Twoim problemem jest to, że powszechną NICOŚĆ mylisz z osobistą PUSTKĄ
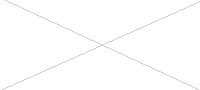
Aluminium –mały ciężar właściwy, odporność na korozje, pokrywa się warstwą tlenku tzw pasywacja chroniącą
przed dalsza korozją, sieć krystaliczna A1,
Stopy aluminium Mają wysoki wskaźnik własności wytrzymałościowych odniesionych do gęstości.
Stosunkowo niewielkie własności wytrzymałościowe aluminium można zwiększyć – nawet kilkakrotnie – przez
wprowadzenie pierwiastków stopowych oraz obróbkę cieplną stopów. W porównaniu ze stalami stopy
aluminiowe charakteryzują się znacznie mniejszą masą, a w niskiej temperaturze – większą udarnością.
Najogólniej stopy aluminium dzieli się na: odlewnicze i do obróbki plastycznej. Odlewnicze stopy aluminium są
przeważnie stopami wieloskładnikowymi o dużym stężeniu – od 5 do 25% – pierwiastków stopowych, głównie
Cu, Si, Mg i Ni lub ich różnych zestawień. Charakteryzują się dobrą lejnością i często małym skurczem
odlewniczym. Stopy do obróbki plastycznej zawierają znacznie mniej, bo ok. 5%, pierwiastków stopowych,
zwykle Cu, Mg, Mn, niekiedy także Si, Zn, Ni, Cr, Ti lub Li. Niektóre z tych stopów są po wyżarzaniu
rekrystalizującym, a część jest poddawana obróbce cieplnej polegającej na utwardzaniu wydzielinowym.
Stopy aluminium z krzemem (Siluminy) (Stopy odlewnicze)
- dobre własności odlewnicze (nie wykazują skłonności do pękania na gorąco)
- mały skurcz odlewniczy
- duża rzadkopłynność (umożliwia wykonanie cienkich wyrobów)
- jako stopy eutektyczne krzepną w stałej temperaturze, nie wykazując przy tym skłonności do segregacji
- dobra odporność na korozję pod warunkiem że nie mają dużej zawartości zanieczyszczeń, zwłaszcza żelaza
- odporne na działanie wody morskiej, wód mineralnych, a nawet sodu, amoniaku i kwasu azotowego, stężonego i rozcieńczonego
- dobre własności mechaniczne, które można jeszcze znacznie zwiększyć na drodze umacniania wydzieleniowego o ile stop zawiera dodatek Mg lub Cu
Duraluminium, wieloskładnikowy stop aluminium, oraz: miedzi (2.0-4.9 %), magnezu (0.15-1.8 %),
manganu (0.3-1.0 %) z domieszkami krzemu i żelaza, przeznaczony do obróbki plastycznej.
Duraluminium charakteryzuje się dobrymi własnościami mechanicznymi przy stosunkowo małym ciężarze
właściwym (2,8 g/cm3) oraz dużą odpornością na korozję. Wykorzystywany jest głównie w przemysłach:
lotniczym, samochodowym i chemicznym.
Miedź – dobra odporność na korozje, na powietrzu pokrywa się zasadowym węglem miedzi który chroni przed
dalsza korozją (patyna), dobre własności plastyczne, idealnie przewodzi ciepło i prąd, zdolność tworzenia
stopów: mosiądze, miedzionikle, brązy.
Stopy Miedzi :
Mosiądze stop miedzi i cynku, zawierający do 40% cynku:
- Mosiądze jednofazowe – zawierają do 32% Zn
zbudowane są z ziaren tylko jednej fazy α. Grupa mosiądzów o bardzo dobrych własnościach plastycznych,
dlatego też przerabia się je plastycznie na zimno.
Stosowane w przemyśle motoryzacyjny, na rury, odkuwki, do 15%Zn noszą nazwę tombaku używane w
przemyśle jubilerskim, mosiądz łuskowy używany do wyrobu łusek.
- Mosiądze przejściowe – zawierają 32-39% Zn
W zależności od obróbki cieplnej mogą mieć strukturę jednofazową α lub dwufazową α + β. Obecność fazy β w
strukturze mosiądzu powoduje wyraźny wzrost jego wytrzymałości.
- Mosiądze dwufazowe – zawierają 39-44% Zn
W strukturze obok fazy α pojawia się faza β. Faza β w temperaturze pokojowej wykazuje znacznie mniejszą
plastyczność zaś większą przy temperaturze powyżej 500oC, dlatego też mosiądze te przerabia się plastycznie na
gorąco. Ich zaletą jest ułatwiona obróbka skrawaniem po przez tworzenie kruchego wióra, stosuje się na odlewy
części maszyn i armaturę.
- Mosiądze wysokoniklowe zwane również nowymi srebrami, to mosiądze wieloskładnikowe zawierające nikiel
(11-19%) i cynk (20-27%). Mają srebrzystą barwę, bardzo plastyczne, duża odporność na działanie atmosfery,
małe przewodnictwo cieplne i duża oporność elektryczna.
Miedzionikle – stopy miedzi i niklu, które mogą zawierać także takie dodatki
stopowe jak krzem, żelazo, aluminium lub mangan. Miedzionikle charakteryzują się
dobrą wytrzymałością, żaroodpornością i odpornością na korozję. Miedzionikle posiadają dobre własności
oporowe. Wytwarza się z nich np. monety
Brązy stopy miedzi (80–90%) z cyną:
Brązy cynowe – zawartość cyny do 9%, stosowane do wykonywania elementów trudno ścieralnych(np.
sprężyny), w stanie obrobionym plastycznie na zimno mają dobre właściwości mechaniczne, stosowane w
przemyśle chemicznym, okrętowym, papierniczym.
Brązy berylowe – zawartość berylu do ok. 2%, posiadają najwyższe własności mechaniczne, można je
poddawać obróbce plastycznej na zimno i gorąco, mają dużą przewodność cieplną i elektryczną. Stosowane do
aparatury chemicznej, elementów żaroodpornych.
Brązy krzemowe – zawartość krzemu do 3,5%, do obróbki plastycznej stosowane na elementy aparatury w
przemyśle maszynowym, chemicznym (sprężyny,łozyska), odlewnicze stosowane na panewki, wirniki pomp,
wadą jest duży skurcz odlewniczy.
Brązy aluminiowe – zawartość aluminium do 11%, dobre właściwości wytrzymałościowe i plastyczne, odporne
na korozje i żaroodporne, stosowane jako materiały do przeróbki plastycznej jak i stopy odlewnicze.
Stale stopowe ze względu na zastosowanie dzielimy na:
Stale konstrukcyjne:
• Stale ogólnego przeznaczenia – do wyrobu części maszyn i konstrukcji, są to stale o małych i średnich
zawartościach węgla i niskostopowe, w których ogólna zawartość pierwiastków stopowych nie przekracza na ogół kilku procent
• Stale niskostopowe o podwyższonej wytrzymałości - zastosowanie: konstrukcje przemysłowe spawane, mosty, statki, do zbrojenia betonu
• Stale konstrukcyjne do ulepszania cieplnego - zastosowanie: części maszyn, pojazdów i konstrukcji
(40Cr4; 36CrNiMo4-4-2)
• Stale do nawęglania zastosowanie: części maszyn o wysokiej twardości i ciągliwym rdzeniu; stężenie węgla nie przekracza 0,25% C, ponadto zawierają Mn, Cr, Ni, Mo, po nawęglaniu stosujemy hartowanie i niskie odpuszczanie (15Cr3; 15CrMnMo4-4-1)
• Stale do azotowania - zastosowanie: części maszyn o wysokiej twardości i zwiększonej odporności korozyjnej powierzchni oraz dużej wytrzymałości rdzenia ponieważ azotowanie prowadzimy przy temp. 550oC dlatego przed tym zbiegiem stale poddaje się ulepszaniu cieplnemu tj. hartowanie i wysokie odpuszczanie, gdyż azotowana stal nie ulega już dalszemu mięknięciu (38CrAlMo6-9-2)
• Stale sprężynowe - zastosowanie: sprężyny, resory, drążki skrętne
powinny mieć wysoką granicę sprężystości i wysoką wytrzymałość zmęczeniową,
są to stale o większych zawartościach węgla z pierwiastkami silnie utwardzającymi
ferryt np.. Si, Mn (50Si2)
• Stale na łożyska toczne - zastosowanie: pierścienie, kulki, wałeczki łożysk tocznych (100Cr6)
• Stale do pracy przy obniżonych temperaturach - zastosowanie: zbiorniki na ciekłe gazy, konstrukcje i rury pracujące przy obniżonych
temperaturach
• Stale do pracy przy podwyższonych temperaturach
zastosowanie: sprężyny, resory, drążki skrętne
są to niskowęglowe stale zawierające dodatek Cr, Mo, które utrudniają zjawisko
pełzania materiału (16Mo3; 20CrMo4-5)
Stale narzędziowe – które powinny cechować się duża twardością, większą od obrabianego materiału.
Zawierają na ogół większe ilości węgla
i pierwiastków stopowych, własności nadaje się im przez hartowanie
i odpuszczanie,
• Stale do pracy na zimno
– narzędzia wykonane z tych stali nie powinny się nagrzewać powyżej 250oC,
– obróbka cieplna tych stali polega na ich zahartowaniu w wodzie lub oleju i
następnym odpuszczaniu przy temperaturze 100-250oC
– stale o małej zawartości %C z dodatkami Cr, W i Si wykazują zwiększoną
ciągliwość, stąd zastosowanie na narzędzia narażone na udarowe działanie
obciążeń
– stale średniowęglowe wysokochromowe są odporne na korozję (narzędzia
chirurgiczne),
– stale niskowęglowe przeznaczone są do nawęglania, przez co narzędzie uzyskuje
twardą warstwę wierzchnią i miękki, ciągliwy rdzeń
• Stale do pracy na gorąco
– stosowane na narzędzia pracujące w temperaturach od 250-700oC (narzędzia
kuźnicze, noże do cięcia na gorąco, matryce pras kuźniczych, formy do
odlewania pod ciśnieniem).
– stale te zawierają od 0.3-0.6 %C oraz Cr, W, Mo i V,
– narzędzia z tych stali narażone są nie tylko na ścieranie ale również na
odpuszczające działanie ciepła
– powinny mieć dobre przewodnictwo cieplne i odporność na zmęczenie cieplne
wywołane cyklicznym nagrzewanie i chłodzeniem
– powinny też mieć dobrą odporność na pękanie
• Stale szybkotnące
– stosuje się na narzędzia do skrawania materiałów z dużymi prędkościami
– mogą pracować bez utraty twardości przy 550-600oC
– ich wysoka twardość i odporność na odpuszczające działanie ciepła jest
wynikiem wystąpienia efektu twardości wtórnej po odpuszczaniu przy
ok. 560oC
– Zawierają 08-1,4 %C, do 19% W, do 10% Mo, do 5% V, do 10% Co,
ok. 4% Cr,
– obróbka cieplna polega na zahartowaniu od 1200oC – 1270oC w oleju lub
w powietrzu i odpuszczaniu przy ok. 560oC na maximum twardości wtórnej
Stale i stopy o szczególnych własnościach – do tej grupy zalicza się stopy o najbardziej
zróżnicowanym zastosowaniu, z tym samym własnościach. Grupę tych stali stanowią stale o
własnościach fizycznych, chemicznych lub mechanicznych decydujących o ich zastosowaniu.
Stężenie pierwiastków stopowych w tych stopach może przekraczać 50% (stopy specjalne), gdy Fe nie
jest głównym składnikiem mówimy wówczas
o nadstopach.
Stale o szczególnych własnościach możemy podzielić na stale:
• odporne na korozję,
• żaroodporne i żarowytrzymałe,
• odporne na ścieranie,
• do utwardzania powierzchniowego
• stopy o szczególnych własnościach magnetycznych,
• stopy o złożonej rozszerzalności cieplnej i wł. Sprężystych
Nawęglanie polega na nasyceniu węglem wierzchnich warstw części wykonywanych ze stali
niskowęglowych. Uzyskanie twardej, odpornej na ścieranie warstwy przy zachowaniu ciągliwego
rdzenia.
Sposób wykonania nawęglania: nagrzewanie niskowęglowej stali w odpowiednim ośrodku
nawęglającym gazowym lub stałym (nawęglanie w proszkach) do temperatury powyżej Ac3 (780°C),
wytrzymywanie przez czas wystarczający do uzyskania żądanej grubości warstwy nawęglonej z
następnym powolnym chłodzeniem.
Temperatura nawęglania: 850-950ºC, czas 2-8 h.
Stale do nawęglania – do ok. 0,25%C, węglowe i niskostopowe z chromem, niklem, molibdenem pierwiastkami poprawiającymi hartowność stali.
Azotowanie stali polega na nasyceniu warstwy wierzchniej N, w wyniku czego uzyskuje się dużą
twardość i odporność na zmęczenie. Tak dużą twardość można jednakże osiągnąć tylko na specjalnych
stalach do azotowania zawierających Cr, Mo i Al. Ponieważ azotowanie przeprowadza się w niezbyt
wysokiej temperaturze, stal uprzednio poddaje się ulepszaniu. Stosuje się atmosferę zdysocjowanego
amoniaku, w której występują aktywne atomy azotu. W wyniku tego następuje ich dyfuzja oraz
tworzenie się azotków pierwiastków stopowych i żelaza. Obecność węgla w stalach utrudnia proces
azotowania. Wobec tego stale wysokowęglowe nie nadają się do azotowania, a stale niskowęglowe,
mimo iż nadają się, są rzadko stosowane ze względu na stosunkowo niskie własności
wytrzymałościowe rdzenia.
Węgloazotowanie i azotonawęglanie stali
Polega na nasyceniu powierzchni przedmiotów stalowych jednocześnie węglem i azotem w
temperaturze 750-950°C (węgloazotowanie) i azotonawęglanie (450-650 °C). Po zahartowaniu i
odpuszczeniu zyskuje się twardą i odporną na ścieranie warstwę powierzchniową. W zależności od
rodzaju ośrodka wydzielającego węgiel i azot rozróżnia się procesy węgloazotowania kąpielowego
(cyjanowania) lub gazowego (wprowadza się amoniak).
Zaletami węgloazotowania kąpielowego są: skrócenie czasu procesu w stosunku do czasu nawęglania,
uzyskanie bardzo twardych powłok odpornych na ścieranie, stosunkowo niska temperatura procesu.
Wadami węgloazotowania kąpielowego są: niebezpieczeństwo zatrucia pracowników parami soli
cyjanowych oraz konieczność częstego kontrolowania składu kąpieli. Węgloazotowanie gazowe eliminuje wadę węgloazotowania kąpielowego związaną z możliwością
zatrucia, przy zachowaniu niemal identycznego efektu końcowego obróbki.
Hartowność stali – zdolność do tworzenia w trakcie hartowania struktury martenzytycznej.
Głównym czynnikiem wpływającym na hartowność stali jest jej skład chemiczny, czyli zawartość węgla oraz
pierwiastków stopowych i technologicznych. Poza składem chemicznym wpływ na hartowność mają także
wielkość ziarna i jednorodność austenitu oraz obecność innych, nierozpuszczonych cząstek. Dodatki stopowe,
zwiększają hartowność stali poprzez zmniejszenie krytycznej szybkości chłodzenia. Krytyczna szybkość
chłodzenia, czyli najmniejsza szybkość chłodzenia pozwalająca na uzyskanie struktury martenzytycznej. Wyższa
hartowność pozwala na zastosowanie mniejszych szybkości chłodzenia (hartowanie w oleju), unikając w ten
sposób naprężeń hartowniczych.
Miary hartowności:
Miarą hartowności jest grubość warstwy martenzytycznej na przekroju hartowanego przedmiotu. W praktyce ocenę hartowności przeprowadza się w oparciu o tzw.średnicę krytyczną, tj. przy której po zahartowaniu uzyskuje się w osiowej części przekroju strukturę o określonej zawartości martenzytu, lecz nie mniejszej od 50%. Średnica krytyczna dla danego gatunku stali jest zależna między innymi od rodzaju ośrodka chłodzącego i im wolniej chłodzi ośrodek tym mniejsza jestśrednica krytyczna.
Struktura krystaliczna, w strukturach krystalicznych atomy są ułożone w periodycznie powtarzających się odstępach w co najmniej 3 nierównoległych kierunkach. Do opisu struktury wybiera się najprostszy element, zwany komórką elementarną. Długości krawędzi są nazywane stałymi sieciowymi lub parametrami sieciowymi. Powtarzanie komórki w trzech wymiarach generuje strukturę krystaliczną.
Defekty sieci krystalicznej, niedoskonałości w ułożeniu atomów nazywamy defektami sieciowymi:
- Defekty punktowe — to wakanse (luki) i atomy międzywęzłowe, Wakans to brak atomu w węźle sieci
krystalicznej. W danej temperaturze istnieje zawsze określona liczba wakansów. Defekty te powstają w
wyniku drgań sieci o amplitudzie wzrastającej z temperaturą, które powodują wypadanie pewnej liczby
atomów ze swoich położeń równowagi. Tworzy się zawsze para defektów atom międzywęzłowy
(wytrącony) — wakans. W modelu Frenkla atom z węzła sieci zajmuje położenie międzywęzłowe,
natomiast w modelu Schottky`ego dokonuje on wyjścia na swobodną powierzchnię kryształu.
Inne defekty punktowe to atomy obcych pierwiastków, które mogą zajmować położenia węzłow (atomy
substytucyjne) lub międzywęzłowe
- Defekty liniowe – to dyslokacje: krawędziowe, śrubowe i mieszane:
- krawędziowa – Powstaje przez wprowadzenie w kryształ dodatkowej płaszczyzny. Cechą
charakterystyczną dyslokacji jest duże odkształcenie sieci, co jest spowodowane dążeniem atomów
sąsiadujących z linią dyslokacji do dostosowania swych położeń do warunków wytworzonych przez
brak płaszczyzny. Dyslokacja krawędziowa ma wektor Burgersa prostopadły do linii dyslokacji
- śrubowa - defekt liniowy struktury krystalicznej spowodowany przemieszczeniem części kryształu
wokół osi, zwanej linią dyslokacji śrubowej. Dyslokacja śrubowa ma w. Burgersa równoległy do linii dyslokacji.
- mieszana – suma dyslok. Krawędz. I śrubow.
- Defekty powierzchniowe - granice ziarn – w obrębie granicy obserwujemy na ogół chaotyczny rozkład atomów spowodowany
nagromadzeniem się tam dyslokacji i defektów punktowych. Rozróżniamy granice szerokokątową i
wąskokątową.
Mechanizmy umocnienia:
Roztworowe – polega na wprowadzeniu do sieci krystalicznej obcych atomów o średnicach różnych od
atomów rodzimych sieci. Naprężenia wprowadzane w ten sposób powodują opór ruchu dyslokacji.
Mechanizm skuteczny ale trudno uzyskuje się większe efekty ze względu na ograniczoną rozpuszczalność
pierwiastków. Duży efekt umocnienia uzyskuje się przy wykorzystaniu przemiany martenzytycznej
Dyslokacyjne - czynnikiem decydującym o umocnieniu materiału jest wzrost gęstości dyslokacji.
Mechanizm skuteczny w wyrobach przerabianych plastycznie. Podczas eksploatacji temperatura nie może
wzrosnąć powyżej 0.3 Tt.
Wydzieleniowe - metoda obróbki cieplnej metali prowadząca w efekcie do zwiększenia ich wytrzymałości
mechanicznej. Mechanizm wykorzystywany w stopach w których rozpuszczalność domieszki maleje ze
obniżaniem temperatury a wydzielane cząstki są koherentne lub częściowo koherentne z osnową i
...