Twoim problemem jest to, że powszechną NICOŚĆ mylisz z osobistą PUSTKĄ
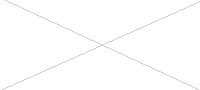
SPAJANIE - łączenie dwóch elementów w sposób trwały, nierozłączny. Rozróżniamy takie technologie jak:
spawanie, zgrzewanie, lutowanie, klejenie. Połączenia spajane należą do spoczynkowych,
nierozłącznych połączeń bezpośrednich, w których powstają siły spójności na powierzchni styku łączonych części. W miejscu styku powierzchnia ulega zanikowi i następuje scalanie materiału. Tą metodą można łączyć wszystkie tworzywa, metale, szkło, tworzywa sztuczne. Spawanie jest to proces, podczas którego łączenie następuje wskutek stopienia, a następnie skrzepnięcia ciekłego metalu.
1. Gazowe
2. Elektryczne: a)żuźlowe
b)łukowe
ad.b.
- elektrodą nietopliwą w osnowie gazów obojętnych
- elektrodą topliwą: elektrodą otuloną, łukiem krytym, w osnowie gazów aktywnych, w osłonie gazów obojętnych)
3. Termitowe
4. Elektronowe
5. Plazmowe
6. Laserowe.
Spawanie tworzyw
sztucznych:
Wykorzystujemy rozgrzane powietrze (elektrycznie lub przez palnik acetylenowy). Tworzywa sztuczne możemy nanosić na inne tworzywa np. na metale.
1.Nanoszenie fluidyzacyjne -powłoka z tworzywa sztucznego jest dość trwała
2.Nanoszenie
elektrostatyczne: materiał o przekroju kołowym typu rura. Ładowanie cząstek tworzywa ładunkami elektrycznymi i nanoszenie ładunków na powierzchnię elementu (gł. elementy tego procesu). Element wcześniej się podgrzewa.
Urządzenia do nanoszenia elektrostatycznego składają się z dyszy, wewnątrz której znajduje się głowica, przez którą przepływa tworzywo ze sprężonym powietrzem. Dookoła dyszy znajdują się dysze płomieniowe, przez które dostarczany jest gaz palny. Dysze płomieniowe wytwarzają pole o wysokiej temp., w którym tworzywo ulega stopieniu. Na powierzchnie spadają stopione krople tworzywa.
SPAWANIE ELEKTRYCZNE łukowe:
Rodzaje złącz spawanych:
l.Doczołowe 2.Teowe 3 .Zakładkowe 4 .Narożne 5.Krzyżowe 6-Kątowe 7.Przylgowe
Rodzaje spoin:
1.Czołowe - łączą ze sobą brzegi blach, które są ułożone względem siebie równolegle lub prostopadle
2.Pachwinowe - spoinę pachwinową stanowi trójkąt składający się z jednego lub większej liczby warstw ułożonych między prostopadłymi płaszczyznami łączonych elementów. Grubość spoiny pachwinowej jednostronnej (wklęsła) nie powinna przekraczać 0,7 grubości cieńszego materiału spawanego, a w spoinie dwustronnej (płaska, wypukła) 0,5 grubości
3.Grzbietowe - przy łączeniu elementów cienkich wykonuje się spoinę bez ukosowania blach (grubości łączonych części do 3 mm)
4.0tworowe - powstają przez wypełnienie spoiwem otworu wyciętego w jednej z blach w złączu przylgowym (kołkowa -otwór okrągły, szczelinowa -kształt owalny) lub
1 .Jednowarstwowe
2 .Wielowarstwowe 3.Wielościegowe (ścieg -warstwa ułożona jednorodnym przejściem elektrody wzdłuż rowka spoiny)
Urządzenia: spawalnice prądu stałego, przetwornice, transformatory spawalnice prostownikowe. Zadaniem tych urządzeń jest zamiana prądu o wysokim U i niskim I na prąd o niskim U i wysokim I.
Łuk elektryczny -nieprzerwany strumień dodatnich i ujemnych jonów oraz elektronów przenoszących ładunek elektryczny pomiędzy (-) a (+) tj. elektrodą a przedmiotem. Częściej stosujemy biegunowość ujemną (elektroda (-), materiał (+)), bo jest korzystniejsza ze względu na ilość ciepła. Przy spawaniu używa się prądu o natężeniu 30-60A i napięciu 20-3 5 V. Temperatura łuku dochodzi do 3500° C (zależy od natężenia prądu spawania). Łuk zajarza się przez potarcie końcem elektrody o spawany przedmiot następnie unosi się elektrodę nieco w górę aby między elektrodą a przedmiotem spawanym powstała odległość nie przekraczająca średnicy drutu elektrodowego. Powstawaniu łuku towarzyszy wydzielanie dużej ilości światła i ciepła. Aby łuk mógł się zajarzyć w czasie spawania warstwa powietrza w przestrzeni łukowej musi ulec zjonizowaniu tj. musi stać się dostatecznie dobrym przewodnikiem prądu
elektrycznego. Zjonizowanie powietrza w łuku elektr. polega na tym, że w wysokiej temp. łuku cząsteczki gazów zawartych w powietrzu i gazów wydzielonych z otuliny oraz par metali rozpadają się na mniejsze, elektrycznie naładowane cząstki -elektrony i jony. Elektrony przyciągane są przez anodę (mat. spawany), a jony przez katodę (elektrodę). Jarzący się łuk staje się dobrym przewodnikiem prądu i szybko doprowadza do stopienia spawany metal.
Natężenie zależy od grubości elektrody, rodzaju elektrody, rodzaju spawanego materiału, grubości spawanego materiału, rodzaju wykonywanego połączenia, temperatury spawanego przedmiotu, pozycji spawania. Zadania otuliny: zapewnia łatwość zajarzenia łuku i stabilność jarzenia, wytwarza osłonę gazową, chroniąca spoinę przed dostępem powietrza, tworzy po stopieniu warstwę żużla, który chroni powstałą kąpiel metalu przed zbyt szybkim stygnięciem, zapewnia właściwy skład stopiwa poprzez wprowadzenie do niego uszlachetniających składników (tj. mangan, krzem, nikiel, molibden), polepsza przewodność elektryczną przestrzeni łukowej, wiąże podczas spawania szkodliwe związki tlenku i azotu i wprowadza je do żużla Składniki otuliny:
l.Stabilizujące łuk elektryczny: tlenki sodu, potasu, kreda, rutyl, tlenki manganu 2.Żuźlotwórcze:
rudy żelaza, rudy manganu, tytanu, kaolit, kreda 3-Gazotwórcze: celuloza 4.0dtleniające jeziorko:
żelazostopy, glin, węgiel 5.Uszlachetniające spoinę:
chrom, krzem, mangan, molibden, wanad i nikiel
Ze względu na pracę spoiny dzielimy: l. Nośne (przenoszą obciążenia); 2. Szczelne (muszą zapewniać szczelność); 3. Szczepne (do łączenia konstrukcji, np. barierki).
Ze względu na kształt i przekrój poprzeczny spoiny dzielimy na: czołowe, pachwinowe, krawędziowe, otworowe.
Przygotowanie elementów do spawania: l.Mechaniczne oczyszczenie; 2.Chemiczne czyszczenie; 3.Ukosowanie i wyginanie blach:
Blachy cienkie poniżej 2mm -wyginamy. Blachy 2-4mm nie wyginamy lecz rozsuwamy na odległość równą połowie ich grubości. Blachy 4-12mm
ukosujemy na V 60-90 stopni. Blachy powyżej 12mm ukosuje się na X .
Spawalność - zespół cech metalu decydujących o możliwości uzyskania spoiny o własnościach mechanicznych zbliżonych do właściwości materiału rodzimego bez dodatkowych zabiegów technologicznych. Stale do 0,25% węgla są dobrze spawalne, zaś powyżej 0,4% nie spawalne. Im więcej węgla, tym stale spawają się gorzej.
Błędy w spawaniu: brak przetopu, zbyt duże przetopienie, zażużlenie, pękanie, brak materiału w spoinie, nadmiar materiału (zgrubienie spoiny), podtopienie, przyklejenie, pory, pęcherze, przegrzanie, źle zakończone końce spoiny. Badanie połączenia spawanego: l .Oględziny zewnętrzne; 2. Prześwietlenie promieniami RTG;
3.Sprawdzanie wytrzymałości i struktury. Rodzaje elektrod:
W zależności od grubości otuliny:
l .Cienkootulone -grubość otuliny nie przekracza 20% średnicy drutu
2.Średniootulone -20%-40%
3.Grubootulone -powyżej 40%
W zależności od przeznaczenia
a) Elektrody połączeniowe do spawania konstrukcji stalowych ze stali węglowej lub stopowej, na przykład elektroda ER1.46, barwa różowa, Rm=46 kG/mm^
b) Elektrody do napawania EN. Na przykład symbol EN200B oznacza elektrodę zasadową do napawania. Twardość spoiwa około 200 HB Napoinę można obrabiać skrawaniem. Barwa jasnofioletowa.
c) Elektrody specjalne ES. Przykładowo symbol ESCrMo5 oznacza specjalną elektrodę zasadową do spawania stali chromowo-molibdenowych narażonych na temperatury od 550 stopni C, jak rurociągi na parę przegrzaną. Stopiwo zawiera 0,9% Cr oraz 0,4% Mo. Barwa czerwono-niebieska. Do spawania stali kwasoodpornych używa się elektrod o symbolu ES 18-8-2B. Barwa czerwono-niebieska. Stopiwo zawiera około 18% Cr, 8% Ni, 2% Mo. Elektrodę specjalną zasadową do napawania narzędzi stalą szybkotnącą oznacza się symbolem ENS18WB. Barwa biało-czama. Zawartość wolframu w stopiwie wynosi około 18%.
płaszczyźnie podziału i po ucięciu wypustki. Proces zależy od: l.Złożoności przekroju wyrobu przy odkuwkach zwartych;
2.0dkuwki wydłużone stosuje się matryce do kucia wstępnego, pomocniczego (międzyoperacyjne) i później matryce do kucia ostatecznego (matrycujące) posiadające rowek na wypływkę. Koszty związane są z wykonaniem narzędzi.
Naddatki technologiczne w procesach kucia matrycowego: na wykonanie odkuwki; na straty w procesach kucia (wypływka, zgorzelina, dna, kleszczowina, zimne końce przy ogrzewaniu); na straty w krajalni (odcięcia od prętów, wadliwy koniec pręta, niepodzielność pręta). Straty pozatechnologiczne (braki).
Określenie ilości materiału -na wykresie odkładamy przekrój materiału, który jest powierzchnią pręta. Rysujemy wykres zmienności przekroju i na podstawie tych wykresów otrzymujemy idealny wykres odkuwki.
WALCOWANIE jest to proces, w którym przedmiot uzyskuje zamierzony kształt w wyniku odkształcenia plastycznego materiału między obracającymi się twardymi walcami. W zależności od rozmiarów materiał może wejść między walce lub nie, zależy to od kąta (alfa) (kat uchwytu -między promieniem przechodzącym przez punkt styku materiału z walcem a prostą łączącą środki obu walców). Proste walcarki składają się z dwóch walców (układ duo) i mogą być jednokierunkowe lub zwrotne. W celu uzyskania produktu materiał należy przepuszczać między walcami kilka razy, dlatego w jednokierunkowych walcarkach duo konieczne jest podawanie walcowanego produktu na drugą stronę walcarki. Zadanie to spełnia walec główny. Walce jednokierunkowe służą do walcowania niewielkich walcówek, większe walcowane są na walcarkach duo zwrotnych (walce po przejściu materiału zmieniają kierunek obrotu). Główną wadą walcarek duo zwrotnych jest konieczność hamowania dużych mas obracających się z dużą prędkością. W układzie walców duo zwrotnych pracują walcarki stosowane do wstępnego walcowania wlewków. Są to tzw. zgniatacze wyrabiające kęsiska lub kęsy, służące
później do produkcji prętów lub kształtowników, oraz blachówki____przerabiane następnie na blachy cienkie. Umieszczenie trzeciego walca umożliwia pracę w obie strony bez konieczności zmiany kierunku obrotu walców (układ trio). W walcarkach trio materiał przechodzi najpierw między walcem górnym i środkowym, a następnie w przeciwnym kierunku - między środkowym i dolnym. Odległości między walcami można zmieniać w pewnych granicach (przesuwanie walców zewnętrznych w płaszczyźnie pionowej). Do walcowania cienkich blach stosuje się walcarki pracujące w układzie czterech walców (układ kwarto). Dwa walce środkowe o małej średnicy wykonują pracę walcowania (walce o małych średnicach umożliwiają uzyskanie dużych nacisków jednostkowych przy małych siłach dociskających). Walce robocze wspierają się na walcach oporowych o dużej średnicy, dzięki temu walce robocze nie wyginają się pod naciskiem materiału. Blachy określonej szerokości walcuje się na walcarkach uniwersalnych (układy walców w osiach poziomych i pionowych). Walcowanie specjalne (kształtowe)
można uzyskać elementy o powtarzalności wymiarów np. druty zbrojeniowe. Przeciąganie - uzyskanie drutów - narzędziem w tym procesie jest ciągadło. Wykonuje się na zimno, aby wystąpiło umocnienie materiału, wówczas mamy mały i wytrzymały element. Wyciskanie i przepychanie -stosuje się, gdy chcemy uzyskać bardzo dokładne wymiary.
WYCISKANIE dzielimy na:
współbieżne- materiał płynie w kierunku zgodnym z ruchem stempla, przeciwbieżne - materiał płynie w kierunku przeciwnym do ruchu stempla, dwukierunkowe -materiał płynie jednocześnie w kierunku zgodnym i przeciwnym do ruchu stempla, poprzeczne
materiał płynie w kierunku prostopadłym do ruchu stempla. Stosuje się w produkcji rur i prętów z materiałów nieżelaznych. Możliwość uzyskania (bezpośrednio z wlewków) kształtowników o złożonych przekrojach. Pręty wyciskane na gorąco wymagają prostowania (często skrzywione lub skręcone).
Przedmioty wyciskane na zimno charakteryzują się silnym i jednorodnym umocnieniem materiału. Powierzchnię przedmiotów o klasie chropowatości 5-7 (zależy od warunków smarowania, rodzaju użytego materiału, stanu powierzchni narzędzi). Przepychanie -siła drugiej strony odwrotna niż w przeciąganiu.
PRZECIĄGANIE
(ciągnienie) jest to obróbka plastyczna na zimno lub na gorąco, powodująca zmiany kształtu lub pola przekroju poprzecznego materiału w postaci drutu, pręta lub rury pod wpływem przeciągania go przez otwór narzędzia (ciągadła) lub między walcami. W celu uzyskania odpowiednich wymiarów należy ciągnąć materiał przez kilkanaście lub kilkadziesiąt coraz mniejszych ciągadeł.
GIĘCIE jest to proces kształtowania , przy którym zostaje zachowana prostoliniowość tworzących a promień krzywizny giętego materiału zachodzi w jednej płaszczyźnie. Rodzaje gięcia:
l. Na prasach: a) wygniatanie, b) zagniatanie, c) zwijanie; 2. ...