praca nastawni i rozdzielni:
Parametry prądnicy synchronicznej: moc pozorna; napięcie stojana; prąd stojana; współczynnik mocy; prędkość obrotowa; napięcie wzbudzenia; prąd wzbudzenia; rodzaj, temp i ciśnienie czynnika chłodzącego (woda, wodór, układy płynowe).
Wał generatora osadzony jest na olejowych łożyskach ślizgowych; rozkład temp w rdzeniu stojana oraz uzwojeń jest w 5 różnych punktach.
Straty w generatorze:
- straty jałowe:
Straty w żelazie,straty prądów wirowych, straty przemagnesowania blach (histerezy)
- straty obciążeniowe:
Sprawność naszego generatora = 0,97-0,98 Praca nastawni:
Łączenie synchroniczne następuje gdy spełnione są warunki: napięcia są równe; częstotliwości są równe; kolejność faz jest taka sama i wskazy się pokrywają. Proces synchronizacji polega na tym, że turbozespół rozpędza się do prędkości bliskiej prędkości synchronicznej. Gdy mamy prędkości równe możemy załączyć wzbudzenie, prądnica pracuje wtedy jałowo, regulując wzbudzenie możemy ustawić napięcie równe napięciu sieci i poprzez stacyjkę oddziaływującą na zawory regulacyjne turbiny możemy precyzyjnie ustawić jej obroty (regulacja częstotliwości).
8 Badanie turbiny APT 12:
W turbinach odbywa się przemiana energii cieplnej zawartej w parze w energię mechaniczną. Podział turbin dokonujemy zwg na wiele czynników:
- zasadę działania – akcyjne i reakcyjne
- kierunek przepływu pary – osiowe i promieniowe
- stan czynnika termodynamicznego – na parę przegrzaną z ciśnieniem nad i pod krytycznym lub na parę nasyconą
- liczbę – korpusów, wylotów pary i wlotów
- specyfikę konstrukcji – komorowe, bębnowe lub ich kombinacje
- sposób realizacji obiegu cieplnego – kondensacyjne, przeciwprężne, upustowo kondensacyjne, upustowo przeciwprężne, kondensacyjno ciepłownicze, upustowo ciepłownicze.
Budowa: podstawowymi elementami biorącymi udział w przemianie są nieruchome tarcze wbudowane w stojan turbiny, wyposażone w dysze lub łopatki kierownicze oraz osadzone na wale turbiny koła z łopatkami wirnika. Odpowiednio profilowane dysze i łopatki tworzą kanały przepływu pary. Łopatki kierownicze i łopatki wirnika stanowią wieńce łopatkowe stojanowe i wirnikowe, które tworzą stopień turbiny.
10 Badanie kotła:
Kocioł jest urządzeniem służącym do zamiany energii paliwa stałego na energię cieplną, a następnie na energię wody i pary przegrzanej.
Budowa badanego kotła: jest kotłem walczakowym parowym, dwu ciągowym z paleniskiem warstwowym. Posiada 2 ruszty taśmowe osadzone na wałach z kołami zębatymi. Wał napędowy rusztu napędzany jest silnikiem asynchronicznym zasilanym z przetwornicy częstotliwości, co umożliwia zmianę prędkości przesuwu rusztu. Do napędu rusztów taśmowych stosuje się silniki prądu stałego pracujące w układzie Leonarda. Węgile jest dostarczany z zasobnika trzykotłowego za pomocą zsypu bezpośrednio na ruszt. Strumień masy paliwa dostarczanego do kotła reguluje się zmiana prędkości przesuwu rusztu oraz zmianą grubości warstwy paliwa. Zapalenie paliwa w ruszcie następuje w wyniku sklepienia zapłonowego, które jest umieszczone nad rusztem q dolnej części przedniej ściany kotła. Po spaleniu się węgla w palenisku pozostaje żużel i popiół który wpada do 1 z 3 lei żużlowych umieszczonych pod rusztem.
Sprawność kotła można wyznaczyć metodą bezpośrednią ηk=Qk/Qb = mD*(i1-iwz)/(mB*Wu); gdzie Qk – strumień energii przejmowanej przez czynniki termodynamiczne; Qb – strumień energii dostarczanej z paliwem; mD – strumień masy pary; mB – strumień masy paliwa; Wu – wartość opałowa paliwa; i1 –entalpia pary na wylocie kotła; iwz – entalpia wody zasilającej
lub pośrednią w której sprawność kotła wyznacza się na podstawie strat cieplnych kotła, które można dość dokładnie określić: ηk=100-ΣS; gdzie S – straty cieplne kotła.
W eksploatacji kotła występują straty ciepła wskutek
- niecałkowitego spalania: Sn=(100Wk)/ (mB*Wu)*ΣmAj*cAj (mAj – strumień mas poszczególnych składników; cAj – udział masowy części palnych w popiele i żużlu; Wk=34000kJ/kg dla koksu) dla kotłów rusztowych wartość tych strat wynosi 2-14%;
- niezupełnego spalania: SCO=k*CO/(CO2+CO) (CO2, CO – zawartość CO i CO2 w spalinach w procentach; k – wsp różny 60 dla węgla kamiennego i 70 dla brunatnego) wartość strat dla kotłów rusztowych wynosi do 5%
- straty wylotowe (kominowe) Sw=α*(ts-t0)/CO2 (α – wsp zależny od zawartości wilgoci w paliwie i CO2 w spalinach; ts – temp spalin; t0 – temp otoczenia). Są największe ze wszystkich strat i jej wartości decyduje o sprawności kotła
- straty promieniowania Spr wynikają z ciepła oddawanego do otoczenia przez promieniowanie i konwekcję obudowy kotła. Wyznacza się ją na podstawie wykresów empirycznych i pomiarów komorą termowizyjną.