Twoim problemem jest to, że powszechną NICOŚĆ mylisz z osobistą PUSTKĄ
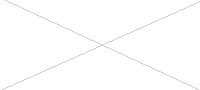
Â
Gazy
By uniknąć zagazowania w procesach topienia metali nieżelaznych, należy jak najdokładniej izolować przetapiany metal od czynników mogących spowodować jego zagazowanie:
-Â Â Â Â Â Â Â Â Â Â pary wodnej
-          węglowodorów i siarkowodorów
-          zanieczyszczeń niemetalicznych i metalicznych
oraz ograniczyć przestrzeń i czas stykania się ciekłego metalu z atmosferą zawierającą wymienione czynniki.
Omówienie pieców do topienia metalu, energia cieplna w procesie topienia.
Najczęściej stosuję się piece tyglowe w których można prowadzić rafinację żużlową i gazową. Podział pieców tyglowych:
-          na paliwo stałe o dmuchu naturalnym i wymuszonym
-          na paliwo ciekłe lub gazowe
-Â Â Â Â Â Â Â Â Â Â indukcyjne i oporowe
Piece płomienne stosowane do wytapiania metali nieżelaznych mogą być trzonowe lub obrotowe, w których metal bezpośrednio kontaktuje się z gazami spalinowymi. Poza tymi piecami można stosować piece elektryczne:
-          łukowe o działaniu łuku pośrednim
-Â Â Â Â Â Â Â Â Â Â oporowe o nagrzewaniu wsadu przez promieniowanie
-          indukcyjne kanałowe(rdzeniowe)
Metody rafinacji metali oraz ich skuteczność.
Rafinacja lancą, gazem obojętnym, można usunąć 40-50%,
Trzeba ruszać lancą w całej objętości.Do azotu będzie dyfundował wodór ponieważ muszą wyrównać się stężenia. Zimna bańka azotu powoduje miejscowe ochłodzenie metalu i obniżenie rozpuszczalności gazu w metalu
rafinacja próżnią
Kołpak może być podnoszony góra dół lub na bok.
Wodór przez dyfuzję będzie dostawał się do kołpaka (wychodził z ciekłego metalu). W tej metodzie czas rafinacji wynosi ok.15 min. Następuje szybkie schładzanie ciekłego metalu. W celu intensyfikacji procesu stosuje się mieszadło.
odgazowanie za pomocą drgań
Mini próżnie przemieszczają się w ciekłym metalu, dzięki czemu następuje odgazowanie.
Â
metoda rafinacji przez dno perforowane
metoda podwójnego topienia
Wytapiamy gąski, a następnie jeszcze raz topimy metal. Jak w alumetal-Kęty
rafinacja metalu gazem
TOPIENIE MIEDZI
1. Topienie stopów Cu-Zn
Zazwyczaj przy topieniu mosiądzów stosuje się piece tyglowe (galowe oraz ropne), płomienne (bębnowe oraz trzonowe) a także indukcyjne, pod warstwą pokrycia ochraniającego zazwyczaj utleniającą lub w rzadszych przypadkach przy użyciu węgla drzewnego. Proces topienia powinien odbywać się szybko z powodu utraty Zn, przegrzewa się go do momentu pojawienia się białego dymu. Nieznaczna domieszka (0,05%-Al) tworzy warstwę ochraniającą kąpiel przed działaniem utleniającym oraz odparowywaniem Zn.
Pozbycie się tlenu za pomocą fosforowanej miedzi nie jest konieczne z powodu obecności cynku, ma ona na celu jedynie upłynnienie stopu. Konieczna jest rafinacja przy użyciu gazów.
2. Topienie brązów
Do topienia brązów używa się stałych pieców płomieniowych, bębnowych oraz obrotowych: stałe tyglowe, elektryczne oraz indukcyjne.
Brązy zawierające Sn i P charakteryzują się dużymi temperaturami topnienia oraz odlewania, dzięki czemu posiadają tendencję do zagazowania oraz wydzielania tlenków.
Brązy zawierające P i Zn posiadają niższa temperaturę topnienia oraz znacznie lepszą lejność. Używane jako pokrycia mieszaniny piasków, szkła, boraksu bądź bezwodnej sody z piaskiem, a także utleniające powłoki mające ochronne właściwości dla mieszanin:
piasku, kuprytu, bosaku,
piasku, boraksu, tlenku Mn,
Topienie należy przeprowadzać w sposób szybki przy użyciu atmosfery lekko utleniającej.
Poprzez dodatek 0,05% fosforu w postaci fosforowej miedzi (CuP )prowadzi się proces odtleniania (odtlenianiu nie poddaje się brązów fosforowych)
Przy ewentualnej rafinacji stosuje się zamiast pokrycia (przeważnie N lub Cl)- rafinator.
Do zasadniczych czynników mających wpływ na właściwości odlewu oraz jego jakość należy temperatura przegrzania oraz odlewania. Podczas procesu topienia przeważającej części metali znaczne przegrzanie stopu wpływa negatywnie na własności.
Podczas wzrostu temperatury przegrzania rośnie także rozpuszczalność gazów, oddziaływanie z wykładziną pieca oraz utlenianie topionego metalu.
Zbyt wysoka temperatura odlewania powoduje wzrost skurczu odlewniczego.
Proces odlewania brązów cynowych jest ograniczony w kokilach z uwagi na pękanie skurczowe (stosowane przy nieskomplikowanych kształtach jak tuleje lub wałki) Wskazane jest aby temperatura kokili zawierała się w zakresie 300-350°C podczas podgrzewania.
BrÄ…zy cynowe:
Stosuje się wsad 50% wsadu odlewniczego i 50% wsadu czystego. Stosować należy żużle pokrywające, podstawowe składniki:
-Â Â Â Â Â Â Â Â Â Â kupryt
-Â Â Â Â Â Â Â Â Â Â borax
-Â Â Â Â Â Â Â Â Â Â piasek gruboziarnisty
Â
Ilość stosowanego żużla ok. 2%. Proces topienia przeprowadzać szybko i nie należy przegrzewać powyżej 11500C ponieważ powoduje to obniżenie właściwości. Temperatura zalewania 1080 do 1150 0C
Przy odlewaniu do kokili, trzeba ją podgrzać do temperatury ok200 0C.
BrÄ…zy krzemowe:
Skurcz wynosi 1,5 do 1,6 %. Do wytopu stosowane piece indukcyjne lub opalane paliwem gazowym. Wsad 50% złomu, 50% czysty wsad.
Żużle ok. 2% połowa przed stopieniem i druga połowa po stopieniu.
Do rafinacji można użyć gazu(preparat Longgaz). Temperatura zalewania od 1050 do 1100 0C.
BrÄ…zy aluminiowe:
Skurcz: 2,5%. Wytapianie w piecach indukcyjnych. Żużle, ilość ok.2-3%: fluoryt, sól kuchenna, (połowa w czasie roztapiania, druga po roztopieniu.) temp. Tygla ok. 500-600 0C zalecany jak najkrótszy czas topienia. Temp. Zalewania i rafinacji 1200 0C, czas rafinacji 8-10min.
13. Zarys metalurgii aluminium.
Aluminium cechy, właściwości i zastosowanie
Gęstość 2,7g/cm3-3xmniejsza niż gęst. Fe. metal lekki, dobre przewodnictwo cieplne temp top. 660st. Wytrzymałość czystego Al.=70-120 Mpa, granica elastyczności=20-40Mpa, twardość 15-30HB-może być zwiększona przez zgniot, Al. na powietrzu pokrywa się cienką warstwą tlenku, która chroni przed dalszym utlenianiem, odporne na działanie wody, wielu kwasów org .i zw. Azotu. Nie jest odp. na działanie wodorotlenków, niektórych kwasów i wody morskiej. Zastosowanie na przewodniki elektryczne, AW-Al. 99,99%-aparatura chemiczna i folia kondensatorowa; AW-Al. 99,8%-folie do opakowań żywności, powłoki kablowe i do platerowania; AW-Al. 99,5%-przewody elektryczne
Wpływ dodatków stopowych na własności Al.:
Stopy Al. po odpowiedniej obróbce cieplnej osiągają wytrzymałość kilkakrotnie większą od czystego Al. Dzięki małej gęstości stopy Al. cechują się korzystnym parametrem konstrukcyjnym Rm/gęst. W niektórych przypadkach Rm jest większa od stali. Stopy te mają małą wytrzymałość zmęczeniową. Ulegają zmęczeniu nawet przy niskich naprężeniach.
Zawartość aluminium w skorupie ziemskiej – 7,48%. Po tlenie i krzemie, trzeci najbardziej rozpowszechniony pierwiastek.
Duża aktywność chemiczna (linia Al2O3 leży najniżej na wykresie E-R) powoduje, że nie występuje w postaci związków metalicznych => składnik minerałów skałotwórzczych.
Do celów technicznych stosuje się niewielką ilość minerałów – rud.
Za rudę aluminium uważa się minerał, który:
-         Wykazuje dostatecznie dużą zawartość tlenku aluminium
-         Znajduje się w zasobnym złożu
-         Umożliwia łatwe uzyskanie metalu o odpowiedniej czystości w procesie technologicznym. Z tego powodu, pod uwagę bierze się: boksyty, nefeliny i kaoliny.
 Otrzymywanie tlenku aluminium z boksytów.Etapy:Otrzymywanie możliwie czystego tlenku aluminium-         Elektroliza tlenku aluminium
-         Rafinacja aluminium i usunięcie zanieczyszczeń stałych i gazowych.
Â
Metody otrzymywania tlenku aluminium z boksytów. Dzieli się na:
-         Kwaśne
-Â Â Â Â Â Â Â Â Â Zasadowe (metoda Bayera, metoda spiekania boksytu z sodÄ… i wapieniem)
W obu tych metodach dąży się do otrzymania rozpuszczalnego NaAlO2 => przez hydrolizę, z roztworu wydziela się Al(OH)3 => przez wyprażenie Al(OH)3 uzyskuje się Al2O3
Â
Otrzymany Al2O3 poddaje się elektrolizie w wannach elektrolitycznych, gdzie otrzymuje się ciekłe, tzw.: aluminium hutnicze (98-99% + Fe, Cu, Ti, Ca, Mg, Mn, H).
Rafinacja ma na celu oczyszczenie otrzymanego aluminium z domieszek i otrzymanie nawet 99,998% Al.
Metoda Bayera:
Â
Metoda spiekaniaÂ
Â
Â
14. Wpływ składników stopowych na właściwości odlewnicze stopów aluminium
Si – krzemMaksymalna rozpuszczalność: 1,55% w temperaturze 567 °C
-         Do 13% - ↑R, ↑HB
-         Powyżej 13% - ↓A5, ↓R, ↑HB
-         Skurcz Al.-Si około 1% - skupiona jama skurczowa.
Odpowiednie właściwości wytrzymałościowe daje modyfikacja – rozdrobnienie Si w mikrostrukturze. Modyfikacja powoduje poprawienie:Lejności,właściwości ślizgowych,zwiększa odporność na korozję
Stopy:
-Â Â Â Â Â Â Â Â Â podeutektyczne: AK7, AK9
-         okołoeutektyczne: AK11, AK12 (eutektyka 11,7%)
-Â Â Â Â Â Â Â Â Â nadeutektyczne: AK20
Cu - miedźCu z Al – tworzy roztwór stały ciekły => nieograniczona rozpuszczalność.
Cu powoduje:
-         ↑R, ↑HB, ↓A. Maksimum R przy 3,5-5% Cu
-         wzrost skurczu do 1,4% - ↑ naprężeń, skłonność do pęknięć na gorąco
-         obniża odporność na korozję – stopy odporne na korozję Cu<0,05%
Po przekroczeniu 5,5% w zależności od szybkiego chłodzenia w mikrostrukturze pojawia się faza międzymetaliczna CuAl2 - ↓A, ↓R Faza ta skupia się na granicach ziarn.
Stopy – AM4, AM5
Ti – tytanTi powoduje (<0,2%):
-         stworzenie drobnoziarnistej struktury - ↑R
-         ↑ odporności na korozję
-         ↓ skłonności do pęknięć na gorąco
Â
Wprowadzenie 0,05% Ti powoduje rozdrobnienie Al2Cu. Ti wprowadzany jest w postaci zaprawy: AlTi5, AlTi5B1
Mg – magnezMg z Al – tworzy roztwór stały. AlSi + Mg daje możliwość przeprowadzania obróbki cieplnej.
Mg powoduje:
-         znaczące ↑ odporności na korozję. Jeśli zostanie przekroczona rozpuszczalność Mg, na granicach ziarn powstaje faza międzymetaliczna Al3Mg2. powoduje to: ↓ odporności na korozję, ↓R oraz ↓A
-         uniemożliwienie rafinacji stopu przy użyciu N2 – powstawanie azotków magnezu.
Mn – mangan
Zawartość Mn < 0,5%
Mn powoduje:
-                     eliminację wpływu Fe
-                     tworzenie faz międzymetalicznych AlSiFeMn
-                     ↑ odporności na korozję – powstaje MnO
Ni – nikiel
Ni powoduje:
-         ↑ właściwości mechanicznych oraz utrzymanie ich w podwyższonych T
16. Klasyfikacja odlewniczych stopów aluminium
Â
Stopy aluminium dzieli siÄ™ na:
-         dwuskładnikowe: AlSi, AlCu, AlMg, AlZn
-         trójskładnikowe: AlSiCu
AlSi – najliczniejsza grupa stopów aluminium:
-Â Â Â Â Â Â Â Â Â niski skurcz;
-         doskonałą lejność
-         dobre odwzorowanie wnęki formy
-         nie wykazują skłonności do pęknięć na gorąco
-         tworzą skupioną jamę skurczową tym bardzie, im skład jest bliżej eutektyki
-         niski współczynnik rozszerzalności cieplnej
-         dobra odporność korozyjna – tworzenie się warstewki Al2O3 która zapobiega dalszej korozji
-Â Â Â Â Â Â Â Â Â spawalne
-         nie modyfikowane ustępują innym stopom pod kątem wytrzymałości
3 grupy:
-         Grupa I – podeutektyczne: AK7, AK9 – do odlewów o skomplikowanych kształtach, do różnych form (wilgotne, suche, kokile)
-         Grupa II – około eutektyczne: AK11, AK12+Mg – wysoka lejność, tworzą skupioną jamę skurczową, odporne na korozję w wodzie morskiej, dobra szczelność.
-         Grupa III – nadeutektyczne: AK20 – do form metalowych.
AlCu – Temperatura zalewania 710°C, eutektyka przy 33%:-         Wysoka wytrzymałość
-         Powstają pęknięcia na gorąco – przyczyny: duży zakres krzepnięcia (110K) wtrącenia CuAl2, naprężenia – skurcz.
-         Nie za dobre właściwości odlewnicze
-         Niższa odporność na korozję od AlSi
-         Wyższy skurcz od AlSi
-         Po przekroczeniu 5% Cu – spadek R, tworzenie się rozproszonej jamy skurczowej
-         W celu poprawienia właściwości stosuje się przesycanie i starzenie
-         Zalewany z jak najniższej temperatury
Dwa gatunki: AM5 oraz AM4+Ti/Mg
AlMg - :
-                     Wysokie właściwości mechaniczne
-                     Największa odporność na korozję
-                     Gorsze właściwości odlewnicze
-                     Skłonność do utleniania i tworzenia zażużleń
-                     Bardzo wrażliwe na zanieczyszczenia Fe, Cu, Si – fazy miedzy międzymetaliczne – pogarszają się właściwości antykorozyjne
-                     Mogą przenosić obciążenia dynamiczne.
-                     0,005% Be obniża utlenianie
Dwa gatunki: AG10 oraz AG51 => AlMg5Si1
Temperatura zalewania 710-740°C
Nie rafinuje siÄ™ azotem.
AlZn - :
-                     Wysokie R – wyższe od AlSi
-Â Â Â Â Â Â Â Â Â Â Â Â Â Â Â Â Â Â Â Â Â ...